ICFs and efficient mid-rise design
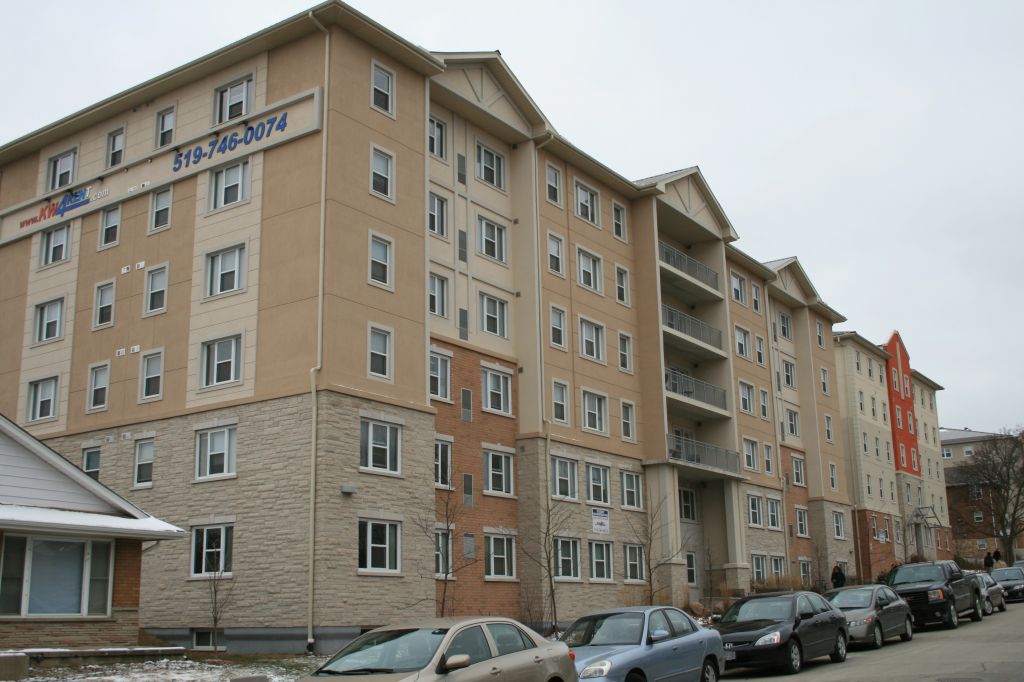
By Andy Lennox and Francis Roma
Over the last decade, something has been transforming the city of Waterloo, Ont. In a community of only 100,000, approximately 80 mid-rise student residences, apartments, and multi-family buildings have been constructed—with 40 built within an area of less than 2.5 km2 (1 mi2). Further, all these structures have used insulated concrete forms (ICFs) in their design.
Many architects, builders, and owners understand ICFs deliver a better building faster, but they may also believe the materials increase the building’s overall cost. However, Waterloo tells a different story. In a place where construction demand is high, timelines are urgent, and the weather is cold several months of the year, ICFs are being used to deliver high-performance cost-effective buildings on schedule.
Insulated concrete forms—A quick primer
ICFs are a permanent formwork system for reinforced concrete construction. The interlocking modular units are dry-stacked into position and filled with concrete. They can be used for almost any concrete wall—interior or exterior, below-grade or above-grade, short or tall.
