Finding the Right Support: Guidelines for specifying rooftop photovoltaics
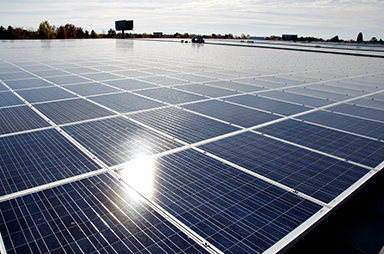
By Mike Ennis, RRC
Low-slope roofs offer an economical and sustainable platform for renewable solar energy in the form of photovoltaic (PV) systems. However, the popularity of renewable energy sources does not change the fact the roof designer’s primary goal will always be to protect the building’s contents and occupants from the elements. In this regard, roofing professionals need to anticipate the potential risks associated with the installation of a roof-mounted PV array. This sort of due diligence is particularly important when installing solar PV systems on existing warranted roofs.
With the installation of rooftop PV, the roofing system becomes more than just a roof—it becomes a permanent platform for the continuous operation, service, and maintenance of the PV system. Ideally, the new or existing roofing system should last as long as the array, and also be designed to minimize the need for major repairs or replacement that could cause leaks and/or compromise the PVs’ continuous operation.
In Canada, the demand for PV has grown significantly over the past five years. For example, the PV module market increased from a meager 6.94 MW in 2008 to 67.3 MW the following year. Continued aggressive growth of PV systems is predicted as existing legislative support of solar is maintained and the PV industry meets or exceeds government targets on photovoltaic power per inhabitant. If this continues, Canadian specifiers can count on yet another complex element being added to their to-do lists on an increasing number of new and reroofing projects.
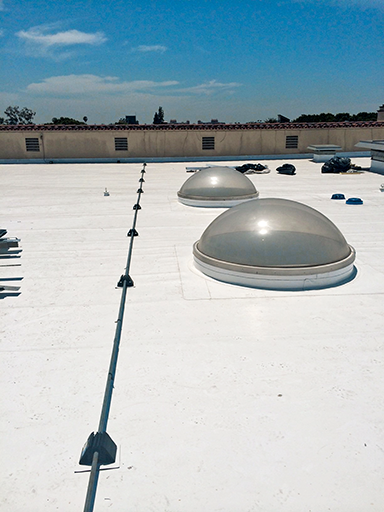
Help is on the way
Fortunately, industry associations like Single-ply Roofing Industry (SPRI) are helping specifiers meet the PV challenge with various guidelines designed to provide maximum protection for the roof and maintain its warranty coverage. In September 2013, the group’s technical committee and board of directors approved Technical Bulletin 1-13A, “Summary of SPRI Membrane Manufacturer Photovoltaic (PV)-ready Roof Systems and Services,” which contains general guidelines related to PV-ready roof assemblies. In April 2014, SPRI released a technical bulletin—1-14, “Recommendations for Rooftop Supports”—that zeros in on some potentially problematic performance issues with rooftop supports. Specifically, these relate to surface-mounted, non-structurally integrated rooftop support systems that include solar PV systems.
The installation of a PV system on an existing warranted roof raises many important questions for the roofing professional and building owner. Forexample, can the roof accommodate the added weight of the PV array?
Obviously, before property owners decide on a specific solar-power system, they need a qualified architect or engineer to determine whether their roofs are sturdy enough to support the additional loads put on the existing roof structure by the solar array.
An average solar panel and support system typically adds at least 14.6 to 19.5 kg per 1 m2 (3 to 4 pounds per square foot) to the existing roof. It is the roofing professional’s responsibility to ensure this additional weight does not exceed the load limits determined by the building’s designer.
From an economic point of view, it makes sense the existing roof membrane’s service life will come close to matching the PV array’s projected service life. If not, a complex and costly reroofing project may be required long before the solar panels need to be replaced. The underlying roofing system must provide the same minimum investment horizon—generally at least 20 years—to realize the full potential of the rooftop PV.
Most PV arrays require penetrating the roof membrane. Even non-rack-type systems may include electrical conduits, wiring, and other components that need to be flashed in a professional manner. It is essential the responsibility for this flashing work rests with the roofing contractor and not the solar installer. One can assume the professional roofer will create a durable detail. The roofing contractor may also follow the instructions of the designer or roofing system manufacturer, should a custom detail be required.
It is also important to ensure the positive drainage designed into an existing roof system is not compromised. The use of a tapered insulation system or relocation/addition of new roof drains are two solutions, but these are often cost-prohibitive options for the property owner. Additionally, an existing drain partially covered by a solar array will make it difficult to clean out.
