Guide to designing and installing commercial IGU glazing
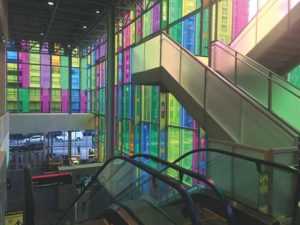
By Amy Becker
Building occupants and residents can enjoy the daylighting, great views, and comfort provided by commercial fenestration. Given continual advances in glazing technology, specifiers need expert resources to select the most optimal glazing systems for their projects. The Fenestration and Glazing Industry Alliance (FGIA) has updated the IGMA TM-3000, North American Glazing Guidelines for Sealed Insulated Glass Units for Commercial and Residential Use, which can be used for this purpose.
Armed with a detailed understanding of the different components, how they are manufactured and integrated into glazing systems, testing standards, and more, specifiers can make informed decisions when it comes to selecting insulated glazing units (IGUs).
IGU performance standards
Before delving into some relevant technical details in the updated standard, it is worth pointing out that the long-term thermal performance of a complete fenestration system depends upon the overall performance and durability of its IGU. To best ensure performance, 101/I.S.2/A440-22, North American Fenestration Standard/Specification for windows, doors, and skylights (NAFS) requires fenestration IGUs to meet CAN/CGSB-12.8-97 requirements and be certified by the National Fenestration Rating Council (NFRC) for thermal performance. This serves as the basis for a requirement in Energy Star Canada through Natural Resources Canada (NRCan).
For NFRC certification, FGIA offers the following three programs:
- Associated Laboratories, Inc. (ALI) AAMA Sealed Insulating Glass Certification Program
- IGMA of Canada (IGMAC) Certification Program
- Insulating Glass Certification Council (IGCC)/IGMA Insulating Glass Certification Program
Returning to IGMA TM-3000, the updated standard covers considerations for glass types, framing, clearances, setting blocks, spacer shims, glazing materials, glazing systems, storage and handling, glass protection, and cleaning for both double- and triple-glazed IGUs.
The document is all inclusive, addressing every aspect of glazing systems from soup to nuts. The comprehensive guide walks manufacturers, fabricators, specifiers, and contractors through all the glazing system components, addressing important points to consider, and things for which to look out.
Most helpful for specifiers are the sections on glazing materials and glazing systems where a detailed understanding is provided on all aspects and types of systems.
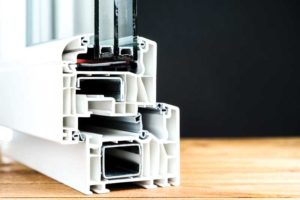
Glazing materials
The glazing materials section in IGMA TM-3000 largely focuses on sealants. For glazing systems, this typically includes silicones, polysulfides, polyurethanes, acrylics, latex, and butyls applied as gunned-in-place glazing sealants. Applications include sash joinery sealants, such as seam sealers, back bedding sealants, exterior weather sealants, heel and toe beads, butt-joint sealants, interior air seals, and structural glazing sealants.
When evaluating these systems, it is critical to check that the selected materials for the glazing system and interior of the IGU are compatible with all glazing system components. This includes the IGU sealant/sealants, which may be in contact with or encased under expected environmental conditions. For example, sealants which contain linseed oil, mineral oil, vegetable oils, certain excess plasticizers, and/or substances which release significant amounts of solvents or acids when curing, may cause IGU seal failure and/or surface contamination on the exterior or interior of the unit.