Havergal College uses copper to bridge tradition and sustainability
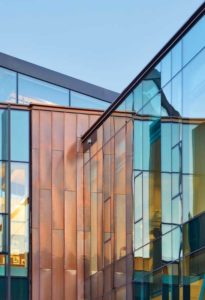
Many of Havergal’s original buildings utilize copper material for roofs, parapets, and flashings. The strength and resilience of these copper elements prove well-suited, especially for educational and institutional buildings with long lifespans. Copper’s natural resistance to corrosion and low maintenance requirements offset higher initial material costs, compared to metals, which require periodic painting, refinishing, or replacement.
The repeating rhythms of vertical copper panels on the exterior represent one of the building’s most striking features.
“The copper takes an existing material and uses it in a way so that it finds a modern expression,” says Jim Graves, project manager at Diamond Schmitt. “The standing seams add texture to the facade and will continue to transform for many years as the material patinates.”
The copper material complements the adjacent glass while evoking copper roofs and ornamentation featured on prominent educational, religious, arts, and government institutions found across eastern Canada.
According to Buttcon, the general contractor, from a construction standpoint, the facade was primarily a structural curtain wall with localized copper wall infill and masonry sections; therefore, copper is a good choice because it will outlast other similar finishes when used as an exterior. Further, copper ages with the building, withstands weather, and is typically a preferred and premium finish for metal clad buildings. Copper elements can last a century or more, reinforcing the principle of using materials wisely and in a sustainable way.
A metal fabricator manufactured more than 1021 m2 (11,000 sf) of facade panels for the project. The cladding is made of 453-grams (16-oz) copper pans, with 50.8 mm (2 in.) of standing seams adding a textural pattern to the facade. Since Toronto can experience warm summer temperatures to well below freezing winters, the manufacturer included “a sprung edge to help reduce oil-canning and allow for expansion and contraction of the copper during varying weather conditions.” For the complementary copper parapets, the project team created 25.4-mm (1-in.) standing seams along the roofline to allow for an infill condition.
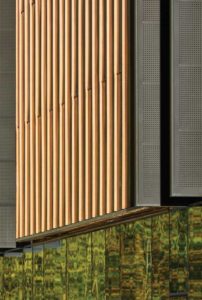
The construction team also applied copper to areas where the old and new structures came together, applying a pan curb that facilitates a 152.4-mm (6-in.) structural joint. Copper’s workability helped it accommodate challenging conditions at these points, creating consistent and functional transitions.
“It is also nice to be able to do the wall and all flashings in one material,” says Graves. “The variability of what you are able to do with copper is greater than some other materials.”
For the projecting copper parapets with deep shadow reveals, the team created small returns along the length to account for changes in the depth of the back-sloping parapets. This flexible approach utilized a mitered parapet profile with 25.4 mm (1 in.) upstand at ends, and a special transition piece which could be s-locked in place.