Getting the details right: building control layers
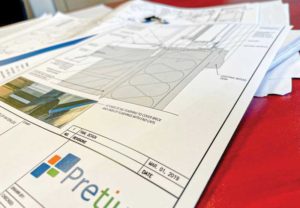
By Ian Miller, P.Eng., LEED AP, CCCA
Good building design incorporates four key control layers to separate the indoor conditioned space from the exterior—the layers of water shedding/drainage, vapour control, air control, and thermal control. Construction specifiers must thoroughly detail these control layers in the design stage. Without them, the design for those elements is left to the contractor—and their role should be installation, not design.
Inevitably, changes occur, and site conditions vary, so contractors need to make decisions in the field, but good details and adequate levels of construction oversight can help make the best building possible. Errors in the design and construction of the building control layers can lead to moisture ingress, occupant discomfort, and damage to the building. Therefore, it is important to get the details right.
Water shedding or drainage layer
The first layer at the exterior is the water shedding or drainage layer. This is the building’s first line of defence from water ingress. Many might think of this simply as the building roofing and cladding, but there is much more to it. Good building design typically involves a rainscreen, whereby the exterior cladding system does not need to be 100 per cent perfect. Instead, any precipitation managing to get past the outer face of the cladding, be it through cracks, holes, or open joints, reaches a secondary layer which drains the water back to the exterior. This is typically accomplished through both membrane and metal flashings.
Sealants should be relied upon as little as possible, since they degrade over time and form a weak point which will require regular replacement. Designers must think in three dimensions—not just what will happen at the window jamb and sill, for example, but also at the corner where the two intersect. This common weak point should incorporate proper layering of the jamb flashing over the sill upturn, as well as an end dam, for example, to prevent water ingress at the corners of the window. Sill and through-wall flashings should incorporate significant-sized drip edges to direct water out and away from the building.
Vapour control layer
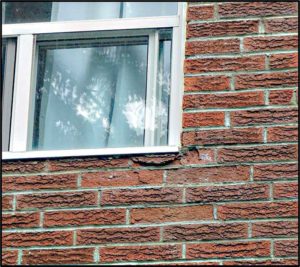
The second control layer is the vapour control layer, sometimes referred to as the vapour retarder or vapour barrier. This layer, as the name implies, controls the movement of water vapour through the wall assembly.
Physics demonstrates how water vapour always wants to move from areas of high concentration to areas of low concentration, seeking equilibrium. If one opens the door to the bathroom after steaming it up with a hot shower, the humidity from the bathroom seeks to escape to the rest of the house, increasing the humidity outside the room and lowering the humidity inside. The laws of physics also demonstrate how warmer air can hold more vapour than colder air.
Looking at the psychrometric chart, one can see how air at 5 C (41 F) can only hold roughly half the amount of moisture at 100 per cent humidity as air at 15 C (59 F), and approximately one quarter of the moisture as air at 25 C (77 F). Air at 20 C (68 F) and 40 per cent relative humidity (RH)—relatively comfortable indoor conditions—reaches 100 per cent humidity, also known as its dewpoint, when cooled to 6 C (43 F). Cooled any further, and the air can no longer hold the moisture, which is deposited as condensation.