Got Hail? Proving the performance of EPDM roof assemblies
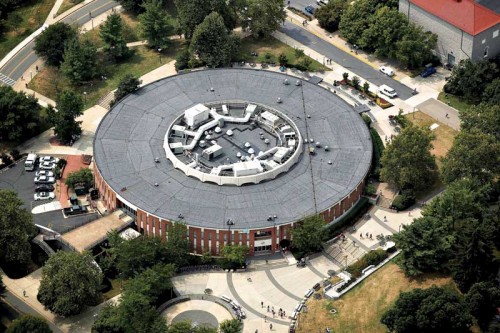
By Jim D. Koontz, PE, RRC, and Thomas W. Hutchinson, CSI, AIA, FRCI, RRC, RRP
Damage to roof assemblies from around the world from hail or other forms of physical damage (e.g. foot traffic and workmanship) results in millions of dollars of economic loss annually. Owners of properties that are largely self-insured are beginning to realize the importance of installing hail-resistant roofing systems.
Based on empirical evidence, ethylene propylene diene monomer (EPDM) roofing assemblies seem to fare very well in hailstorm events. The EPDM Roofing Association (ERA), however, desired scientific validation; it decided to embark on a hail testing program. The technical committee decided that in addition to new EPDM roof membrane material, the real question in the design, insurance, and contractor communities was over how well aged, in-situ EPDM roof covers performed.
It was determined the test sample pool would include new EPDM membrane material, new membranes that would be heat-aged, and existing in-situ material procured from existing roofs with five to 20 years of actual exposure. The major EPDM manufacturers each provided:
- 1.2 x 1.2-m (4 x 4-ft) new 1.52-mm (60-mil) material EPDM samples;
- new, but heat-aged, 1.52-mm material; and
- 1.52-mm samples from roof covers that had been exposed between five and 20 years, procured from the field.
Prior to sending the EPDM samples for testing, the material was fully adhered to various 1.2 x 1.2-m substrates: mechanically fastened polyisocyanurate (polyiso) insulation, mechanically fastened wood fibre board, and 13-mm (½-in.) plywood. Between 20 and 35 samples of each roof cover category were sent for testing.
Field experience from the examination of thousands of roofs, and through Roofing Industry Committee on Weather Issues (RICOWI) hail impact investigations (For example, the “2011 Dallas−Fort Worth Hail Storm Report” can be downloaded from www.ricowi.com), has clearly shown hail damage to a roofing system can be the result of several factors:
- hailstone diameter;
- roofing system type;
- roof cover age;
- substrate beneath the primary roof assembly; and
- surface temperature at the point of impact.
To evaluate a roofing system’s resistance to hail, these reference points have to be considered as part of a research project.
NBS impact research
In the early 1960s, the National Bureau of Standards (NBS) in Washington, D.C., conducted research by impacting roof systems with ice spheres. The group’s Sydney H. Greenfield performed this initial research and generated technical article NBS 23, Hail Resistance of Roofing Products. Referring to previous research (This came from “Hail and Its Effects on Buildings,” by J.A.P. Laurie, Council for Scientific and Industrial Research (CSIR) Research Report No. 176, Bull. 21, 1-12, published by the South African National Building Research Institute in 1960), he initially determined the freefall or terminal velocity of hail.
The technical data shown in Figure 1 indicates the free-fall velocity of the hail increases with hailstones of larger diameters. A key factor is the amount of ‘impact energy’ imparted to a target or roof surface. Simply stated:
Impact Energy = Kinetic Energy = ½ Mass * Velocity2
The mass of a hailstone obviously depends on the volume of the ice sphere and the density of the ice. The density of hailstones is typically valued at .91.
Volume of a sphere = 1.33 * Π * Radius3
A substantial difference in impact energy occurs with only slight changes in diameter. As shown in Figure 2, increasing hailstone size from 25 to 51 mm (1 to 2 in.) only represents a 100 per cent change in diameter, but the impact energy increases by 1580 per cent.
Industry impact research
Historically, the hail resistance of roofing products has been tested by dropping steel balls or darts onto the roofing product. The procedures used to impact roofing products have varied between Canada, the United States, and European organizations.
In Canada, groups have utilized the now-withdrawn impact procedure of Canadian General Standards Board (CGSB) 37-GP-52M, Roofing and Waterproofing Membrane, Sheet Applied, Elastomeric. As is the case for UL and FM Global south of the border, this procedure employed steel darts to impact targets, typically at room temperature.
Other organizations have developed impact tests that use steel darts, such as ASTM D3746, Standard Test Method for Impact Resistance of Bituminous Roofing Systems. Within the last few years, greater consideration has been given to impacting targets with ice spheres. Prior research by this article’s co-author has also reviewed the issue of ice spheres versus steel darts. (For more, see Koontz’s “Simulated Hail Damage and Impact Resistance Test Procedures for Roof Coverings and Membranes,” published by RICOWI in 2000). (The use of ice spheres, obviously, comes closer to replicating what occurs during a real hailstorm.)
Hail launcher
A key factor in performing the test is to have reproducible impact energies with each shot of ‘hailstone.’ The hail gun or launcher propels ice spheres by utilizing the quick release of compressed air from a tank to a barrel (Figure 3). To achieve reproducibility, several factors have to be taken into consideration. Consistent ‘air pressure’ is required for each shot. This necessitates controlling the air pressure to 70 Pa (0.01 psi).
Moulds for ice spheres are fabricated using precise-diameter steel spheres (Figure 4). Each ice sphere of a given diameter is then weighed to 0.01 g prior to each shot. Laboratory-grade barrels or tubes with precise internal diameters are also necessary to develop consistent impact energies. Basically, the charge (i.e. air pressure), the quick-release valve, and the bullets (i.e. ice spheres) require precise fabrication in order to achieve reproducible impact energies.
The ice spheres are initially weighed and then placed in the barrel, similar to a lead shot for a muzzle loader. As the ice sphere is pneumatically launched toward the target, the velocity is measured with a ballistics timer. The kinetic (or ‘impact’) energy is then calculated for each hail shot. The minimum kinetic energies listed by NBS are maintained within a tolerance of minus zero plus 10 per cent.
The specified slider id does not exist.