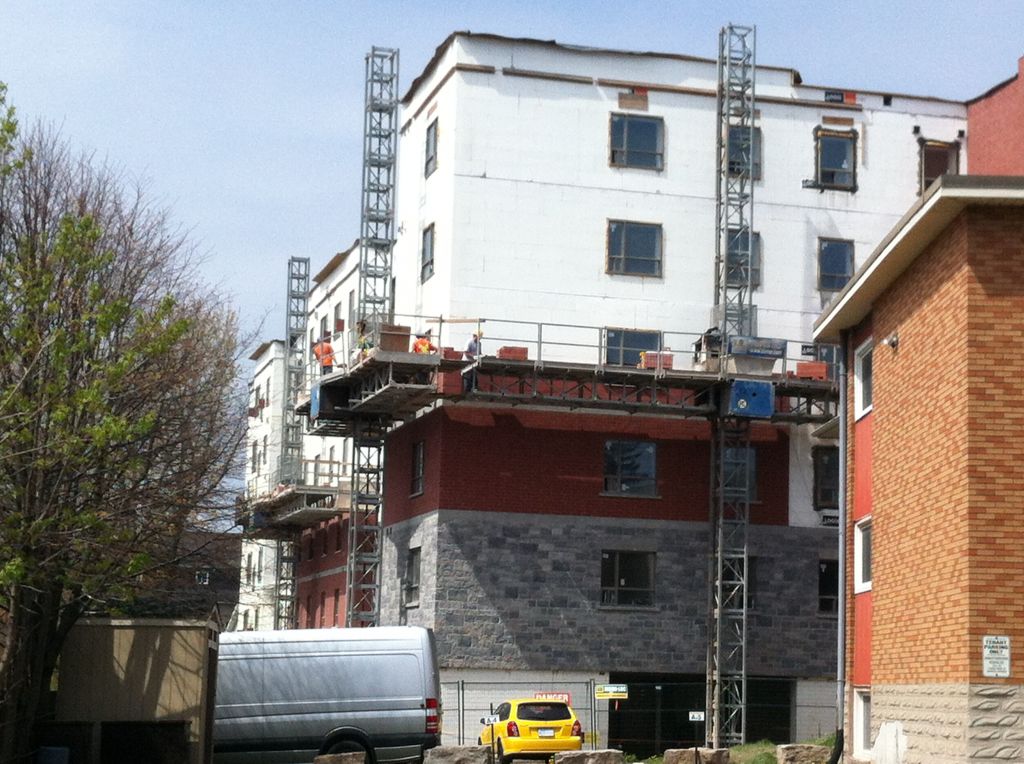
ICF construction is the successful marriage of two proven technologies: concrete and expanded polystyrene (EPS). In an ICF wall, the concrete mass is sandwiched between two layers of foam insulation.
A traditional exterior concrete wall contains six building components:
- concrete;
- reinforcement bar;
- insulation;
- air barrier;
- vapour barrier; and
- studs/strapping.
ICFs combine these six components into a single building system installed by one crew at the same time.
A more efficient building design
In mid-rise buildings ICFs are most commonly used for above-grade exterior walls. In this application, where thermal performance is important, they provide maximum impact and benefits when compared to traditional construction methods such as wood or concrete masonry unit (CMU) construction. ICFs can be used to construct a building of any shape, and they can easily accept any type of exterior wall finish acceptable for mid-rise buildings as per the various provincial fire codes.
However, ICFs are also often used for:
- frost walls;
- below-grade walls;
- parking garages;
- interior demising walls;
- shear walls;
- elevator shafts;
- fire-rated walls; and
- load-bearing walls.
Architects and engineers considering ICFs for the first time may be initially hesitant to design with a new technology.
“However, it is just like a concrete building design professionals were taught in school,” says Kurt Ruhland of Kitchener, Ont.-based MTE Consultants Inc., who have designed many ICF-built mid-rise buildings in the Waterloo area.
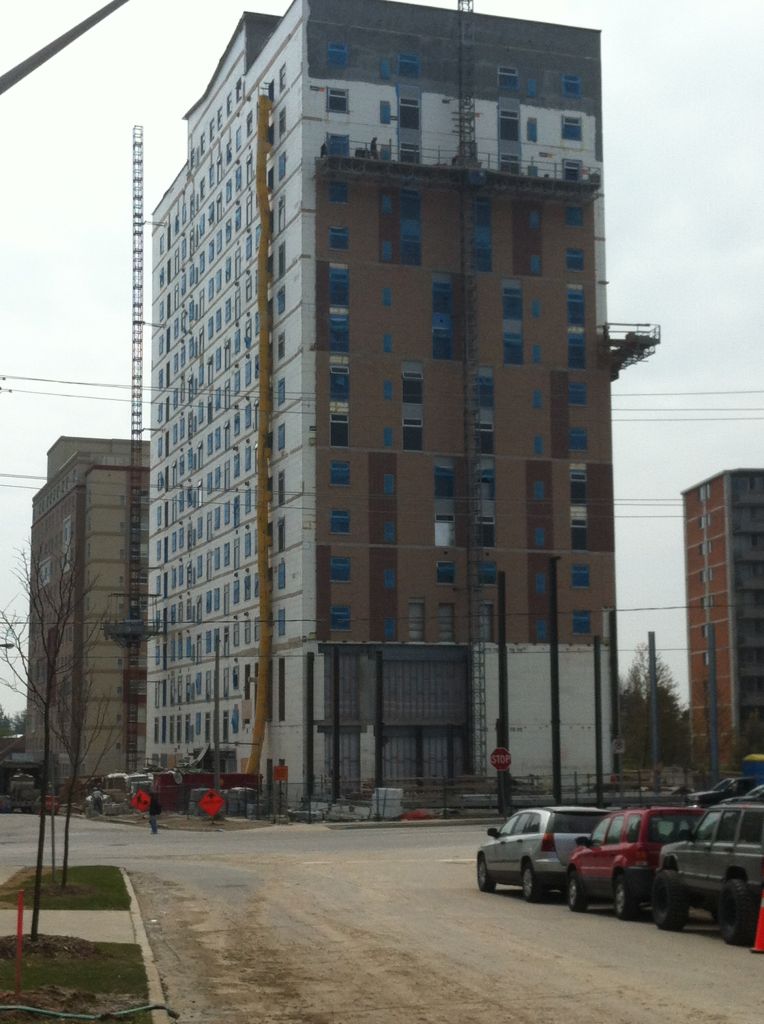
Further, given their size, function, and design requirements, ICF-built mid-rise multi-family buildings tend to have their own set of design parameters. To maximize performance and minimize buildings costs, they typically have:
- ICF exterior walls;
- precast concrete floors—usually 203 mm (8 in.); and
- ICF or masonry interior walls.
