Harnessing the all-in-one aspects of tilt-up
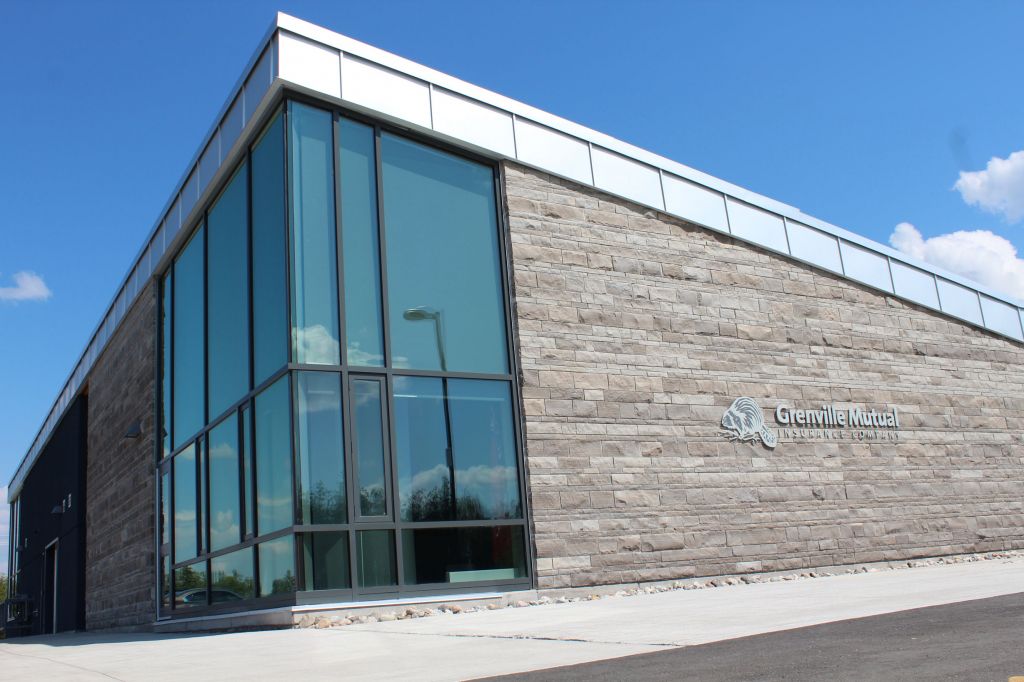
By Ross Monsour
Constructing buildings requires the skills and knowledge to meet the demands of speed of construction, energy efficiency, resiliency to environmental conditions, cost efficiency, and long-term durability. The tilt-up concrete method, which speaks to all these attributes, has steadily grown since the 1940s due in large part to the development of the mobile crane and advancements in ready-mixed concrete.
Thomas Edison was one of the early pioneers of the tilt-up system, building a New Jersey village in 1908 in an attempt to minimize the labour requirements for the site. This effort to find a simpler way to build, was ironically derailed with the advent of World War II, as the economy no longer required labour savings—an injection of public funds intended to drive the war effort and put everybody to work.
Tilt-up has come a long way from those days with the refinements in technology, materials, systems, and understanding of building science.
Anatomy of a tilt-up system
In tilt-up, the concrete panels are cast on the structure’s floor slab or, depending on the building’s footprint, on an adjacent slab. A bond breaker is used between the casting slab and the panel’s exterior. The outside cladding is placed first on the slab, and then the panel is built from the exterior to the interior depending on the design requirements. This allows for insulation to be encased in the building panel.
