Four ways to eliminate joints in wide-slab concrete floors
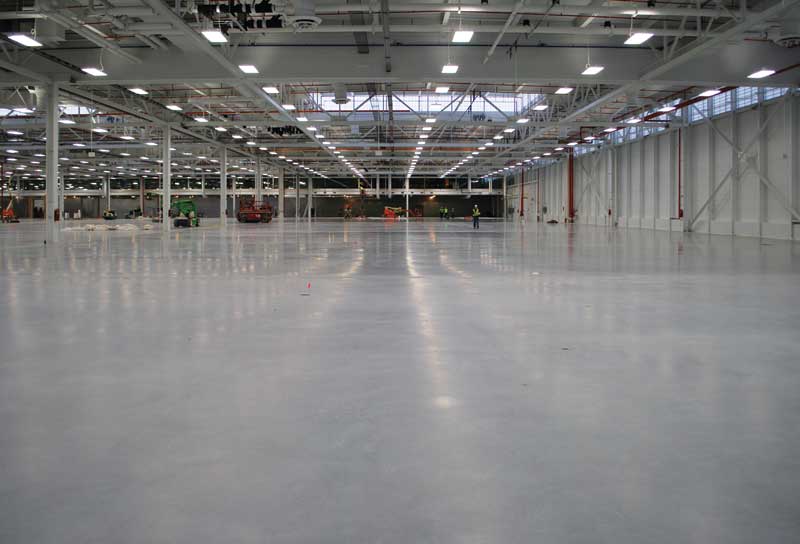
By George Garber
What is it about ground-supported concrete floors that make owners and tenants complain? The answer depends on where the floors are located. In residential basements and garages, cracks generate the most complaints. In office buildings and retail stores, moisture-related problems top the list. In industrial buildings—warehouses and factories—the most common issues involve joints.
Joints are the seams dividing a concrete floor into multiple slabs. Modern industrial floors contain both construction joints and sawn joints. (The word ‘joint’ can also describe the location where a floor slab meets another building element such as a wall or column. The construction methods described here do not eliminate that kind of joint.) A construction joint, also known as a formed joint or a day joint, marks the line between two concrete pours made on separate days. A sawn joint is located within a pour, and is made by sawing partway through the concrete after it has hardened. The sawcut creates a weakened vertical plane where the concrete can easily crack. The goal is to control cracks by keeping them under the sawcuts, but this is not always realized. In most industrial floors, sawn joints far outnumber construction joints, and their sole purpose is crack control.
Joints can do a good job of controlling cracks, but there is a price. They are costly to make and maintain, and can have numerous issues including:
- spalling under traffic (Figure 1);
- faulting that leaves one side higher than the other (Figure 2);
- creating exposed edges where delamination can start;
- allowing slabs to curl, making them less flat; and
- reducing a floor’s load-bearing capacity, because every joint creates two slab edges (and slabs are weaker near the edges).
Given all these problems, it would make sense to try and eliminate these joints. Some designers do try, but most do not. The typical industrial floor in Canada still relies on closely spaced joints as its primary method of crack control. This is the same method used 50 years ago. Previously, it was common to space joints about 6 m (20 ft) apart, but these floors sometimes cracked between joints, so designers began recommending closer spacings. For a while, the standard rule of thumb for joint spacing was not to exceed 36 times the slab thickness. Meaning a 150 mm (6 in.) thick slab would have joint spacings up to 5.4 m (18 ft).
Today, the American Concrete Institute, (ACI) 360R-10, Guide to Design of Slabs-on-Ground, recommends joint spacings that would have previously been considered absurdly close. For a slab 150 mm (6 in.) thick, made of concrete with unknown drying shrinkage—a common situation—ACI 360 now calls for joints no more than 3.6 m (12 ft) apart. Even very thick slabs are subject to a maximum joint spacing of 4.5 m (15 ft) unless the concrete is tested for shrinkage and proves to have an ultimate drying-shrinkage rate below 0.078 per cent.
Cracks are still being controlled, but floors are still riddled with joints. Is this progress?
To remedy this situation, there are at least four ways to build industrial floors with far fewer joints. They include:
- continuous heavy rebar;
- shrinkage-compensating concrete;
- post-tensioning; and
- steel-fibre reinforcement.
All four methods allow wide-slab (or ‘extended-joint’) construction, with joint spacings greater than 15 m (50 ft). Some call them jointless or joint-free floors, but these terms are inaccurate, because only 70 to 90 per cent of joints are actually eliminated.
Continuous heavy rebar
The continuous heavy rebar method was borrowed from highway engineers, who refer to it as continuously reinforced concrete pavement (CRCP). This method reinforces the floor with deformed steel bars running continuously the full length of the slab. In CRCP highways, the reinforcement ranges from 0.5 to 0.8 per cent of the slab’s cross-sectional area. Designers who adapted this method for interior floors around 1990 chose the low end of the range at 0.5 per cent, and it has been successful. ACI 360 endorses this, stating:
to eliminate sawcut contraction joints, a continuous amount of reinforcement with a minimum steel ratio of 0.5 per cent of the slab’s cross-sectional area in the direction where the contraction joints are eliminated is recommended.
The reinforcing steel is typically placed about 50 mm (2 in.) below the floor surface. Continuity is essential, so bar ends must be carefully lapped. A publication from the U.S. Federal Highway Administration (FHWA), Technical Advisory 5080.14, contains lap details and other useful information. (For more, see the United States Department of Transportation, Federal Highway Administration, Technical Advisory 5080.14 paper, Continuously Reinforced Concrete Pavement.)
Compared to other methods of wide-slab construction, continuous heavy rebar has several powerful advantages, including:
- unlimited joint spacing;
- elimination of a slipsheet under the slab;
- ability to structurally tie the slab to other building elements (e.g. walls); and
- no need for special skills or unusual materials.
However, there is one large and often fatal drawback that needs to be considered. Continuous heavy rebar does not prevent cracks. On the contrary, it creates them. The goal of this method is to relieve shrinkage stresses at a large number of very narrow cracks. The distance between cracks varies by project, but can be as little as 300 mm (12 in). Crack width also varies, but usually stays below 0.3 mm and never exceeds 0.5 mm unless there is, by mistake, a break in the continuity of the rebar (Figure 3).
Though CRCP highways are common in Canada, industrial floors designed along the same lines remain scarce, probably because floor users have a strong prejudice against cracks. It could be argued a tight crack with rebar running through it is not a defect and will cause less trouble than a joint. While this is a reasonable argument, many users will not accept it.
The specified slider does not exist.