Hot-dip Galvanized and Metallizing: A dynamic duo
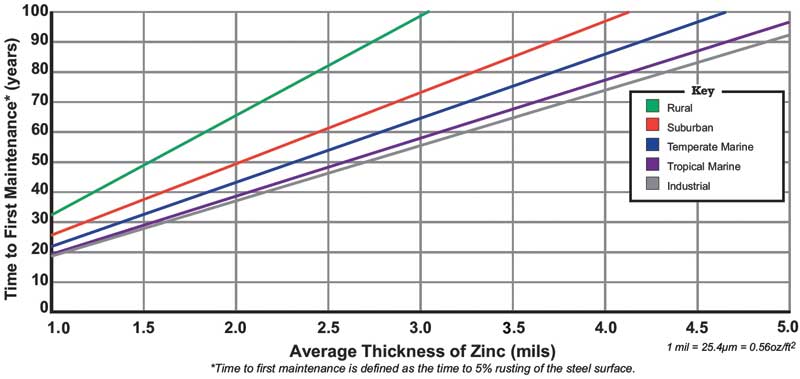
Images courtsey AGA
Zinc spray metallizing
Zinc spraying, or metallizing, is accomplished by feeding zinc powder or wire into a heated gun where it is melted and sprayed onto the part using combustion gases and/or auxiliary compressed air. While there are automated metallizing processes, the coating is still most often applied by a skilled operator. Prior to metallizing, the steel must be abrasively cleaned to a near white metal. As the steel surface must remain free of oxides, it is common to clean smaller areas, coat the area, and then move to the next section of the part, which adds time and cost to the coating process. The coating is 100 per cent zinc and is often sealed with a low-viscosity polyurethane, epoxy-phenolic, epoxy, or vinyl resin. Metallizing does not provide the same bond strength as galvanizing to steel, but still has a bond strength of approximately 10,300 kPa (1500 psi)—much stronger than the 2000 to 3500 kPa (300 to 500 psi) of paint coatings.
The metallized coating is rough and slightly porous. However, as the metallized coating is exposed to the atmosphere, zinc corrosion products tend to fill the pores, providing consistent cathodic protection. If the metallized coating is applied properly, and is thick enough, the corrosion performance will be similar to hot-dip galvanized steel. The metallized coating can be applied to meet any thickness requirement (with a density about 80 per cent of hot-dip galvanizing), but excessively thick coatings can have adhesion issues. The metallized coating cannot be applied to interior surfaces and tends to thin at corners and edges as they are harder to consistently spray than flat surfaces. Additionally, the complexity of the structure and accessibility are important to consider for the operator.
Zinc spray can be applied to materials of any size, and is often used as an alternative to, or in conjunction with, batch hot-dip galvanizing when a part is too large for immersion in the galvanizing kettle. Although the coating is more commonly applied in the shop, it is possible to apply in the field—making it a great option for extending the life of a steel structure already in place. The biggest limitations to metallizing applications are availability (i.e. skilled operator and equipment) and the significant cost premium.
The difference in initial cost for a typical project can be substantial between hot-dip galvanizing and metallizing (e.g. $24.98 vs. $125.88 per m2 [$2.32 vs. $11.70 per sf]). Metallizing is even more expensive when performed in the field, and also for smaller pieces, as the material handling increases. The lifecycle cost for metallizing is also greater because hot-dip galvanizing remains maintenance-free over the life of the project, while metallizing may require maintenance depending on the project and environment. To analyze the initial and lifecycle costs of galvanizing and metallizing for a specific project, the project data can be placed into the Lifecycle Cost Calculator (LCCC) tool located on the American Galvanizers Association (AGA) website. (Find the lifecycle cost calculator online by visiting lccc.galvanizeit.org).
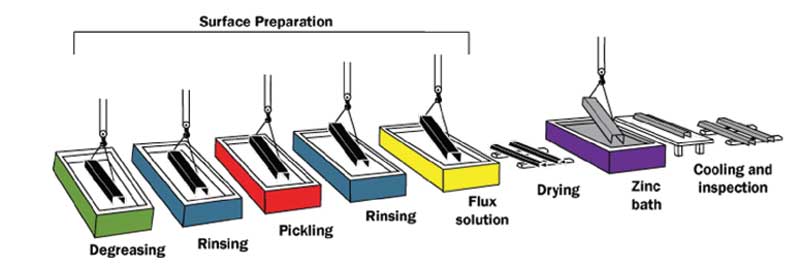