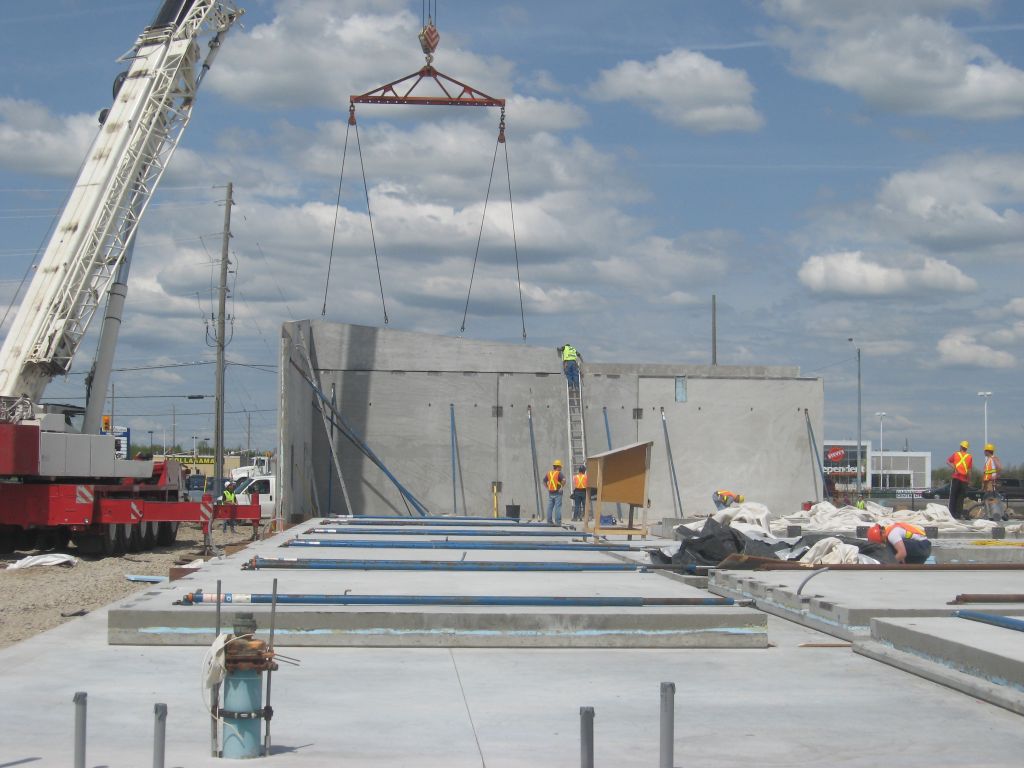
The lifting hardware is placed in the wall before the casting of the concrete. Sufficient time must be allowed for the concrete to reach its structural lifting strength. Then, the panels are lifted into place where they are tied together. The junction of the roof and wall panels has an edge-to-edge junction; it provides a continuous layer of insulation that eliminates thermal bridging.
Another option for the construction of the panels is in a precast location offsite. The only issue with this method is transportation to the site becomes another design factor, and can have an impact on the construction timing. However, an advantage of offsite casting is it can be done inside, away from the elements. This still requires proper setup time of the concrete, and may limit the potential size of panels both from a transport and facility perspective.
Design considerations for tilt-up construction go beyond the detailing and construction of the panels. The layout of the panels on the slab must be engineered so sequential placement is crucial when they are lifted into place. Another major consideration is the location and loading capacity of the cranes needed for a project. These elements affect the speed and placement of the panels onsite.
Safety is a major consideration. As with any site, crews must be trained in the placing and lifting of panels. Individual panels can reach as high as 27 m (90 ft), and weigh in at 150 tonnes. Once the panels are lifted into place, they require temporary bracing until tied into the building’s structural elements.

The exterior design of panels can accommodate various claddings. Decorative architectural finishes can provide other options, including a wide array of colours that can be added directly to the concrete mix, or textured paints that may be applied to the surfaces. The panels can be designed to use extensive surface textures by using formliners and conventional forming materials to produce any surface effect required. Exposed aggregate and mechanical tooling surface treatments can be incorporated in the panels for the desired architectural finish. Use of a brick inlay system offers the appearance of masonry construction for the finished building.
Determining whether tilt-up is right for a project
Applications for tilt-up have varied over time, with the initial use limited to warehouses and commercial facilities—the construction method was not originally seen as particularly flexible. The move to more energy-efficient buildings has brought this technology into a much broader series of potential uses. Today, applications cover a wide range, such as single- and multi-storey retail, schools, or generally any project where the owner-developer retains ownership of the building, and is seeking the operating savings and maintenance benefits outlined in this article.
The selection on whether a tilt-up system is right for a particular project can be assessed by looking at the needs of the design. The first consideration around every decision is the budget; looking at the owner’s operating and maintenance costs will also assist in this decision.
