Harness design freedom with hot-dip galvanized steel
Process controls
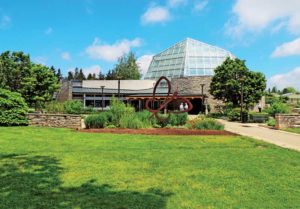
Photo © BigStockPhoto.com
Although there are many design and fabrication considerations outside of the galvanizers purview impacting the overall HDG finish and appearance, there are process controls the galvanizer can implement to minimize surface smoothing and improve final appearance for AESS projects. A few controls the galvanizer can consider and possibly implement are:
- immersion/withdrawal controls (quick as possible immersion, suspension of parts above dross line, highest possible dip angle, minimize dip time, and slow withdrawal);
- elemental additions to the galvanizing bath;
- optimizing selection of touchup and repair materials; and
- proper storage.
Although the galvanizer can control these items, most require a team effort or shared responsibility. Many of these controls relate to the design practices discussed (optimizing vent/drain holes, discussing practical limitations, etc.) For example, the galvanizer can only immerse the material as quickly as is safe based on the vent holes provided. If the part is designed to optimize venting for quick immersion, then the galvanizer can speed up the immersion to help with overall appearance. Further, if the galvanizer employed all of these noted process controls, but the steel chemistry of the material used is outside of the recommended compositions for HDG, these controls will have a negligible effect on the final appearance.
There is also a lot of shared responsibility when considering the use of touchup and repair materials and proper storage. In-plant repair and storage are the responsibility of the galvanizer. However, field touchup and storage are the responsibility of the fabricator and/or the GC. The touchup and repair of hot-dip galvanized steel both in the plant and field is controlled by ASTM A780, Standard Practice for Repair of Damaged and Uncoated Areas of Hot-Dip Galvanized Coatings, which contains three acceptable materials: zinc rich paint, zinc solder, and zinc metallizing. Each is acceptable for touchup (effective), but they all have different appearances. So, if esthetics is critical, it should be discussed and added to the bid documents.
It is important to note, the requirements within ASTM A780 are to ensure proper corrosion protection is in place and appearance is not really a consideration. The use of a preferred touchup material should be outlined in the project specification, and is another area where direct communication is beneficial to ensure the method used maximizes the esthetic to meet the appropriate AESS category. Some touchup materials that are a closer match to the initial appearance may not be the closest match to the galvanized coating once it weathers. Making sure the galvanizer, fabricator, and GC are in agreement and aware of esthetic requirements and preferences in regard to touchup at the plant and field is critical.
Proper storage of hot-dip galvanized steel is necessary to prevent the formation of wet storage stain (commonly referred to as white rust). Wet storage stain can develop on the HDG surface if the parts are stored where they can have a buildup of moisture without the presence of free-flowing air. The presence of light or medium wet storage stain does not negatively impact the corrosion protection afforded and, therefore, does not require remediation. However, it can lead to an undesired appearance. Similar to all hot-dip galvanized surfaces, differences in appearance due to wet storage stain will become uniform over time as the zinc coating weathers. However, if the appearance is unsuitable, the AGA has instructions on cleaning wet storage stain. Similar to touchup and repair, proper storage is a shared responsibility of the galvanizer and fabricator/GC.