Five common mistakes made in the façade industry

Mistake #2: Not designing for the coefficient of expansion and contraction
Façade materials expand and contract. Every building material has a unique value for coefficient of expansion/contraction. A critical design failure is ignoring these fluctuations in façades and their substructures. Both systems engage in a dynamic dance with one another, and this is largely attributed to changes in temperature and humidity. Over the last 10 years, the author has witnessed façade cracking, warping/oil canning, and fastener failures. As the global climate changes, higher frequencies of extreme weather are placing greater stress on buildings, and, specifically, façades that are at the frontlines 100 per cent of the time.
This all points to designing dynamic building envelopes that can expand and contract with the environmental fluctuations facing it. Façade materials can be hung on a substructure in two ways: exposed or concealed fastening. Both of these methods can address the dynamism required to thwart failure. Proper design and installation of the systems is critical. Taking a look at a typical face fastened (exposed) system, which is less expensive than concealed, fixed and floating points of fasteners are required to hold the façade skin to the substructure. This method ensures the façade skin is held back sufficiently to the substructure, but the nature of the floating points allows the panel to respond to expansion and contraction without locking up and binding. The fixed point(s) positions/locates the panel, where the floating points make up the majority of the fasteners. Floating points are created by over-drilling the fastener hole diameter by only a few millimeters larger than the fastener diameter. The amount of fluctuation is rather small in comparison to the overall size of the façade skin module, but repeated stress between the fasteners and the panel without the float compromises both the façade skin and fastener. This is a very simple and affordable procedure, as well as an empirically proven methodology addressing an unavoidable condition, given the materiality in contemporary façades, typical building practices in North America, and the environmental conditions structures are subjected to. Overtightening of fasteners is a detrimental, easily avoidable issue, and is essentially the equivalent of increasing the number of fixed points and removing float. With the help of available accessories, such as cordless rivet guns and rivet setting adapters. Rivet assemblies have proven to be the easiest to moderate and the most promising for success. Emphasis on cordless rivet guns is key. The use of pneumatic guns and compressors drives the rivets with far too much force and creates overtightening. The use of threaded fastening solutions (screws) is another option to the rivet but it leaves the fastener tension in the hands of the installer and the impact driver. Impact drivers do not have clutches, so the tension is completely arbitrary. This can be disastrous. While many façade skin manufacturers endorse the use of threaded fasteners, the assumption is installation crews will use ‘all means necessary’ to modulate fastening tension so the ideal conditions are met. While this introduces a subjective element, it is this author’s opinion this is an unrealistic and unfair expectation of installers who are usually under time constraints or, in some cases, battling adverse weather conditions of either extreme cold or heat.
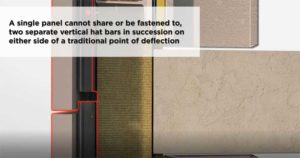
Concealed fastening systems inherently have a design allowance for expansion and contraction. They also cost more than exposed fastener systems. At a premium of roughly 30 per cent upcharge (relative supply and installation cost) for concealed systems, the exposed fasteners, with the proper installation methodology, are economical and promise success.
Mistake #3: Substructure design omissions and installation shortcomings
Façade systems are suspended outside of the superstructure. In Canada, the substructure façade skins are typically fastened to 18-ga galvanized metal, which is light when compared to structural steel. The challenges faced here are many fold.
As mentioned earlier, a vertical cavity should exist directly behind the panel for good ventilation. Working from the panel back there should be a vertical ‘hat bar’ to support the panel. A horizontal plane of a Z bar, or equivalent will support the hat bar and insulation (assuming there is outboard insulation). In many cases, specific RSI values will be required, thus demanding the implementation of a thermal clip. The clip should be a part of the horizontal member, and best-case scenario would be for the product to be adjustable for sub wall misalignment.