Fireproofing hot-dip galvanized steel
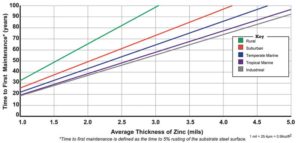
Some SFRMs, such as cementitious coatings, are unable to exclusively provide significant corrosion resistance in aggressive environments, or can be subject to corrosion under fireproofing when damaged or on retention of moisture in the pores of the SFRM. The resulting products of steel corrosion (e.g. iron oxides) are more voluminous than the base steel (rusting steel expands), and the ensuing pressure can lead to delamination of SFRMs and failure to protect structural members during a fire (consult the white paper “Corrosion Under Insulation” by the Materials Technology Institute [MTI], published in 2012). Meanwhile, field studies conducted on the corrosion performance of hot-dip galvanized steel under cementitious passive-fireproofing materials have demonstrated the ability to provide over 48 years of maintenance-free longevity in corrosive interior environments containing high levels of humidity and/or chemical exposure (refer to “Corrosion of Galvanized Steel Under Fireproofing” by A.M. Stoneman and F.E. Goodwin). The HDG provides a barrier and cathodic protection to prevent the buildup of iron oxides, with the addition of superior abrasion resistance. However, site conditions that could result in damage to fireproofing that exposes the coating to chemical environments or solutions with pH values below three or above 13.5 are not recommended due to the rapid corrosion of the galvanized coating (refer to “Corrosion of Galvanized Steel Under Fireproofing” by A.M. Stoneman and F.E. Goodwin). In other aggressive environments, proper inspection and maintenance of the fireproofing material and replacement of any damaged material is important to prevent accelerated corrosion of the galvanized steel.
A subset of SFRMs, IFRMs purposefully char and swell dramatically on exposure to fire, and the charred layers protect the steel from a fire. Intumescent coating systems provide corrosion resistance in addition to fire-resistance since acrylic, vinyl, or epoxy primers are often specified for improved bond-strength and barrier protection. However, when IFRMs are applied over a galvanized surface using a compatible tie-coat recommended by the IFRM manufacturer, a more sophisticated corrosion resistance, known as the synergistic effect, is achieved. The IFRM coating system prevents the galvanized steel from exposure to the environment, thereby delaying the onset of zinc corrosion. In return, HDG acts as a primer for the IFRM system and prevents the occurrence of under film corrosion when IFRM begins to deteriorate and expose the galvanized surface (consult Duplex systems: Hot-Dip Galvanizing Plus Painting by J.F.H. van Eijnsbergen, published in 1994). The combined effect results in maintenance-free corrosion protection for 1.5 to 2.3 times the sum of the IFRM service life and HDG time-to-first maintenance. Further, primers applied prior to the intumescent paint layers will last 50 per cent longer in service life when applied as a tie coat over a HDG surface in comparison to when used as an IFRM primer applied over bare steel (consult Duplex systems: Hot-Dip Galvanizing Plus Painting by J.F.H. van Eijnsbergen, published in 1994).
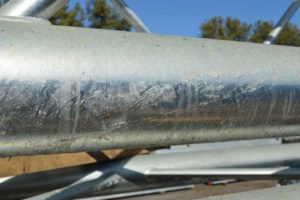
To achieve these benefits when applying IFRM coatings over hot-dip galvanized coatings, the tie coat specified for application over the galvanized surface must be approved by the IFRM manufacturer. This ensures minimum specified bond-strength requirements are met and the IFRM will perform as intended. For example, oil-based tie coats comprising alkyd and epoxy esters, or linseed oil derivatives should be avoided as these paints can saponify and eventually delaminate when applied over the alkaline hot-dip galvanized surface. On the other hand, if the tie coat is incompatible with the intumescent paint, the latter will either delaminate or develop large holes or unprotected areas in the coating when exposed to elevated temperatures (consult “Galvanizing, Primer Adhesion Test and Beyond” by Ernst Toussaint, published in 2019). To avoid these issues, passive fireproofing manufacturers can provide a list of approved tie-coat products tested for compatibility with the IFRM. Where an approved tie coat is not readily available or where field confirmation is required, bond testing and small-scale fire testing can be performed independently.
Preparing HDG surfaces for passive fireproofing application
As with any industrial coating application, proper surface preparation is key to the overall success of passive fireproofing materials applied over a galvanized surface. However, determining the steps for surface preparation can be challenging as these requirements vary by type of fire-resistive material and can further vary by manufacturer or product line. Some passive fireproofing materials (i.e. rigid board and flexible blanket systems) are mechanically fastened to structural steel, and, therefore, no specialized preparation of the hot-dip galvanized coating surface is required prior to installation. On the other hand, preparing galvanized surfaces for SFRMs and IFRMs often require additional preparations to promote adhesion, achieve the specified cohesive/adhesive bond strength requirements, and ensure fire-resistive coatings perform as intended while avoiding damage to the galvanized coating.
Cementitious and gypsum-based SFRMs require the removal of oils, grease, dirt, and debris from the HDG surface at a minimum (read the National Fireproofing Contractors Association’s (NFCA’s), “NFCA Standard Practice 200 Field Quality Assurance Procedure for Application of Spray Applied Fire-Resistive Materials (SFRMs)”, published in 2004, and refer to “Fire-resistance Ratings,” the American National Standards Institute/Underwriters Laboratories (ANSI/UL) 263-2018, Standard for Fire Tests of Building Construction and Materials). For such materials, solvent cleaning per Society for Protective Coatings (SSPC)-SP1, Solvent Cleaning, should provide sufficient preparation. Depending on the structural member dimensions and the results of bond tests conducted in accordance with ASTM E736, Standard Test Method for Cohesion/Adhesion of Sprayed Fire Resistive Materials Applied to Structural Members, additional preparations can be employed to promote the adhesion of SFRMs over HDG. Additional recommendations prior to application of the fire-resistive material may include:
- application of mechanically fastened metal lath;
- use of a bonding agent; and
- application of a primer (technically a tie coat) tested by the manufacturer for compatibility with the fire-resistive material (read the National Fireproofing Contractors Association’s (NFCA’s), “NFCA Standard Practice 200 Field Quality Assurance Procedure for Application of Spray Applied Fire-Resistive Materials (SFRMs)”, published in 2004, and refer to “Fire-resistance Ratings,” the American National Standards Institute/Underwriters Laboratories (ANSI/UL) 263-2018, Standard for Fire Tests of Building Construction and Materials).
Occasionally, failures in lightweight cementitious fireproofing have occurred when a bare metal lath is used. As the bare metal eventually corrodes, the voluminous iron oxide (Fe2O3) corrosion causes a buildup of pressure that can result in cracking in fireproofing. Where metal lath is required, the use of galvanized mesh is recommended to maximize the longevity of the fireproofing and minimize the chance for accelerated corrosion under fireproofing (refer to “Corrosion of Galvanized Steel Under Fireproofing” by A.M. Stoneman and F.E. Goodwin).