HFO-blown spray foam to prevent air leakage, improve waterproofing
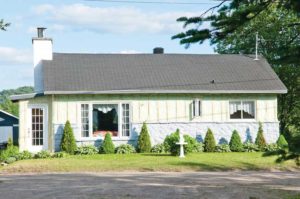
Commercial/institutional building
Baie-Saint-Paul Hospital is an example of an air barrier and waterproofing project. The architectural consortium, which designed the project, and the general contractor used spray foam insulation in an effort to receive LEED certification.
Today, the hospital’s air barrier system meets energy efficiency requirements. By using spray foam insulation, the hospital has a value of R-27 for the insulation alone, which exceeds all requirements for all building types.5 Including the complete wall assembly, the insulation value is approximately R-30. Further, all the insulation is on the exterior side of the wall, keeping thermal bridges to a minimum, which improves the wall’s effective R-value. The heating and air conditioning costs are also therefore greatly reduced, resulting in a much lower building use cost.
Cold storage facility
Cultures H. Dolbec Inc. in Saint-Ubalde, Quebec went with an exterior spray foam insulation approach for their moisture-controlled warehouse, using state-of-the-art technology fully automated for potato conservation. The mandate for their 50 x 92 x 9.6 m (164 x 301 x 31 ft) design-build, with a surface area of near 5,202 m2 (56,000 sf) of the building envelope, including wall and roof insulation, interior partition wall, and the doors.
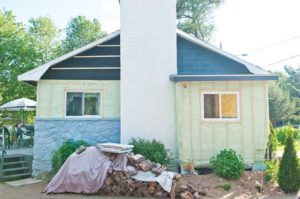
The building was constructed to offer a spacious interior and a high energy efficient building envelope to reduce the operation costs. Storage of large potato crops requires a controlled climate environment and must be moisture-free. Spray foam insulation sprayed in the walls and ceilings allows for those desired climate conditions and minimized condensation inside the storage building. By having spray foam insulation installed from the exterior of the building, it created a monolithic insulation and air/vapour barrier, removing the risk for condensation, addressing thermal bridging, and creating a rainscreen for exterior water penetration.
Historical building renovation
In the autumn of 2000, Patenaude Consultants Inc. conducted a condition survey case study of a wall in the Lofts Corticelli Complex in Lachine, Quebec.6 The Lofts Corticelli Complex consists of three, four-storey buildings (blocks A, B, and C). The buildings are clad predominantly with solid clay bricks (two or more courses) and aluminum punch windows. The wall sections consist of 12.7 mm (0.6 in.) gypsum board with aluminum foil backing on steel furring; 44.5 mm (1.75 in.) fibreglass batt insulation, 19 to 25.4 mm (0.9 to 1 in.) polyurethane foam insulation, and two or more courses of brick cladding. This type of retrofitted wall was insulated from the interior using spray-applied polyurethane foam insulation.
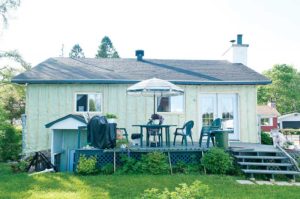
Originally built for industrial purposes, the buildings were converted for residential use in 1984. As part of the conversion work, polyurethane foam insulation was sprayed over the interior surface of the solid masonry walls. An insulation-filled wall framing system, finished with gypsum board sheathing, completed the wall assembly. The physical analysis for the spray foam applied met the CAN/ULC S 705.2-98 standard requirements for cohesion and adhesion properties, and had a good cell structure and normal density. In general, the spray-applied polyurethane foam insulation was in good condition, with good adhesion to the masonry. The polyurethane foam had been applied as a continuous system, and no visible cracks in the material were noted. The success of the masonry insulation retrofit at Lofts Corticelli is primarily due to adequate control of air and moisture flow across the masonry.
In all these examples, HFO-blown spray foam insulation showed its strengths: unparalleled performance in terms of R-values, cost savings for the end-user, waterproofing abilities, and an overall lowered ecological footprint.