Fluid-applied Flashings: Fully adhered instead of self-adhered
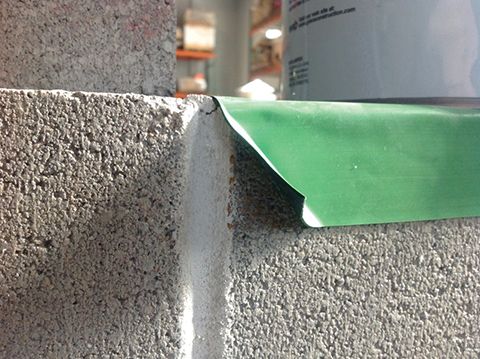
Fitting a flashing to a building in this complicated manner can affect long-term performance. Even though most of these flashings have reputations as high-quality products, the intended installation process and the actuality of correct installation tend not to directly mirror one another. If any of the previous installation steps are bypassed, the products should function as they were designed, but the method of installation can affect the performance.
Each step has a unique importance to ensure the tape functions as intended. Tape alone ‘sticks’ to some wall substrates better than others, which is why manufactures recommend priming the surface first. If this step is skipped, it may not adhere well. Additionally, if the tape is not completely flat around the edges, it may allow water to enter the building. This is why a mastic or sealant is recommended as the final step.
A building will not remain perfectly still throughout its lifetime, as the ground below it shifts, or as it expands and contracts with the weather and temperature. Flashing tapes are typically designed to account for this movement, but if not installed exactly to the manufacturer’s specifications, problems could arise five, 10, or 50 years in the future. If the various pieces of tapes are improperly lapped, or if fish mouths and wrinkles are present, the tapes could lose adhesion and allow moisture to enter the building. This works in the same way a bandage does. A cut on the knuckle can be covered by a bandage, but if the hand is always in use, the product will start to peel away. Windows suffer from similar adhesion and leaking problems, but leaks are rarely caused by the defects in the window.
Self-adhered flashings require more time to properly install than other new methods, such as the fluid-applied flashing products introduced over the last few years, because additional installation steps—priming, installing, and terminating with mastic—are required with self-adhered flashings. These additional steps also require the use of more materials than a fluid-applied flashing and entail proper sequencing of laps to ensure water is directed correctly throughout the building’s lifetime. It takes a considerable amount of time to properly splice, bend, and fold in the appropriate areas. Although fluid-applied flashings are relatively new, they still conform to the same flashing standards. In fact, a study by Charlie Saul of Aquatech Consultancy suggested fluid-applied products actually exceed most code requirements for flashings.
Fluid-applied flashings
Like their self-adhered counterparts, fluid-applied flashings have many different chemical formulations that allow them to perform in multiple types of construction and different environments. Instead of pre-determined sizes and shapes, fluid-applied flashings may come in sausages, cartridges, or even pails. Before applying these flashings, the surface must be dry and the materials must be applied at the proper thickness. Some will require a primer while others do not. Even if the material requires a primer, the fluid-applied flashing application is quicker than tape application.
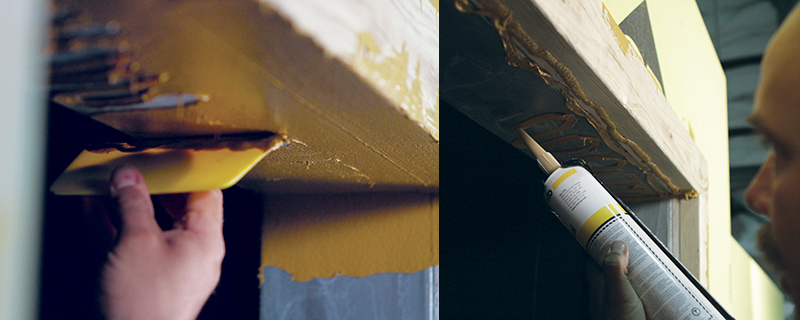
Installation
Fluid-applied flashings are incredibly easy to install. The liquid material is applied to the substrate and is spread across areas requiring protection. Liquids take the shape of whatever substrate they are in or on—meaning wrinkles and fish mouths are no longer a concern. Further, there is no reason for pieces to lap onto each other. The liquid chemistry results in all the material applied becoming a single monolithic membrane. Generally, these types of products form a chemical bond with whatever substrate they are applied to—meaning long-term adhesion is less of a concern than before.
Like self-adhered flashings, there are some materials that may inhibit proper bonding of a liquid flashing. It is important to ensure substrates are clean before installation. Some liquid flashings have temperature requirements for surface and ambient conditions to make sure that these materials bond properly to the substrate. However, some of the new liquid flashing technologies allow for a much wider range of installation temperatures and in some cases can even be installed in wet conditions. Liquid flashings also tend to be highly flexible throughout the building’s lifetime, and normal building movement should not prevent them from protecting against moisture intrusion.