Floor vibration control strategies for adaptive reuse of buildings into labs
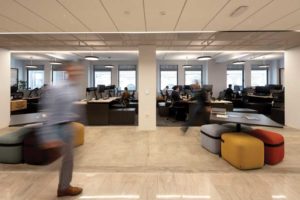
By Brad Pridham, Ph.D., P.E., Michael Wesolowsky, Ph.D., P.E., Rabih Alkhatib, Ph.D., P.E., and Sami Rahman, M.A.Sc., P.E.
Over the past five years, the commercial real estate industry has witnessed a surge in the acquisition of properties to be repurposed as laboratory space for the health sciences sector. This has involved renovations of buildings across North America to create tenant space suitable for housing state-of-the-art research tools and programs.
A key challenge for architects and engineers has been the development of strategies for vibration control, where it is necessary to achieve a base level of performance suitable for life sciences. Success in most cases requires an evaluation of the vibration performance of the base structural system, followed by an assessment of options that can result in compliance with performance targets.
Vibration sources of concern
Floor vibration problems in reuse scenarios are typically caused by:
- Occupant activity, such as walking, running, dancing, and exercising, which results in dynamic forces transmitted to the floor during each footfall.
- Building services, such as pumps, fans, and generators with vibrations during operation that can transmit to the structure, resulting in structure-borne noise and tactile levels of vibration.
- Environmental sources, such as roadway and railway traffic and vibration activity in nearby buildings that transmit through the ground into the building.
While occupant activity is arguably the most problematic source of vibration on supported floors, it is not uncommon during reuse scenarios for spaces to be sited close to building equipment or exterior roadways, resulting in increased exposure to vibrations.
Vibration criteria
Criteria for floor vibration are specified based on the space’s use and occupancy. Many of these evolved from the isoperceptibility curve, which represents the threshold of vibration perception for humans (foot-to-head vibration direction) over the 1 to 80 Hz frequency range.
The y-axis is the root-mean-square (RMS) vibration acceleration level—typically computed for a one-second time window. Floor vibration levels having magnitudes greater than this curve will be perceptible to most people. The flat portion between 4 and 8 Hz represents the frequency range of people’s greatest sensitivity to vibration.