Harness design freedom with hot-dip galvanized steel
The categorical approach
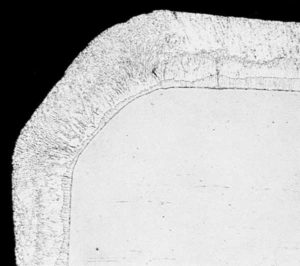
The Canadian Institute of Steel Construction (CISC) updated their guidelines for specifying AESS in 2011 to assist architects in communicating the additional esthetic requirements for galvanized AESS. These guidelines clarify the requirements and assign responsibilities between the architect, general contractor (GC), fabricator, and galvanizer. CISC’s guide established the following AESS categories for the steel based on viewing distance, type/function of the structure, and cost increase to achieve the sequentially higher appearances:
- AESS 1: Basic elements;
- AESS 2: Feature elements viewed at a distance greater than 6 m (20 ft);
- AESS 3: Feature elements viewed at a distance less than 6 m;
- AESS 4: Showcase elements with special surface and edge treatment beyond fabrication; and
- AESS 5: Custom elements with characteristics described in contract documents.
A summary of requirements for each category can be found in Table 1 of the CISC Guide for Specifying AESS. The key takeaway from this categorical approach is, requirements do not need to be equally applied across a project as AESS 1 or 2 are more suitable for elements that will not be closely seen by the public or will be covered by fireproofing, while artwork, columns, or showcase elements likely to be viewed up close or touches may require AESS 3 or 4. This allows one to optimize the quality and inspection requirements for galvanized steel to avoid unnecessary and expensive detailing/smoothing.
Assigning responsibilities beyond ASTM A123/A123M
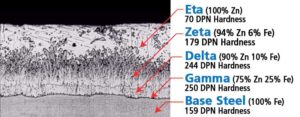
CISC’s guide to AESS primarily dictates additional requirements related to fabrication, but when specifying galvanized AESS elements, it is important to familiarize oneself with the finish and appearance requirements in ASTM A123/A123M. This will allow one to discuss and successfully assign responsibility to the fabricator and galvanizer for additional work required to meet the esthetic characteristics for the AESS categories in the project. As previously noted, there are surface conditions allowable under ASTM A123/A123M that do not affect corrosion protection, but will likely be unacceptable for the esthetic of an AESS project.
If these responsibilities are not clearly outlined in the project specifications, it is unlikely the fabricator, GC, and/or galvanizer would include the additional costs in their bid for the level of detailing required, leaving all parties unwilling to take on the additional work (and significant cost). The result of poorly written specifications is often galvanized steel delivered to the jobsite do not meet expectations or the specified AESS category. To avoid this discrepancy, it is best to include all the required information in specifications—at least call out the project is AESS and highlight areas where discussion may be necessary. It is also advisable to plan a pre-job meeting with the galvanizer, fabricator, and GC to explicitly review and assign requirements that are beyond ASTM A123/A123M to ensure they are included in the bid and contract award.
Additionally, it is best practices to set out in the specifications a prefabrication meeting to review the specifications, as well as a requirement for a mockup, to be approved by the architect, in order to establish an acceptable quality.
Although there are requirements in the AESS guide for visual samples to be used to demonstrate capabilities of meeting AESS 3 or 4, architects should use caution in expecting this to replace a pre-job meeting with all parties as previously suggested. These samples will demonstrate whether the galvanizer and fabricator can provide a galvanized part with suitable corrosion protection, smoothness, installation tolerances, and overall quality. However, it is not practical to expect the esthetic finish of all galvanized articles in the project will exactly match the sample pieces.
As previously noted, the initial appearance of hot-dip galvanized steel is difficult to predict. In fact, it is possible to galvanize identical pieces at the same time resulting in different finishes or overall appearance. However, regardless of the initial appearance, all galvanized steel parts will take on a uniform matte grey appearance on exposure to the environment (wet/dry cycles) and develop the zinc patina necessary for long-term corrosion protection. The evolution of the initial HDG appearance to this soft grey typically takes place within six months to two years. If some variation in the metallic grey finish does not meet one’s expectations, it may be prudent to consider a duplex system (paint or powder coating over galvanized steel).