From waste to resource: Designing for disassembly
By Sanaz Mani, LEED AP, Architect AIBC
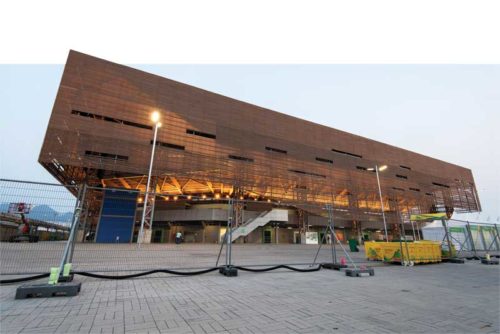
When thinking about sustainable buildings, their CO2 emissions, energy consumption, embodied carbon, etc., come to mind. However, there is another contemporary challenge that rarely gets any attention but embodies all the above, and that is construction, renovation, and demolition (CRD) waste. Construction waste includes any debris produced during construction, such as cut-offs of materials and packaging waste. The significant construction waste that may lead to up to 30 per cent of materials wasted during construction increases the overall CO2 emissions and energy consumption, embodies project carbon, and increases construction cost.
In 1907, Leo Baekeland invented the first plastic called Bakelite, the first fully synthetic plastic, meaning it contained no molecules found in nature, by combining two chemicals: formaldehyde and phenol.1 Since then, the products used in buildings have changed from natural products such as wood, stone and brick to complicated synthetic products with components that are hard to pronounce. Today, plastics and chemicals are an important component in what makes up our buildings, services, furniture, and tools. As a result, the challenge has shifted from preserving architecture to ways of disposing of it without creating catastrophic implications for the environment.
Release of dust and chemicals
People are aware of microplastics in oceans, asbestos in old gypsum walls, lead in paint, mercury in light bulbs, and CO2 detectors, and the damage they continue to inflict on wildlife, users, and construction workers, but there is still a lot unknown about new materials specified for projects. According to the Toxic Substances Control Act (TSCA) in the U.S., out of 82,000 chemicals registered, only 650 have been monitored by the EPA Toxic Release Inventory, and only five have ever been banned.2 According to Perkins + Will’s precautionary list of materials,3 any of today’s indispensable construction products, such as stains, sealants, and fire stoppings, are suspected to contain hazardous chemicals. Currently, these products are being discarded in landfills.
Depletion of our natural resources
The construction industry has been found to consume approximately 40 per cent of raw materials globally. “While some municipalities have construction waste bylaws, in Canada, an average of only 16 per cent of construction and demolition waste is diverted from landfill or incineration, with most being ‘downcycled’ to a lesser use.”4
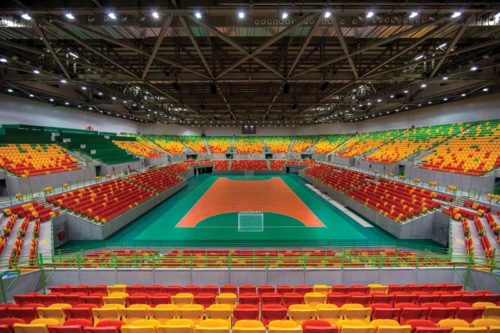
High cost of managing the construction and demolition waste
Managing this ongoing waste stream has become a multibillion-dollar challenge for governments worldwide. Statistics Canada states5 that Canada spent $3.2 billion in waste management in 2012 alone. In Canada, construction and demolition waste is one of the largest contributors to municipal solid waste, which is 3.62 million tonnes (4 million tons) or 12 per cent of the solid waste stream generated in Canada. According to the City of Vancouver,6 the numbers are higher at about 22 per cent of the material in the landfill.
What is a solution to reducing CRD waste?
One solution to reduce the waste and turn the demolition waste of the project into a resource in architectural design is a relatively new concept introduced in the 1990s called “design for disassembly,” or DFD for short.7 This sustainable design strategy invites architects to design buildings that address the issue of construction and demolition waste by proposing two strategies: advocating for the building to become fully disassembled at the end of life to be recycled or reused; and by proposing ways for the building to be repaired, upgraded, adapted to ensure the building’s longevity. The principal ideas of zero-waste are reduce, reuse, and recycle put into architectural design. There is a shift in thinking and wanting to retain, fix, and adapt rather than discard.
A CSA Group guideline, Design for Disassembly and Adaptability, or DFD/A DFD/A, was introduced in 2006 to help architects in Canada apply and measure their success in designing for disassembly. DFD principles introduced in the CSA guideline can be applied to the whole building down to the smaller details, such as the cladding or interior finishes.
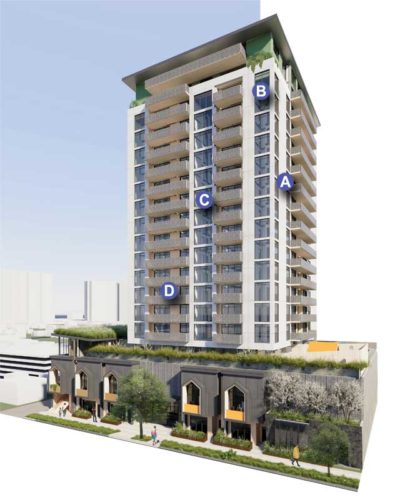
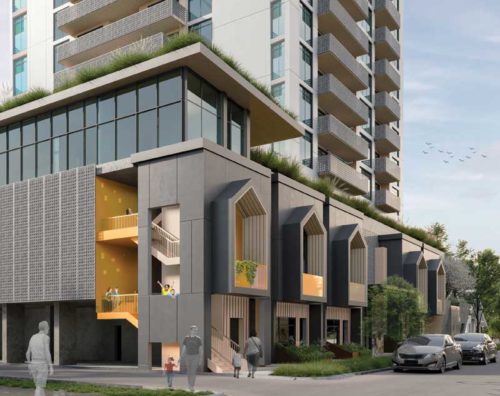
Disassembly and adaptability principles
Adaptability
This principle aims to increase a building’s longevity. This kind of building needs to be versatile so it can be changed into a different use or expanded vertically or horizontally to accommodate more area. Examples include creating blank walls on one side of the building that do not contain any MEP services and are built with panels mechanically fastened and easily removable, allowing the building to grow from one side.
