Healthier Indoor Air: Reducing harmful emissions from building materials and consumer products
Since emission rates tend to change over time, it is important to select an optimal test period in order to reach a balance between correctly characterizing long-term emissions and keeping the test costs reasonable. The European Committee for Standardization (CEN) recommends air samples should be taken after three to four days to characterize short-term emission behaviour, and after 28 days to understand long-term emission behaviour. (These recommendations can be found in European Committee for Standardization Technical Specification [CEN/TS] 16516:2013, Construction Products–Assessment of Release of Dangerous Substances–Determination of Emissions into Indoor Air.) In North America, a conditioning period is recommended for a short-term test. For example, ASTM D6007 and ASTM E1333, Standard Test Method for Determining Formaldehyde Concentrations in Air and Emission Rates from Wood Products Using a Large Chamber, require seven-day conditioning before one-day testsfor formaldehyde emissions from wood products, while a 10-day conditioning period is required before four-day tests for VOC emissions from indoor sources. (This requirement is stated under California Department of Public Health’s [CDPH’s] Standard Method for the Testing and Evaluation of Volatile Organic Chemical Emissions from Indoor Sources Using Environmental Chambers–Version 2.1 [Emission Testing Method for California Specification 01350].)
At NRC, temperature control is achieved using an environmental enclosure that can hold the temperature at a desired level (e.g. 23 C [73 F]). The humidity in the chamber is maintained by blending dry and humidified airstreams, typically with mass flow controllers, and continuously monitoring the exhaust air for relative humidity.
In order to limit the emissions to the material surface, NRC developed and custom-fabricated a specimen holder, mimicking the emissions in real environments, minimizing emissions from specimen edges and back, and therefore precisely meeting the material loading ratio requirements. Meeting the requirement of a material loading ratio (i.e. the ratio of the area of exposed surface of the test specimen to the chamber volume) is particularly important, as it can affect the chamber concentration and emission rate. This practically means that emissions are fairly characterized, like in a real indoor environment.
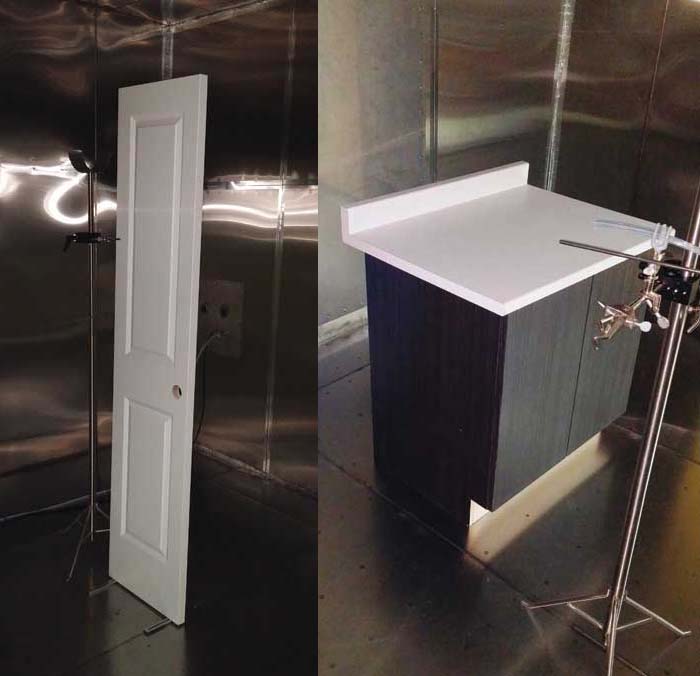
VOCs and formaldehyde emitted from the building material into the chamber are then drawn out of the chamber onto a sampling medium (i.e. sorbent) at a designated time, and subsequently analyzed with a gas chromatography/mass spectrometry (GC/MS) and high-performance liquid chromatography (HPLC). Since materials can emit hundreds of chemicals, which cannot all be caught by the same sorbent, it is sometimes necessary to sample onto several sorbents in parallel and analyze them with different apparatus.
While small-scale testing is one very useful approach, in some cases it is more appropriate to do large-scale experiments for room-size building materials, material assemblies, and furnishings. It may also be helpful to think of your office and all that is in it. The 31,000- to 55,000-L (31 to 55m3) full-scale test chamber at NRC (Figure 5) was developed to assess exactly this type of scenario. The room-sized chamber has a dedicated HVAC system, which also includes charcoal and high-efficiency particulate air (HEPA) filters to clean the supply air, which is identical to the small-scale chamber in principle. This chamber meets the specifications stated in ASTM E1333, which is adopted as the full-scale testing method by CSA O160 and CARB ACTM 93120.
Screening of SVOC emissions
In addition to formaldehyde and VOCs, building materials may contain so-called semivolatile organic compounds (SVOCs). The main difference between VOCs and SVOCs is the latter have higher boiling points, which means only a smaller portion is released from the building materials as compared to volatile organic compounds, with the majority of the released SVOCs then ‘sticking’ to indoor surfaces or airborne particulates. While this can mean lower levels of chemicals in air as compared to VOCs, the chemicals that are present in building materials will be emitted over much longer time periods. Many different chemical classes fall under the category of SVOCs, such as flame retardants (including polybrominated diphenyl ethers [PBDEs]), plasticizers (including phthalates), and biocides, to name a few.
Health effects of SVOCs or classes of SVOC vary widely, and are dependent on chemical classes and their individual chemical properties. Health effects potentially associated with exposure to some classes of SVOC include allergic symptoms in children, effects on the reproductive system and birth weight, and endocrine disruption. (For more, see C.J. Weschler and W.W. Nazaroff’s “Semivolatile Organic Compounds in Indoor Environments,” in Atmospheric Environment 42, 9018−9040.)
Some SVOCs found in building materials are on the List of Toxic Substances under CEPA. Examples are diethylhexyl phthalate (DEHP) used as a plasticizer, PBDEs used as a flame retardant, and hexabromocyclododecane, 90 per cent of which is used in polystyrene insulation. (For more information, consult the Government of Canada’s Toxic Substances List–Schedule 1, from April of this year, at www.ec.gc.ca/lcpe-cepa/default.asp?lang=En&n=0DA2924D-1&wsdoc=4ABEFFC8-5BEC-B57A-F4BF-11069545E434. More on hexabromocyclododecane is available at www.ec.gc.ca/toxiques-toxics/default.asp?lang=En&n=58F1CC80-1.) When investigating SVOC emissions from building materials, test conditions should be modified to consider SVOCs’ high boiling point and low volatility relative to VOCs, which would lead to high absorption rates on the test chamber surfaces. Therefore, it might take up to several months to achieve a steady state between surface and chamber air concentrations. Steady-state conditions are desirable to reproducibly assess emission rates. Furthermore, sampling before steady state could lead to chamber concentrations that are too low to be reliably detected.