A punch-out window design is cost-effective with ICFs, and optimizes the wall-area to opening-area ratio, thereby maximizing the building’s thermal performance.
“We find ICFs to be very efficient to engineer,” says Ruhland. “When a precast concrete floor is specified in an ICF mid-rise, the structural engineers do not have to engineer the floors as they would in a cast-in-place building. We also find that an ICF mid-rise building is easier to engineer than a masonry building—there is simply much more strength capacity in the steel-reinforced ICF walls.”
Additionally, engineers do not have to be concerned with esthetic cracking with ICF mid-rise buildings as they would be with a cast-in-place building with painted exterior walls. As a result, horizontal bars with greater spacing in order to facilitate easier installation can be specified.
A specific ICF feature that also simplifies engineering is what is known as a ‘transition block.’ This allows an additional 50.8 mm (2 in.) of concrete at the top of the block.
“In a 203-mm concrete wall, that extra 50.8 mm gives us 254 mm (10 in.) of concrete to work with,” says Ruhland. “This gives us our 101.6-mm (4-in.) bearing for the precast floors and leaves another 152.4 mm (6 in.) of concrete so the vertical rebar can continue up centred in the wall, which is where we want it.”
A faster, efficient build
ICF construction is often faster than traditional construction because the building process is simple. The form’s technology combines the six building elements in one step and the process requires fewer trades. As seen in Waterloo, the walls go up quickly and easily. ICF construction can also continue during the winter and allows for fewer seasonal delays.
First, the site is prepared and the concrete footing is constructed. Then the forms are stacked, the rebar is set in place, and the walls are braced. The concrete is then poured, and finally, electricity and plumbing are roughed-in before interior and exterior finishes are adhered.
Floor slabs are typically laid as soon as seven days after a pour. Before the entire superstructure is built, interior and exterior finishes can be attached to the walls and window installation can begin. When using precast floors no shoring is necessary, which would otherwise impede the fit-and-finish sub-trades.
When a different trade is introduced into a footplate, there are increases for labour, complexity, and the potential for conflict and inefficiency increase. With ICF construction, the same crew can install the complete exterior wall system, interior walls, pre-cast floors, and windows to ‘dry-in’ the building and create the shell. Interior finishes are protected from the elements earlier, efficiency is increased, and the number of suppliers and trades that have to be managed and co-ordinated are reduced.
ICF construction is also often both less expensive and less-labour intensive. Conventional concrete construction requires the erection of temporary formwork and can be a time-consuming and demanding process with larger structures. Per the Concrete Design Handbook, the concrete must cure for 28 days at a temperature above 10 C (50 F), during which time it can be prone to be exposed to all the elements—from extreme cold to extreme heat, both of which can affect the curing process. With ICFs, the concrete is insulated as it cures and is inherently protected from extreme weather conditions.
Mid-rise buildings can be built in the winter and ICF construction offers significant savings on hoarding (i.e. building of the tents) and heating costs. If conventional construction takes place during winter, temporary tents must be built around every section of freshly poured concrete, and hot air must be blown into each tent 24 hours per day until the concrete cures sufficiently.
The hoarding and heating process is costly and repetitive. However, when building with ICFs during the winter, these hoarding and heating costs are drastically reduced or eliminated because only the concrete at the top of the ICF wall needs protection and this provides a significant cost savings.
