How to stop: Parapet and soffit construction solutions
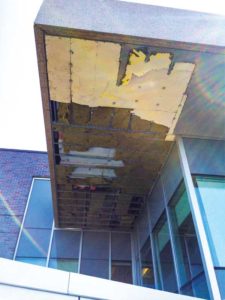
by Scott Armstrong, BSSO, CET, LEED AP
Building shapes have become increasingly complex and cladding systems are often soaring high above the roof level or beyond adjacent façades. Whether used as a design statement or to conceal mechanical or rooftop components, parapet extensions, wing walls, soffits, and other appurtenances create many challenges for design and construction teams. Successful parapet and soffit design means knowing how to stop.
Understanding service conditions
Building enclosures are intended to control air, water, and thermal transfer between dissimilar environments. As we push for taller, larger, more complex, higher performing buildings, the stress on enclosures increases. For example, tall building enclosures are often subject to combined pressures from HVAC supply, wind, and stack effect. These combined pressures can result in long-term positive pressure in some areas and modulating pressure in others.
Designing and constructing is only one aspect of the built environment. A building enclosure must perform its functions in a durable manner and be maintainable. In some cases, the industry expects an enclosure to be functional for more than 50 years with little or no intervention.
It is no secret most enclosure failures occur at transitions and any enclosure specialist will readily identify areas most prone to failure (Read “Improving Tie-in Details for Better Envelope Performance” by Andrea Yee and published in the July 2018 issue of Construction Canada). This article focuses on two extremes of vertical enclosures: parapets and soffits.
Evaluating deterioration and failure
What do parapet and soffit failures look like? Sometimes it is obvious, such as moisture on exterior cladding materials or significant cladding deterioration, but more often, failures present less obvious symptoms. These could be occupant discomfort, space temperature fluctuations, poor building pressurization, or perceived water infiltration. Since many mechanical systems are designed to accommodate a wide range of heating and cooling demands, many of these symptoms can be masked by adjusting dampers, increasing air flow to some areas, or adding supplemental conditioning. Unfortunately, these strategies are short term and energy intensive, and do not address underlying defects contributing to enclosure failure.
Parapet case study
This author’s firm was recently consulted on a newly-constructed mid-rise commercial office tower featuring an approximately 3-m (10-ft) curtain wall parapet extension above the roof. During tenant fit-up, moisture damage was occurring at interior gypsum board window heads and on curtain wall vertical mullions. The damage was initially attributed to condensation on the interior of the back pan due to high interior moisture levels and cold exterior temperatures. The back pan was insulated on the interior by a batt-filled steel stud assembly. This meant back pan temperatures were below the dewpoint range and, as expected, interior air was leaking into the batt-filled cavity and condensing. This article will not debate the ineffectiveness of batt-filled steel stud walls on the interior of curtain wall systems; rather it will focus on remedial strategies attempted and outcomes.
The first attempt to remedy this interior condensation problem, by a different consultant, included adding heat tracing cables to the interior of the back pan to try and maintain the back pan temperature above the dewpoint. The author’s firm was not able to determine whether the heat tracing was able to increase the back pan temperature above the dewpoint; however, repeated damage to refinished interiors confirmed the heat tracing was ineffective at mitigating condensation. Clearly, a deeper investigation was needed to identify other contributing factors and to also develop an effective and low-energy solution.
The author’s firm directed a contractor to provide several interior test openings to assess the back pan, slab edge, and parapet extension detailing. This was coupled with an exterior visual review and infrared thermographic review from the roof-side of the parapet. The investigation revealed air leakage into the parapet and exfiltration at the top of the building as significant contributing factors in the recurring moisture damage. It was acknowledged an effective remedial strategy would need to control air leakage primarily while being minimally invasive and cost effective.
The design and construction documentation provided the necessary data to develop an air barrier plan specifically for the parapet and associated detailing. The temperature drop from interior space to the parapet void space is precipitous, so installing an air seal transition at the roof slab underside to stop interior air flow into the parapet appeared to be the most suitable approach. Since the vertical curtain wall mullions (effectively hollow vertical tubes) extend from the interior to the parapet void space, it was also necessary to provide an air seal transition inside the mullion. Otherwise, interior air could bypass the slab edge air seal and cause condensation.
Fortunately for this client, the trouble was quickly identified and a solution could be implemented prior to occupancy, during the fit-up stage. The air sealing strategy was deployed at the top floor around the entire building perimeter. Once air sealing was complete, no further reports of condensation or moisture damage were reported and the tenant occupied their space on schedule. While this matter was resolved quickly with little disruption, these issues could have been identified on the design or shop drawings and resolved prior to the tenant fit-up stage, saving time and money. Some appropriate design strategies will be presented later in this article.