Harness design freedom with hot-dip galvanized steel
Maximizing esthetics by utilizing duplex systems
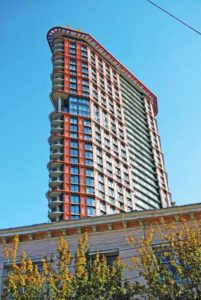
Photo courtesy American Galvanizers Association
Some fabricators and architects who do not believe hot-dip galvanized finishes can meet various AESS requirements or client expectations think simply upgrading to a duplex system (paint/powder coating over HDG) is the solution to their concerns. Although duplex systems can provide unlimited colour options and cover differences in HDG coating appearance, if proper design practices are unemployed for HDG and for preparing the HDG surface for paint are unfollowed, it is likely the duplex coating will not meet the visual requirements for AESS.
When planning a duplex system, it is still imperative to design the steel to avoid excessive zinc buildup, roughness, and other surface imperfections that will be accentuated (not hidden) by the top coat. Similar to AESS requirements going beyond those of ASTM A123/A123M, non-AESS galvanized items that will be duplexed also have more strict guidelines on finish that must be discussed, and responsibility assigned to ensure success. Communicating through clearly written specifications the intent to duplex coat the steel to both the galvanizer and painter is needed to ensure critical surface preparation steps are accounted for in the bid and performed to ensure proper adhesion and maximize esthetics.
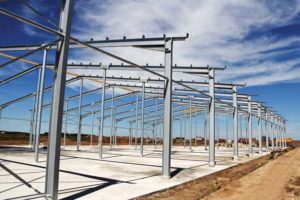
Photo © BigStockPhoto.com
When planning for duplex coated AESS, there is even more importance to clarifying and agreeing to responsibilities for surface smoothing of the HDG coating, and potential additional practices that may be necessary to achieve finishes meeting AESS 3 or 4. For example, it may be necessary to specify filler material to even out divots or indentations on the surface from vent/drain plugs, weld areas, etc. to provide a uniform, smooth surface for the paint.
When planning to duplex AESS steel, it is important to reference and understand ASTM D6386, Standard Practice for Preparation of Zinc (Hot-Dip Galvanized) Coated Iron and Steel Product and Hardware Surfaces for Painting, and D7803, Standard Practice for Preparation of Zinc (Hot-Dip Galvanized) Coated Iron and Steel Product and Hardware Surfaces for Powder Coating, to ensure proper surface preparation of the HDG coating. Additionally, AGA has resources and instructional guides and videos available for specifiers and painters to ensure successful duplex coatings.
Conclusion
Architecturally exposed structural steel (AESS) allows architects almost limitless design freedom to bring their creativity to life. Protecting exterior AESS with HDG allows these designs to transcend time without the worry of unsightly rust forming or expensive maintenance. Although hot-dip galvanized steel’s initial appearance is difficult to predict, there are a number of design practices and process controls that can be employed to maximize the appearance. By communicating early and often with all parties involved through a well-written specification, it is quite possible to eliminate headaches and achieve successful hot-dip galvanized AESS projects.
Melissa Lindsley is the American Galvanizers Association’s (AGA’s) marketing director. She is recognized as a leading voice for the galvanizing industry in North America. Lindsley educates architects, engineers, fabricators, owners, and specifiers about the technical aspects and benefits of hot-dip galvanizing. She can be reached via e-mail at mlindsley@galvanizeit.org.
Alana Hochstein is the American Galvanizers Association’s (AGA’s) corrosion engineer. She provides assistance to architects, engineers, fabricators, owners, and specifiers on technical issues and processing of hot-dip galvanized steel. Hochstein also manages AGA studies and research on performance, application, and processing of galvanizing steel, including selection of abrasives to prepare hot-dip galvanized steel for painting/powder coating. She is a member of both National Association of Corrosion Engineers (NACE) International and the Society for Protective Coatings (SSPC) and is a certified NACE Level 1 coating inspector. She can be reached at ahochstein@galvanizeit.org.