Roof system wind and fire code approvals have always been active topics within SPRI, and the increasing popularity of PV and vegetative roofs adds another layer of complexity when attempting to meet codes and standards. In 2010, American National Standards Institute (ANSI) approved the first of three standards for vegetative roofs: ANSI/SPRI VF-1, External Fire Design Standard for Vegetative Roofs. In the United States, this standard is included in the 2015 edition of the International Building Code (IBC). The National Building Code of Canada (NBC) and provincial building codes also reference several standards from developers, and these standards are then given force of law in jurisdictions where the code is adopted.
A second SPRI vegetative roof standard was approved by ANSI in 2010. ANSI/SPRI RP-14-2010, Wind Design Standard for Vegetative Roofing Systems, provides design guidelines associated with wind uplift and stone ballast scour. It is slated for inclusion in the 2018 IBC and may be of value to Canadian specifiers when working with green roofs.
Like it has done with vegetative systems, the roofing industry in North America now needs to investigate and standardize wind and fire code designs for PV roof systems. In the meantime, roofing professionals must use care when installing a PV array over an existing roof system that carries fire and/or wind classifications. In new construction applications, code-compliance procedures are the designer of record’s responsibility. When installing a PV array on an existing roof, specifiers should consult the roof system manufacturer to ensure existing codes are met.
Roof system manufacturer guarantees on existing roofs are an important consideration for the building owner and specifier. On older roofing systems there may be various roofing manufacturers represented. Even with the popularity of today’s single-source system guarantees, these documents must be evaluated in detail with the appropriate approvals given by the issuer of the guarantee.
Roof system durability
Roof durability directly affects sustainability; it has become a major factor in the choice of the entire roof assembly. At the same time, the potential benefits of the rooftop PV system itself offer long-term energy independence and environmental sustainability. The unique challenges of matching PV systems to compatible roofing systems are so important the building owner needs assurance the combined rooftop PV system is designed, installed, and maintained for optimal economic and environmental benefit.
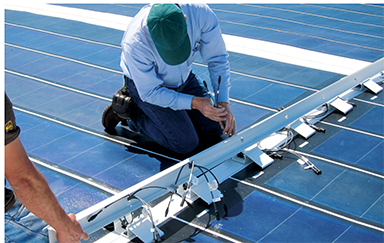
Some commercial PV roofing installations in Canada and in the United States are financed using long-term power purchase agreements (PPAs) or other contracts. These financial arrangements are typically made between a third-party that owns, operates, and maintains the PV system and a host who agrees to place the system on his or her property and purchase the electric output for a predetermined period. For this reason, the continuous, undisrupted generation of solar power is critical to the fulfillment of the PPA terms. As a consequence, the margin of safety required in the roof’s design, installation, and maintenance may likely exceed normal expectations and minimum standards for commercial roofing systems.
Raised-panel and membrane-integrated PV systems often cover most of the roof surface, and both types of PV systems require regular inspections and maintenance. Fortunately, current PV racks can be changed out fairly easily, which can be a big advantage. Indeed, the frequent need for solar roof inspections and maintenance means the amount of foot traffic on these systems may be far greater than the traffic generated by an occasional piece of HVAC equipment on the roof.
Therefore, the chance of sharp tools dropping onto the roof surface or impact damage from heavy traffic or equipment installation increases. This is why enhancing the puncture-resistance of membranes used with rooftop PV systems can be so important. Solutions may include protective cover boards when practical or other options for existing roofs, such as roof walkway rolls or pads.
When it comes to PV arrays, almost all roof system manufacturers require an approved insulation board with a minimum thickness and compressive strength and/or a protection/separation sheet installed between the photovoltaic components and the membrane. Protection pads should be large enough and properly secured so they do not move during the roof membrane’s expansion and contraction.
Membrane type and thickness
A broad selection of membranes and thicknesses are available for consideration when a PV installation is planned. They include:
- ethylene propylene diene monomer (EPDM), polyvinyl chloride (PVC), thermoplastic polyolefin (TPO), ketone ethylene ester (KEE), and co-polymer alloy (CPA) smooth and fleece-back membranes;
- atactic polypropylene (APP)- and styrene butadiene styrene (SBS)-modified bitumen (mod-bit) membranes; and
- certain types of ‘enhanced’ membranes, such as those engineered with special formulations to accommodate the additional heat generated by the PV array or other sources.