Specific ICF features
Over the years, ICF systems have been refined and now offer advantages making them especially suitable for mid-rise multi-family construction. For example, 203-mm precast floor slabs are commonly used in such projects. A slab acceptor is a specialty block with a half-height interior foam panel that creates a space to readily accept a precast floor slab. This eliminates the need to cut away the interior panel, thus reducing waste and saving time on the job site.
In some regions, where textured acrylic veneers are desired, architects must specify an exterior drainage layer on ICF walls in order to qualify for liability insurance coverage. This can be a costly construction step as a separate foam panel usually must be mechanically bonded to the entire façade. By specifying an interior drainage layer for ICF walls, it can now be installed while the walls are being built; and the need for an additional exterior drainage layer is eliminated. As a bonus, this type of system also provides additional R-value to the insulation (i.e. R-8 is R-value of the interior drainage layer) and can bring the total R-value of the exterior walls to R-30 or greater.
ICFs made with an EPS enhanced with graphite particles that act as infrared absorbers and heat reflectors are also available. ICFs made with this brand of EPS deliver approximately 15 percent more R-value without increasing the thickness of the wall.
Unassembled ICFs, also known as ‘knock-down forms,’ can be fully compatible and interchangeable with solid pre-assembled forms. Unassembled forms are typically used to build around complex and heavy rebar patterns, and pre-assembled forms are typically used where the rebar patterns are lighter. Thus, integrating assembled forms and unassembled forms saves time and money on the jobsite.
Forms are now available with incremental corner support and additional interior and exterior fastening surfaces. Corners are typically the weakest point in an ICF wall due to the concrete forces coming from two directions. ‘Blow-outs’ are repairable and uncommon, however they get more time-consuming to repair as you build farther from the ground. Pre-formed reinforced corners offer affordable insurance as a building grows taller. Pre-formed reinforced ICF corners are often available in 90- and 45-degree angles.
Bracing is an integral element in the successful erection of ICF walls. There are many bracing systems designed for regular, tall-wall, and high-rise ICF construction. In most cases, conventional ICF bracing systems brace from the structure’s interior, are mechanically fastened to the ICFs furring strips, and can efficiently align walls up to approximately 6.2 m (20 ft) high.
Implementation and support to the construction team
“The key is in the details—for instance, how to fasten brick ties to the walls or keeping walls plumb,” Ruhland notes.
Thus, certain ICF manufactures provide extensive design and estimating resources to architects and engineers aiding in effective cost-estimation and project implementation.
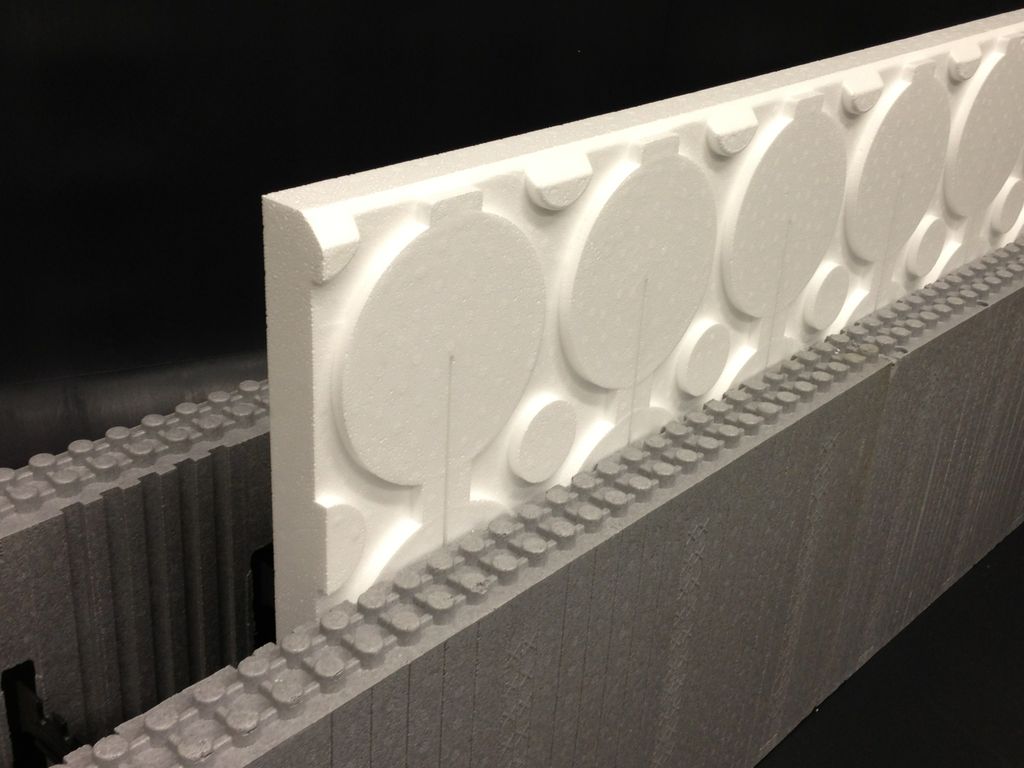
Since accurate technical drawings are critical to successful integration, some ICF manufacturers provide various tools allowing the architect, engineer, and computer-aided design (CAD) technician to insert ICF components into working drawings. These solutions simplify the construction documentation process, and reduce perceived risk associated with using ICFs for the first time.
