Galvanized reinforcing steel in precast concrete
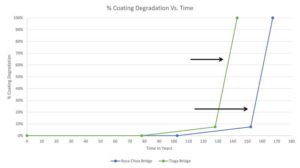
There are, however, situations where the galvanized products need to be assembled, cut, and/or fabricated in the field. For these instances, it is important to use rebar produced by either a proprietary method or the continuous process. Both yield a thinner coating comprised mostly of the pure zinc eta layer, which is ductile and stretches during forming.
Lap lengths
If overlapping of galvanized rebar is required, it is important to know the same requirements for black/bare bar apply. In studies conducted by the University of California Berkeley, the bond strength of galvanized bars is equal to or greater than black/bare bar (Figure 3).
Abrasion and impact resistance of galvanized coatings
The zeta and delta alloy layers are harder than many base steels (Figure 6). These alloy layers offer excellent abrasion resistance during transport, placement, and severe service conditions, meaning special handling procedures are not required.
Corner and edge protection
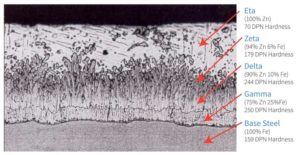
Since galvanizing is a total immersion process, all areas of the product are coated, including hidden or hard to reach places. Galvanized coatings on edges and corners are at least as thick, and sometimes thicker, as on other parts of the product. Unlike epoxies or spray-applied coatings, the coating does not thin out on edges and corners due to the formation of an alloy layer. These areas are where protection is typically needed the most (Figure 7).
Welding of galvanized steel
Welding can be accomplished by either grinding away the zinc coating and directly welding the base metal, or by welding through the galvanized coating. Materials that have been galvanized may be welded easily by all common welding techniques. Generally, anything that can be welded before galvanizing can be welded too; but some minor changes to the technique need to be incorporated to insure full weld penetration. These changes are intended to allow the galvanized coating to burn off at the front of the weld pool.
Dissimilar metal forms in contact with galvanized rebar
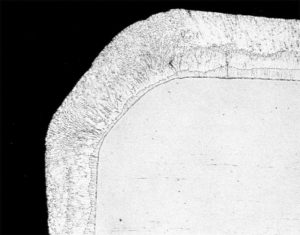
Zinc is anodic to most metals commonly used in construction (i.e. it sacrificially corrodes to protect the metal it is in contact with). Metal forms should be electrically isolated from the galvanized rebar by non-conductive spacers to prevent dissimilar metal reactions during the concrete curing. If metal forms are not isolated from the galvanized rebar, then zinc ions can be released from the galvanized coating to try to protect the metal form, resulting in a change in the concrete appearance near the galvanized bar placement.
Since types of cement with naturally low-occurring levels of chromates may react with zinc, it is important to ensure forms and supports are not removed before the concrete has developed the required strength to support itself. Normal form removal practices may be utilized if the cement contains at least 100 ppm of chromates in the final concrete mix or if the HDG bars are chromate-passivated according to ASTM A767. Too little chromate may allow the zinc to react with hydrogen in the water of the concrete mix, thus causing bubbling, which makes its way to the surface and results in poor concrete quality almost immediately.
Conclusion
Design considerations of reinforcing steel durability in precast concrete for specific exposure conditions, lowest life-cycle cost, and demonstrated performance are paramount in the decision-making process used by architects and specifiers. HDG reinforcing steel offers an objective option, and with some research into existing projects, architects and specifiers may just have found the best solution for
their design.
For 26 years, Philip G. Rahrig has been the executive director of the American Galvanizers Association, working in all facets of market/product promotion and positioning, as well as in technical support. Additionally, he is responsible for worldwide co-ordination of objectives with international organizations with common industry interests. His prior experiences include 10 years with the U.S. Steel Distribution Division, Thyssen Industrial Automation, and IBM. He is a graduate of Xavier University, Cincinnati, Ohio, with a BSBA – Management and a minor in physics. He can be reached at prahrig@galvanizeit.org.