In approving the installation of a PV system atop an existing roof while maintaining the warranty, membrane manufacturers may have specific requirements that must be met, such as:
- limitations on the current age of the existing roof system;
- restrictions on the method of roof system attachment to the structural deck;
- restrictions for a minimum approved roof membrane thickness;
- pre-solar and post-solar system installation roof inspections; and
- requirement the building owner make any needed repairs at his or her expense.
It is generally best to contact the roofing manufacturer for help in deciding on the membrane, thickness, and/or existing roof requirements when considering rooftop PV systems.
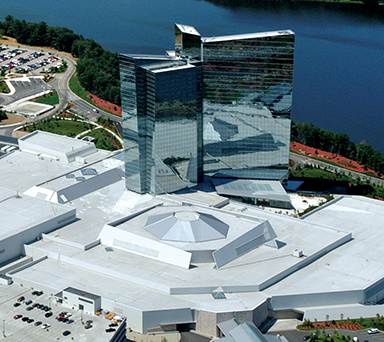
Paperwork
Roofing manufacturers frequently require project documentation forms be completed before installing a PV system over an existing warranted roof to maintain warranty coverage. For example:
- standard pre-installation notice with roof drawings;
- a PV post-warranty alteration form;
- completed inspection reports (before and after PV installation);
- overburden (o/b) waiver form completed by the building owner, wherein the owner describes the PV materials to be installed;
- agreements to pay for the overburden removal when leak repairs are necessary; and
- agreements to pay for repairs caused by the overburden removal and replacement.
There are various other general terms, conditions, and suggestions that should be considered when installing PV systems on existing roofs, according to SPRI. For example, racks should have enough clearance above the membrane to allow for roof servicing. Additionally, PV arrays should be set so all field seams and penetrations are accessible for repair. Further, any staging areas for PV installation should be identified and protected.
There is no question partnering with a roof system manufacturer offering PV-ready roofing systems can be a benefit to the specifier. Many roofing system manufacturers offer certain services to building owners in addition to the sale of roofing system products. These range from financial analyses to show return-on-investment (ROI) periods for a planned solar installation to specifications and layout to single-source warranties for the roof system and solar integration.
Minimizing rooftop support problems
There are four general factors that roofing professionals need to consider when choosing rooftop supports:
- material compatibility;
- load distribution;
- thermal movement; and
- weathering/durability.
Over the years, the roofing industry has developed various solutions to safely support rooftop pipelines, HVAC equipment, antennas, and other paraphernalia often facing designers, particularly in reroofing applications. However, the advent of PV has significantly increased the complexity of choosing rooftop supports. In fact, one of SPRI’s members is not a traditional roofing company, but rather one specializing in electrical grounding, bonding, and connectivity products for alternative energy.
