Higher-performing Balconies: Integrating manufactured structural thermal breaks
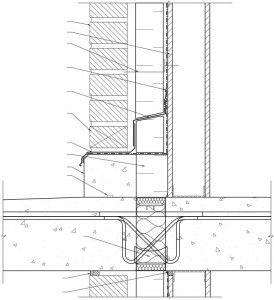
Integration in Canadian design
The National Building Code of Canada (NBC) serves as the model building code for provincial jurisdictions. Part 4, “Structural Design,” includes provisions applicable to manufactured structural breaks as part of the overall structural design. Compliance to these code provisions is generally objectively based. Conversely, sections like Part 3, “Fire Protection, Occupant Safety, and Accessibility,” contain provisions that may be deemed applicable to structural breaks, depending on the Authority Having Jurisdiction’s (AHJ’s) interpretation of the code and the material used. It is therefore recommended this be discussed at early design stage.
As manufactured structural thermal breaks become more widely used in Canada, it seems likely future iterations of building codes will adopt specific language to address these components’ use. Additionally, the manufacturers can be helpful in satisfying certain current code provisions by providing fire and thermal ratings or code-compliance reports for materials.
To ensure the requirements of a project are met, an integrated design process between the project architect, relevant specialty consultants, construction team, and the manufacturer’s technical staff is recommended. For example, an appropriate design solution for a high-rise residential building with cantilevered concrete balconies will vary based on regional construction practices and cladding assemblies. Brick veneer, architectural precast concrete, exterior insulation finish systems (EIFS), and painted concrete will all yield different outcomes depending on thicknesses and other variables. Therefore, the project designers will be required to determine and illustrate the location/placement of the thermal breaks, taking into account considerations from the integrated design team.
This team includes:
- the code consultant to comply with requirements for fire resistance/protection specific to the project details;
- the building envelope consultant and architect to maintain continuity of the critical barriers (i.e. air, moisture, vapour, and thermal); and
- the structural engineer to avoid interference with the structural attachment of other elements (e.g. glazing and framing).
Additionally, the structural engineer should take into account:
- slab rotation at the balcony (primarily due to the elongation of the unbounded bars in the break) can result in a possible camber of the balcony, depending on the drainage requirements;
- expansion joints in the exterior structure due to thermal elongation of the exterior element, which are required by using structural thermal breaks, and are recommended by comprehensive manufacturer testing; and
- lap reinforcement to ensure the transmission of the loads into the slab—the normally used slab reinforcement for balconies should consider the overlapping with the manufactured thermal break’s reinforcement to ensure load transmission from the balcony to the slab.
The manufacturer’s technical staff may also be able to offer support with these factors, based on project experience and internal research/testing. Some companies provide recommendations for these considerations in their technical manuals.
To summarize, the following key points should be discussed among the design team before the drawings are finalized:
- minimum clearance needed for structural attachment of
other elements; - fire protection requirements at selected details;
- continuity of the building envelope critical barriers;
- waterproofing transition and connection details; and
- installation procedure and construction sequencing.
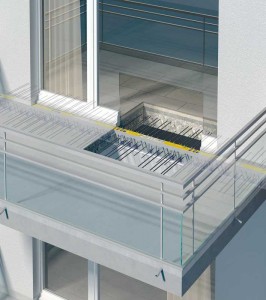
Construction installation
For cantilevered concrete balconies, co-ordination issues can be simplified by making the acquisition and installation of the structural thermal break part of the concrete contractor’s scope. Also, an ‘early’ submittal can ensure satisfactory lead time with the component supplier’s engineering, manufacturing, and delivery, along with onsite technical assistance schedules.
A main advantage of manufactured structural thermal breaks is they come readily assembled to reduce additional installation time. The products can therefore be installed with relative ease and speed between the other onsite reinforcement.
Conclusion
As energy efficiency requirements in the Canadian building construction market continue to become more stringent, greater emphasis and attention will be necessary to reduce thermal bridging during design. In addition to the energy use benefits of thermal breaks, there are also other benefits such as reduced risk of condensation and mould occurrence, and improved user thermal comfort.
Manufactured structural thermal breaks provide an attractive option because the product/system testing has already been completed to facilitate ease of adoption in design and construction. The integration and installation of thermal breaks has various considerations, necessitating collaboration among the project stakeholders to ensure the requirements are met. This is no different from any quality construction project.
Dieter Hardock, Dipl.-Ing., is a product manager at Schöck Bauteile GmbH (Baden-Baden, Germany), which develops and manufactures products related to the prevention of thermal bridges and impact noise in buildings. He can be contacted via e-mail at dieter.hardock@schoeck.de.
Dave André, P.Eng., LEED GA, is a project manager/building science consultant at Morrison Hershfield’s Toronto office. He has more than eight years of experience in building science ranging from envelope failure investigation and rehabilitation on existing buildings to field review for new construction projects. André can be reached at dandre@morrisonhershfield.com.