Accessibility
DFD recommends keeping each building component accessible so it can be fixed, replaced, or upgraded without damaging other parts. In a traditionally built space, to fix a leaky pipe, design teams need to demo parts of the building to access the services behind. Having minimal mechanically fastened interior finishes that can be removed during repairs or upgrades can help reduce waste.
Documentation
It is important to document a building’s disassembly plan in a way that is still legible for future generations. Documenting material and manufacturer information helps increase the chance of reusing and recycling components. As seen today with asbestos, its existence cannot be determined without expensive and timely lab tests.
CSA guidelines list and explain other principles, including durability, exposed connections, independence of components, and inherent materials that help achieve a building that can fit into a circular economy. They also offer tools to measure success.
DFD projects
As an example of a building designed to be disassembled and reused, consider the Rio 2016 Olympic Handball Arena by OA. The modular building components were disassembled after the Olympics and reused to build four schools in Rio de Janeiro.8 The Arena and the schools were designed at the same time. Attention was given to the methods of construction and assembly of the modular components of the arena building to ensure minimum construction waste during the assembly of the four schools. The grid for the floor plates and the roof were all designed from the outset for both buildings, so the panels on the facade and the floor and roof could be easily relocated so the modules could work for both buildings.
A presentation centre in Squamish, B.C., was disassembled in six days and was reassembled as a laneway house in Salt Spring Island. More than 99 per cent of the materials were reused and diverted from the landfill.9
Conclusion
Douglas Coupland’s art project at Vancouver Aquarium made a big impression on the author. The Vortex depicts a Japanese day-fishing boat, which vanished in the 2011 Tohoku earthquake and tsunami and reappeared on Haida Gwaii’s shores in 2017. It features children standing aboard, reflecting on how today’s youth is consuming the waste that ends up in the oceans.10
The ideas represented in the design for disassembly come with many challenges, but as a whole, they provide a valuable tool and a glimmer of hope.
Brenda Marten from Light House, a company specializing in construction management and general contracting services, who teaches the DFD/A course at the British Columbia Institute of Technology (BCIT), notes: “When we look at the analysis from Watching Our Waste, it becomes very clear that current construction practices are not sustainable. If we are to meet our carbon targets now and in the future, we need to abandon some of our 20th-century building practices, such as constructing most of our buildings on site and demolishing our existing buildings without regard for the materials embedded in them. Regulators should be aware that much higher diversion rates than currently being achieved are possible and should consider setting targets and creating bylaws accordingly. Beyond diversion, we should be embracing prefabrication, modular construction, purpose-built components, and the design of buildings for durability, adaptability, and disassembly at end-of-life.”13
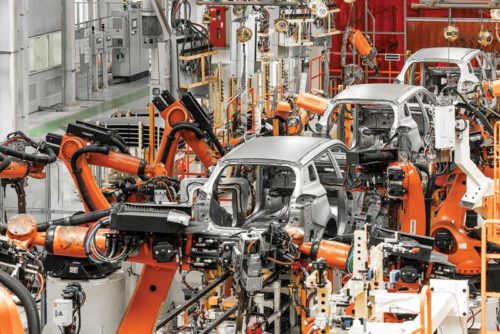
Notes
1 Read the article by Kevin Shah, “A Brief History of Plastic” at medium.com/@thisiskevinshah/a-brief-history-of-plastic-2336f7bbdb96.
2 The five banned chemicals are lead, asbestos, DD, phthalates, bisphenol A.
3 Perkins+Will Architecture firm has produced a precautionary list to browse substances of concern by project type, product type, CSI specifications, and hazards, see transparency.perkinswill.com/lists/precautionary-list.
4 Refer to the Canadian Council of Ministers of the Environment—Guide for identifying, evaluating, and selecting policies for influencing construction, renovation, and demolition waste management, 2019.
5 See the statistics at 150.statcan.gc.ca/n1/pub/11-402-x/2011000/chap/gov-gouv/gov-gouv01-eng.htm.
6 Learn more at vancouver.ca/doing-business/construction-and-demolition-waste.aspx.
7 For more information, read archdaily.com /943366/a-guide-to-design-for-disassembly.
8 See note 7.
9 Review the case study by Zosia Brown, “Design for deconstruction: Nexii circular economy case study,” 2022.
10 It is estimated more than one truck load of plastic ends up in the oceans every minute. CBC News explores impacts of plastic waste in oceans in Vancouver Aquarium Exhibit, read the article at cbc.ca/news/canada/british-columbia/douglas-coupland-explores-impact-of-plastic-waste-in-oceans-in-new-vancouver-aquarium-exhibit-1.4664515.
11 Micro plastics have been found in human blood for the first time in 80 per cent of people tested according to Prof Dick Vethaak, an ecotoxicologist at Vrije Universiteit Amsterdam in the Netherlands.
12 Refer to the document, “Watching our waste: Executive Summary” by Light House.
Author
Sanaz Mani, LEED AP, Architect AIBC, is the CEO and founder of Mani Architect, a boutique architecture firm in West Vancouver, B.C. She holds a Master of Advanced Studies in architecture from the University of British Columbia (UBC) and is dedicated to sustainable design and environmental conservation.