Material compatibility
SPRI Industry Information Bulletin 1-14 emphasizes the extra care that needs to be taken by roofing professionals when specifying and installing rooftop supports for PV solar panels, piping, and equipment. This document includes factors to consider when choosing rooftop supports and also addresses material compatibility. To help in this area, the bulletin includes an extensive chart on dissimilar metal compatibility and potential galvanic reactions between different metals (Figure 1).
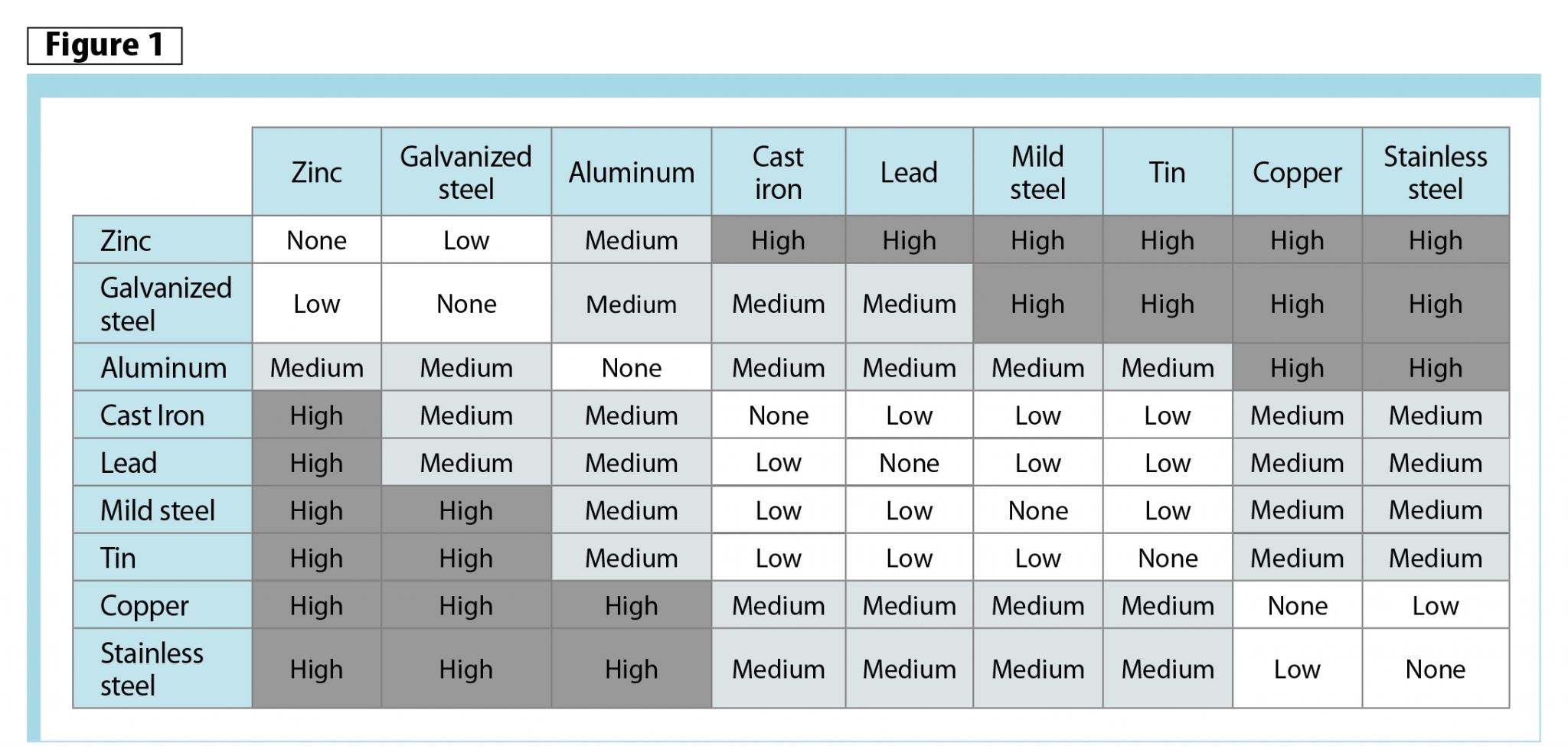
Galvanic corrosion occurs when two different metals are in contact in a corrosive environment, and one of the metals experiences an accelerated corrosion rate. The contacting metals form a bimetallic couple because of their different affinities (or attraction) for electrons. These different affinities create an electrical potential between the two metals, allowing current to flow.
Additionally, when two different metals are in contact in a corrosive environment, one of the metals experiences accelerated galvanic corrosion, while the other metal remains galvanically protected. In Figure 1, metals near each other in the galvanic series have little effect on each other—the ‘None’ or ‘Low’ indicated in the chart. Generally, as the separation between types of metal in the series increases, the corroding effect on the metal higher in the series increases as well—the ‘Medium’ and ‘High.’ Generally, environmental conditions remain large determinants of corrosion rates.
Due to the increase in rooftop PV installations, contractors need to widen their knowledge of potential material compatibility issues. This is why it is a good idea to check with the membrane manufacturer when that material will come into contact with something potentially dissimilar. As always, rooftop supports should consist of similar metal components; or, the metal components should be galvanically compatible metal pairs.
Load distribution
The load distribution and compressive strength of the roof system should always be taken into account before design and installation. Rooftop loads should not exceed the roof and component manufacturers’ recommendations. For support spacing, one should always follow the component manufacturer’s guidelines.
Reduced spacing of support components may also be required. When supporting pipe or conduit spacing is limited, SPRI recommends referring to Manufacturers Standardization Society of the Valve and Fittings Industry (MSS) SP-58, Pipe Hangers and Supports−Materials, Design, Manufacture, Selection, Application, and Installation, Canadian Electrical (CE) Code (or CSA C22), or other applicable codes and standards.