Full-service ICF manufacturers also provide shop drawing services and technical advisors to assist in creating accurate specifications and resolving building details.
Architects and owners also need access to a network of builders trained in ICF best practices and experienced with using the products. Certain manufacturers provide a database of such experienced companies across Canada; and also provide support to builders by offering both classroom and job site training. These courses educate builders on tool requirements, various forms and features available, and general best practices for ICF construction. Some ICF companies offer advanced training courses specifically focused on mid-rise construction.
A better building
ICF mid-rise buildings are energy-efficient and sustainable. They deliver ongoing energy savings for building occupants and owners, have less of an impact on the community, less risk related to fire or natural disaster, because ICF walls typically carry a sound transmission class (STC) rating of 50 or more, and provide increased occupant comfort due to diminished sound transfer from the outside or from adjacent units. ICF mid-rise buildings are energy-efficient simply because they are air-tight and built with high-mass concrete walls sandwiched between two continuous foam insulation layers.
According to the study “Energy Consumption of Concrete Homes versus Wood Frame Homes” by Pieter VanderWerf, PhD (of Boston University), ICF exterior walls reduce energy consumption for heating by 44 per cent and for cooling by about 32 per cent, on average, versus a framed wall.1
Since the insulation is continuous, ICF walls typically offer a much higher whole-wall effective R-value. This means there are no thermal bridges or interruptions in the building envelope that can reduce the effective thermal performance of the ICF wall assembly.
The report, “Field Monitoring of the Dynamic Heat Transmission Characteristics Through ICF Wall Assemblies Over A Full-year Cycle of Weather Exposure,” issued by the National Research Council (NRC) of Canada2 determined the high heat absorption capacity of a high-mass ICF wall creates a five-day thermal lag that helps to maintain a constant indoor temperature even when outdoor temperatures fluctuate. This contributes toward reduced energy requirements and increased occupant comfort. In mid-rise construction, reduced peaks and loads can translate to a reduced HVAC size, ultimately improving the bottom line for both the building owner and occupants.
In the 2005 study, “Monitored Thermal Performance of ICF Walls In MURBs,” conducted by Canada Mortgage and Housing Corporation (CMHC), it was concluded the air infiltration properties of ICF wall assembly delivers up to 60 per cent lower air infiltration than a conventionally built wall.3 Concrete is an air barrier and ICF walls are monolithic by nature and easy to seal around openings. Less air infiltration adds to the thermal performance of the foam insulation, making the building even more draft-free and comfortable, and can also contribute to reduce HVAC system sizing.
All in all, combined with cost-effective renewable energy generation, ICF construction is well-suited for commercially viable net-zero, intelligent buildings.
ICFs sustainable contributions
Using local materials to support economies and reduce transportation costs is a sustainable practice. Concrete is produced locally and ICF distributors and manufacturing facilities are located across Canada, making it easy to service a construction site without excessive transportation costs and delays.
