Galvanized reinforcing steel in precast concrete
By Philip G. Rahrig
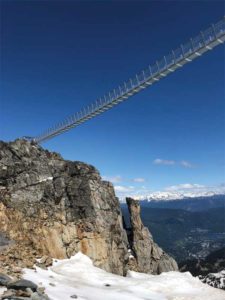
Hot-dip galvanizing has been applied to reinforcing steel in concrete used for precast panels, barriers, and bridge decks since the early 1970s. While new technologies have surfaced in decades past, none have matched the performance or economic savings that galvanized reinforcing steel has delivered. To comprehend how and why, it is important to understand the intrinsic properties of zinc in concrete, the corrosion mechanisms that are at play in chloride-rich exposure conditions (proximity to salt water/mist, road salts used for de-icing), what the sacrificial (anodic) properties of zinc mean for precast forms made of dissimilar (non-zinc) metals, and the flexibility in fabrication, handling, and placement of hot-dip galvanized (HDG) rebar.
Hot-dip galvanizing process and coating metallurgy
Unlike paint coatings that form an adhesive bond with the underlying steel, galvanized coatings develop a metallurgical bond with the steel. This occurs because when steel is placed in a molten zinc bath heated to approximately 454 C (850 F), the iron diffuses out of the steel and forms a series of iron-zinc alloy layers. The iron and zinc become metallurgically bonded together at about 24,821 kPa (3600 psi). However, for these intermetallic layers to form properly, the steel must be prepared and processed in a specific sequence. The galvanizing process consists of three basic steps (Figure 1):
- surface preparation;
- fluxing; and
- galvanizing.
Each of these steps is important in obtaining high-quality HDG coatings because if the steel is not white (i.e. free of iron oxide [rust], and organic material such as oil, dirt, and grease) the iron and molten zinc will not react with each other.
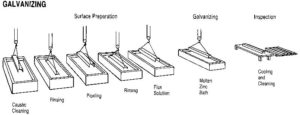
Surface preparation
It is essential the steel surface is clean and uncontaminated for a uniform, adherent coating. Surface preparation is usually performed in sequence by caustic (alkaline) cleaning, water rinsing, acid pickling, and water rinsing. The caustic solution is used to clean the steel of organic contaminants such as dirt, paint markings, grease, and oil, which are not readily removed by acid pickling. Scale and rust are normally removed by pickling in hot sulfuric acid at 65 C (150 F) or hydrochloric acid at room temperature. The rinsing in a water bath after each step simply prevents contamination of the liquid in the next step of the process.
Fluxing
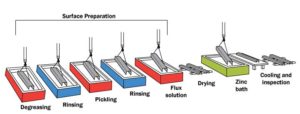
The final steel cleaning is performed by a flux solution of zinc-ammonium chloride. Flux is required at this step to remove any oxidation that may take place after the steel is taken out from the acid cleaning bath, and to prevent further oxidation of the clean steel between the time it takes for the product to dry and its immersion in the molten zinc. Steel must be completely dry prior to immersion in the molten zinc. If not, zinc will violently splash out of the kettle. The method of applying the flux to the steel depends on whether the ‘wet’ or ‘dry’ galvanizing process is used. Dry galvanizing requires the steel to be dipped in an aqueous zinc ammonium-chloride solution prior to immersion in the molten zinc bath and then thoroughly dried. This ‘pre-flux,’ as it is called, prevents oxides from forming on the material surface before galvanizing. Wet galvanizing uses a flux layer of zinc ammonium-chloride floating on top of the more viscous molten zinc. The steel is passed slowly through the flux and any oxides are removed.
Galvanizing
The steel to be coated is immersed in a molten zinc bath maintained at a temperature of 435 to 460 C (815 to 860 F). Typical bath chemistry used in hot-dip galvanizing contains a minimum of 98 per cent zinc with a variety of trace elements or alloy additions. These additions, which could include lead (up to 1.2 per cent), aluminum (up to 0.005 per cent), tin (about 0.05 per cent), nickel (up to 0.1 per cent), and bismuth (about 0.1 per cent), can be mixed into the zinc to enhance the appearance of the final product or to improve the drainage of the molten zinc, as the material is withdrawn from the bath.
Galvanizing processes
Three different galvanizing processes are used today to produce HDG rebar, but it is important to note all three produce a zinc coating durable for decades by isolating the bar from corrosive chlorides in the concrete. Production to exacting ASTM specifications ensures consistent performance from galvanizer to galvanizer.