Another determining factor in using tilt-up is the site’s layout must allow for sufficient room to cast the panels, whether they are cast on the slab footprint of the building or on the surrounding construction site. All owner developers require the job to be constructed in the shortest possible time frame, consideration for buildings such as high schools or seasonally sensitive developments can make use of the speed of construction that tilt-up offers.
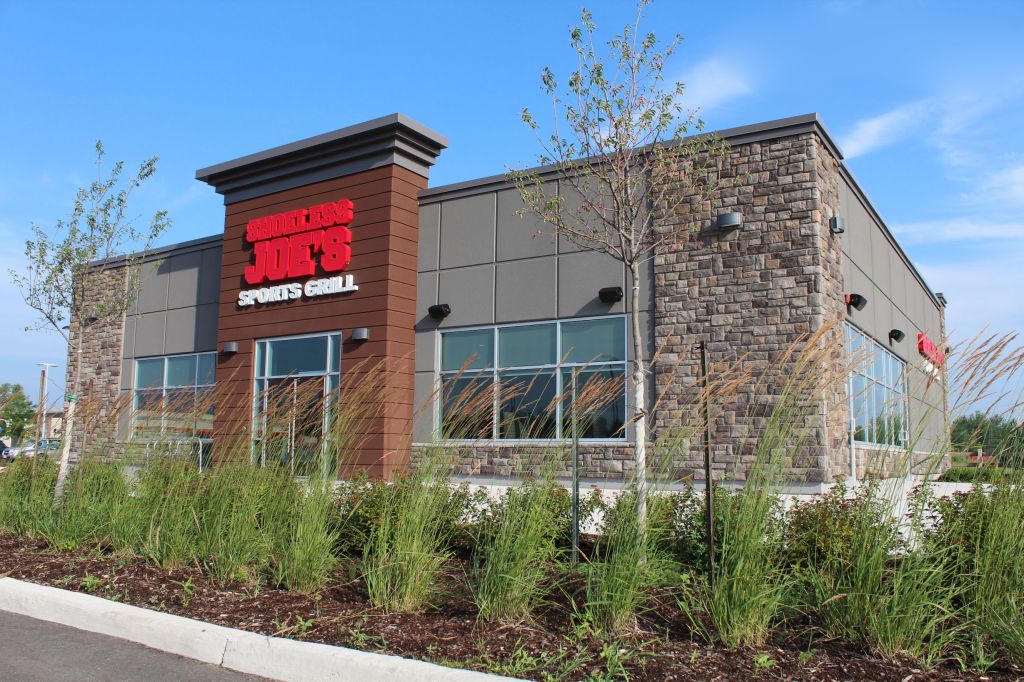
Speed of construction
The panels are constructed from the exterior to the interior, with the crews completing the panels before being craned into place. This reduces the logistical time of co-ordinating the trades to build the envelope and results in significant savings of construction time.
Energy efficiency
The tilt-up system provides an airtight barrier with the continuity of the walls and roof panels. Floor junctions are in the interior of the building assisting in the continuous air barrier assembly. The insulated tilt-up panel consists of two concrete layers with insulation sandwiched between, providing not only good thermal resistance, but also the positive impact of thermal mass for the building’s energy efficiency.1
Site security
As moisture and fire resistance are inherent properties of concrete, there is reduced potential for vandalism damage during the construction process.
Portability
The construction and attachment of the panels allows for the dismantling and moving of the building to another location. Although this is presently not normal for most Canadian buildings, the potential for moving schools could have a positive impact on society’s future economic demands with changing demographics. For example, in urban areas, some inner-core schools are being closed, with new ones built out in the developing areas. The savings afforded by transporting buildings from location to location to follow demand could be substantial.
Other advantages
Architects and designers want the flexibility to express their own signature for the building—with a wide range of finishes, tilt-up assemblies can provide specific esthetic features. Different formliners placed on the slab to emboss any design directly into the concrete can be used.2 This embossing can be textured, coloured, or painted. Finishes such as brick masonry, with the option for large glazing areas, can also be incorporated into the design.
