How to stop: Parapet and soffit construction solutions
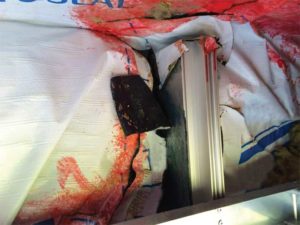
Parapet design strategies
Everyone loves rules of thumb so here is a suggestion for a new one: the one meter rule. In other words, parapets extending more than 1 m (3 ft) above the roof require extra care to control air leakage, mitigate thermal losses, and reduce condensation risk. Parapets less than 1 m can be adequately insulated and air-sealed by conventional means. Of course, there are always exceptions to rules but, for the purposes of this article, here are simple strategies for tall parapets.
Air leakage control in parapets is important since moist, interior air leaking into parapets can lead to concealed (or not) moisture accumulation, especially in colder climates. In fact, perceived roof “leaks” can be the result of parapet air leakage and back pan condensation. Installing an effective air seal at the roof deck level provides compartmentalization to the parapet and helps mitigate the condensation risk.
Additionally, air seals are sometimes needed within a cladding system. As discussed earlier, vertical curtain wall mullions often act as shafts carrying interior air into parapet voids. In the simplest instance, these air seals can comprise a sheet metal and sealant closure on the building interior and foam-filling of vertical curtain wall mullions. More complex or taller parapets may present other opportunities, such as starter tracks just above the roof level to accommodate simpler tie-ins. Solid opaque walls can incorporate an air seal comprising a continuous through-wall membrane at the deck level that transitions to the wall AB/VR control layer.
Thermal control at parapets can present unique challenges. Parapet walls are sometimes designed to accommodate loading from building maintenance equipment such as boatswain’s chairs or swing stages and, as such, are often reinforced with elements anchored directly to the building structure. A prime example is a hollow structural steel (HSS) parapet upstand. These may look great from an air sealing perspective, with continuous membranes, fully-welded plates, and solid materials, but they present significant thermal bridges. This undermines thermal performance and increases the condensation risk. Structural thermal breaks (STBs) may help; however, these may increase cost and affect construction scheduling.
It is important to understand how parapets transition from one to another around the building perimeter as well. Recent architectural trends, such as slot windows, present challenges since they require transitions from unitized (curtain wall) to site-built (opaque wall) systems, each with very different air, vapour, and thermal control layers and materials.
What about a low parapet that becomes a high parapet? Or a low parapet extending behind a shear wall, effectively limiting heat flow to the void space and increasing condensation risk? Each project is unique and likely requires bespoke solutions.
Soffit design strategies
While the one meter rule can apply to soffits, too, many other conditions make soffit design a unique challenge. In most cases, the preferred design is to have a warm, interior zone directly below the occupied floor with suspended control layers. This zone is filled with services such as HVAC supply, plumbing, electrical, and cabling. Maintaining a warm zone below the occupied floor provides optimal thermal comfort to occupants since the floor will generally be maintained at interior space temperatures.
The control layers (typically membrane and insulation) separate this warm, interior zone from a vented—or exterior—soffit space. This vented soffit space permits installation of infrastructure, such as lighting, signage, suspended access supports, and security services, behind architecturally appealing soffit cladding systems. This vented soffit space also permits maintenance of infrastructure elements without compromising the carefully detailed and constructed control layers. Of course, the soffit assembly itself is only one component in the enclosure assembly. Success relies on effective transitions.
Transition design and construction requires knowledge of construction sequencing, a general understanding of structural movement in buildings, and detailed insight into different enclosure systems and how they manage air, water, and thermal. As discussed in the soffit case study, soffit control layers typically comprise “thick” site-built assemblies, such as steel studs, sheathing, AB/VR, insulation, and cladding, whereas many cladding systems comprise “thin” shop-fabricated assemblies, such as curtain walls or precast. The increasing specialization of all sectors, including design and construction, means workers familiar with one system are rarely familiar with another.
Since curtain wall systems are installed prior to soffit systems, it is often left to the soffit worker to complete the tie-in between the two systems. Since curtain wall systems are unique to the manufacturer, one strategy does not apply in all cases. It is incumbent on the design professional and construction quality assurance (QA) team to ensure these transitions receive proper oversight.
One method to improve the simplicity of air barrier transitions between soffits and curtain walls is to remove the curtain wall neck in the transition zone. This permits installation of a continuous, solid transition material on the exterior side of the vertical mullion against which insulation can be installed for a reasonable thermal barrier. The closure must be designed to accommodate differential movement as noted earlier and must be able to resist expected pressures.
Conclusion
Designing and delivering increasingly complex and high-performing buildings requires an understanding of environmental conditions, building materials, construction technologies and delivery models, and physics. Failure to appreciate common demands on modern building enclosures in areas like parapets and soffits can lead to early and costly failures.
Scott Armstrong, BSSO, CET, LEED AP, is senior façade specialist, building sciences, WSP. Armstrong has 20 years of experience in high-performance buildings, building enclosures, façades, existing building repair and renewal, roofing and green roofs, and integrated design. He is past secretary and board member of the Canada Green Building Council (CaGBC) Greater Toronto Chapter. Armstrong can be reached via e-mail at Scott.R.Armstrong@wsp.com.