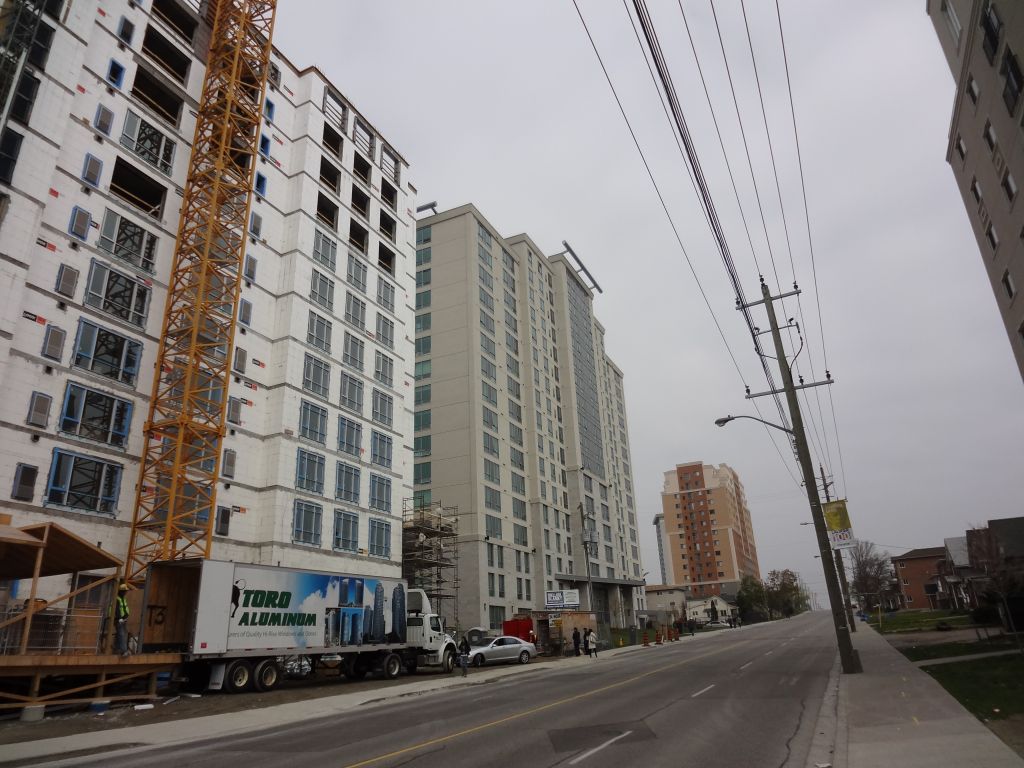
Additionally, ICF construction uses many recycled and recyclable materials. EPS foam can be recovered and reprocessed over and over for reuse at a high level of performance. Also, many ICFs employ 100 per cent recycled materials for their plastic web components. Concrete can be crushed and reused, and much of the portland cement component can be replaced with recycled materials such as fly ash and slag.
ICF construction qualifies as a non-combustible wall assembly and can be engineered to be wind-rated to 482 kph (300 mph). Further, ICF buildings enhance passive-survivability. The superior insulating properties of the high-mass ICF walls mean, in the event of a natural disaster, an occupant will stay comfortable for a longer period of time without power. Indoor environmental quality is of increasing concern, as unhealthy air can pose serious health risks, including cancer and respiratory ailments such as asthma. EPS and concrete are non-toxic materials which do not emit gas. The airtight nature of ICF construction also allows for control of the replacement air which is generally brought in through the HVAC system and filtered.
Finally, ICFs can be a significant contributor in obtaining a project’s Leadership in Energy and Environmental Design (LEED) certification. LEED points are available under Energy and Atmosphere (EA) Credit, Optimize Energy Performance.
Conclusion
The construction of approximately 80 ICF-built midrise multi-family buildings in a single city over the past decade provides construction professionals with a sufficiently large and reliable sample size that proves where timelines are urgent and the weather is cold several months of the year, insulated concrete forms can deliver high-performance, cost-effective buildings on schedule.
Notes
1 For more, see “Energy Consumption of Concrete Homes versus Wood Frame Homes,” by Pieter VanderWerf, PhD, for the Portland Cement Association (PCA). (back to top)
2 See the 2011 report “Field Monitoring of the Dynamic Heat Transmission Characteristics Through ICF Wall Assemblies Over A Full-year Cycle of Weather Exposure,” conducted by Canada Mortgage and Housing Corporation (CMHC) and National Research Council Canada (NRC)/IRC. (back to top)
3 See CMHC’s 2005 “Monitored Thermal Performance of ICF Walls in MURBs.” (back to top)
Andy Lennox is a vice-president with Logix Insulated Concrete Forms Ltd., an ICF manufacturer with four company-owned manufacturing locations across Canada. He has worked in the ICF industry for 17 years in a variety of sales, marketing, and management capacities. Lennox can be contacted by e-mail at andy@logixicf.com.
Francis Roma is the technical director for Logix Insulated Concrete Forms Ltd. An Engineering graduate from the University of British Columbia, Roma has previously worked in the structural design and inspections of bridges, commercial, and industrial buildings and has also worked for Intertek Testing Services evaluating building products to building code and national standards. Roma can be contacted by e-mail at francis@logixicf.com.