Harness design freedom with hot-dip galvanized steel
Practices to maximize HDG esthetics
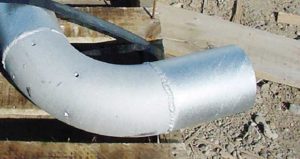
Maximizing the esthetics of hot-dip galvanized steel is a team effort. Communication throughout the process is a critical step to achieving a successful AESS finish with hot-dip galvanizing. Practices followed by the designer/architect, fabricator, and galvanizer will have a significant impact on the final finish. The following are a summary of best practices that should be employed throughout the production process.
Design and specification
There are a few considerations in the overall design of the steel before fabrication that can have a significant impact on the overall galvanizing finish. These decisions are often made without considering the significant impact it may have on the appearance and without the galvanizer’s knowledge or input. Communicating early in the project with the galvanizer and referencing ASTM A385, Standard Practice for Providing High-Quality Zinc Coatings (Hot-Dip), are a great start for the architect and fabricator. However, it is likely additional design optimizations may be necessary to maximize HDG esthetics for AESS.
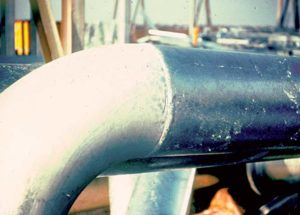
A few areas to pay special attention are:
- material selection;
- placement of vent/drain holes and lifting points and practical limitations of the galvanizer’s facility and kettle;
- weld rod chemistry and weld cleanliness; and
- thermally cut edges.
Material selection has a major influence on the hot-dip galvanized coating appearance. Combining steels with different thicknesses, chemistries, or surface conditions can result in a mixed appearance after galvanizing. If unavoidable, it is best to send the parts to the galvanizer separately and connect after galvanizing to match appearances or abrasively blast the parts before HDG to encourage the potential for a uniform appearance.
Direct communication with the galvanizer about the size, quantity, and placement of venting and drainage holes to optimize handling through the galvanizing process is another opportunity to improve the final appearance. This can minimize the potential for zinc buildup and other visual imperfections. To take it a step farther, discussing cropped corners and temporary or designated lift points can also minimize excess zinc buildup, runs, and the appearance of chain/wire marks.
Similarly, designers should discuss and keep in mind practical limitations of the galvanizing plant and kettle. It may be difficult to process large parts that come close to the dross line of the kettle when dipped, or are larger than the galvanizing kettle and require progressive dipping. AESS requirements may still be achieved, but it is paramount to discuss and work through the concerns with the galvanizer to understand what limitations the facility or kettle may have.
Two other common design and fabrication practices that can lead to different finishes are welding and thermal cutting. The CISC guide to AESS has specific requirements for weld contouring and grinding of sharp edges based on the category. However, there are additional considerations in both of these areas to maximize the HDG coating appearance.
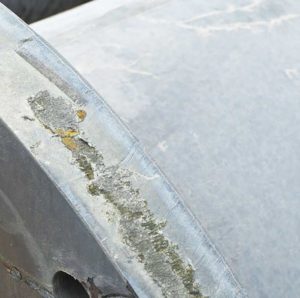
Just as steel chemistry can have a profound effect on the appearance and thickness of the hot-dip galvanized coating, the chemistry of the weld rod can also impact the appearance. If the weld material chemistry is significantly different than the chemistry of the surrounding steel, particularly in terms of silicon content, it is common to see a thicker and/or darker HDG coating present in the weld area. Therefore, it is recommended to optimize the welding material used and discuss the potential for additional smoothing after HDG, which may be necessary to meet the weld contouring and blending requirements of the AESS category.
Thermally cut edges can also present quality and appearance issues after hot-dip galvanizing. Even if the fabricator performs grinding of sharp edges in cut areas, as outlined in the AESS guide, it is often not enough to prevent the known issues of thin and/or flaking coatings. To achieve a high-quality finish along thermally cut edges and avoid field repair of the galvanized coating, it is important to designate responsibility to ensure all affected surfaces are ground up to 1.5 mm (1/16 in.) even though it is not explicitly stated within the AESS category requirement.
This is not necessarily an exhaustive list of additional design practices to maximize appearance, but the noted ones are intended to highlight some common areas and demonstrate the importance of communication amongst the parties involved. The American Galvanizers Association (AGA) has a number of free resources as well as free technical support to assist the designer and specifier to optimize their design for maximum HDG appearance.