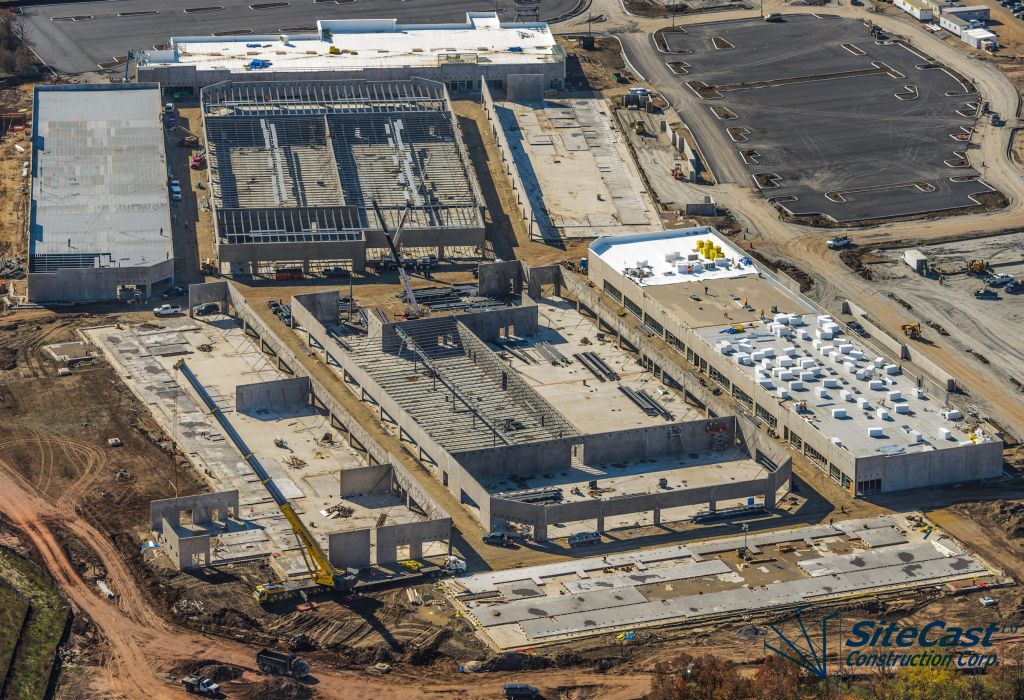
Another area of concern is the long-term sustainability and durability of current building and infrastructure systems. Building certification programs have had success raising awareness in the design community, and tilt-up provides the necessary features and benefits to address those concerns.
Concrete itself has many properties attracting designers seeking durability. Use of local materials reduces carbon emissions for transport, and concrete is recyclable. Further, having panels constructed onsite minimizes material waste, reducing impact on local landfills. Further, the combination of an insulated airtight envelope and the thermal mass can allow for reduced carbon footprint and potentially lower operating costs over the life of the building.
Thermal mass allows more stable control of building temperature, which reduces the overall design load for heating and mechanical equipment. The design versatility of tilt-up can create a smaller footprint during the construction of the building, minimizing the land usage because panels can be cast on the interior slab.
The glazing can be designed to maximize the solar gain or minimize the cooling loads on a building using natural daylighting as it uses concrete as the structural component in the panels.
Examples from the field
An example of the energy savings achieved with tilt-up in a high school—Des Sentiers in Cumberland, Ont.—has been verified through one of the major tilt-up contractors in North America, Ottawa-based Site Cast Construction. The actual energy savings for hydro was 23 and 38 per cent less for natural gas compared to a similar school built at the same time. This is attributed to the airtightness detailing of the tilt-up panels when combined with the thermal mass properties.
Further, the school also showed the tilt-up building was completed three months ahead of the standard construction for the school board. The tilt-up panel minimizes the need for scheduling trades at each stage of construction as complete panels are built from the slab up and reduces time spent co-ordinating the standard construction of the wall. This has created an extended market in high schools and portables for the tilt-up system.
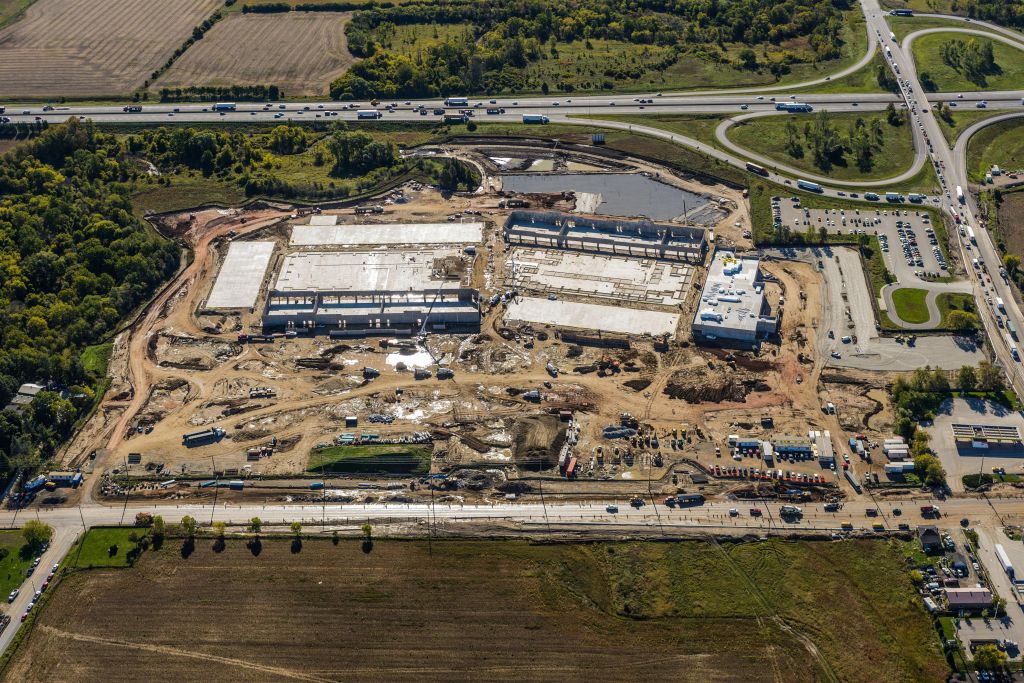
Another example of Site Cast’s contractor’s tilt-up development work was the Simon-Calloway’s first Canadian mall outlet in Toronto. There were eight buildings covering about 39,950 m2 (430,000 sf) of floor area, which resulted in 389 tilt-up panels covering almost 20,440 m2 (220,000 sf) of panel area.
Reason cited for opting for tilt-up included:
- structural panels allow for unobstructed show, office, and retail floors;
- exterior finish enables corporate identity to be projected on building;
- construction time savings;
- safety and security of the durable panels during the operation of the building.
Conclusion
Tilt-up has been used across Canada with the markets in the Western and Atlantic provinces more developed than Ontario. This might be related to the U.S. influence on these markets, with some of the big-box stores south of the border employing tilt-up as their main form of construction. Ontario has been slow to move in this direction and the technology remains the choice of a few owner/developers. However, this may change in the future as development continue to allow larger panels, more artistic finishes, and potentially high R-value vacuum panels incorporated into the wall system.3
Notes
1 For more on thermal mass, see the article, “Mass Appeal-Energy savings through concrete’s thermal mass,” by Andy Vizer, P.Eng., LEED AP, in the September 2007 issue of Construction Canada. (back to top)
2 Additional information on the visual possibilities of these tools can be found in “Function Meets Esthetics: Using Architectural Concrete Formliners,” by Ray Clark and Bob Fedchyshyn in the May 2013 issue of Construction Canada. (back to top)
3 Those looking for more information, can consult the Tilt-up Concrete Association (TCA), which provides training and certification for this type of construction throughout North America. Its site, www.tilt-up.org, provides additional resources. (back to top)
Ross Monsour is Ready Mixed Concrete Association of Ontario’s (RMCAO’s) director of marketing. He was previously a residential construction advisor with Canadian Home Builders’ Association (CHBA) and has worked under contracts with the Natural Resources Canada (NRCan) R-2000 Home Program and National Research Council’s Industrial Research Assistance Program (NRC-IRAP). Monsour’s expertise ranges from troubleshooting residential buildings to codes and standards development. He is a sitting member of the National Building Code Standing Committee on Small Buildings and Housing. Monsour has been in the industry for more than 30 years. He can be contacted via e-mail at rmonsour@rmcao.org.