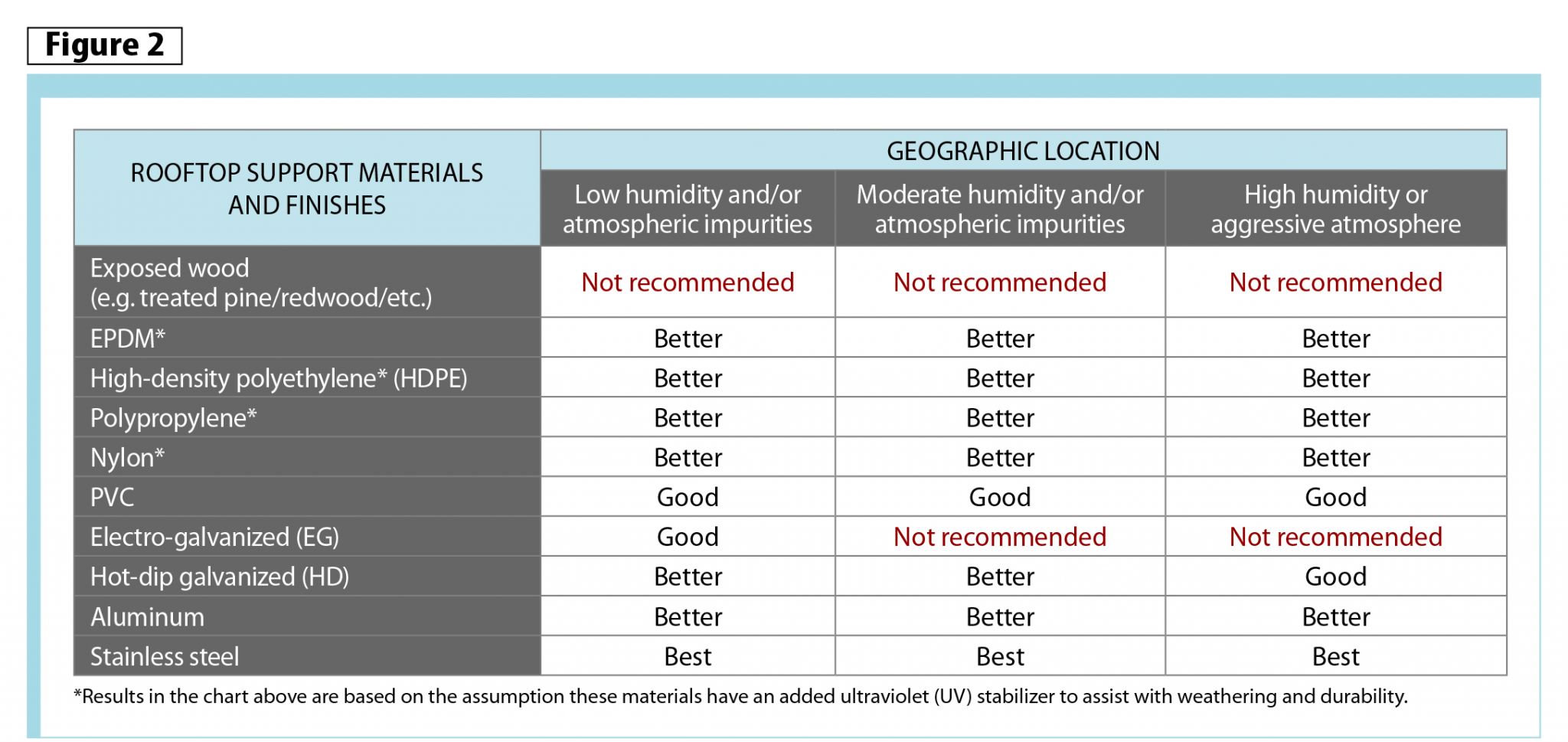
Weathering/durability
The chart in Figure 2 lists the effects of humidity on 10 common rooftop support materials and finishes. Approximately 85 per cent of all steel produced is carbon steel, and therefore susceptible to natural oxidation and galvanic corrosion. The most common exposure environment for metallic corrosion is atmospheric. As steel, copper, magnesium, and aluminum are exposed to the atmosphere, they react with free-flowing air and moisture to develop oxides.
The performance of atmospherically exposed metals depends on five main factors:
- temperature;
- humidity;
- rainfall;
- sulfur dioxide (pollution) concentration in the air; and
- air salinity.
While none of these factors can be singled out as the main contributor to corrosion, extensive studies have been conducted on metals and a predictable corrosion rate for each is available.
For example, corrosion of carbon steel occurs when the relative humidity of the air is 70 to 80 per cent and the air temperature is above 0 C (32 F). Of course, protective layers (zinc) and use of different metals are affected under different conditions. Corrosion rates may be accelerated by air impurities that dissolve in condensed water or rainwater and by dust and dirt settling on the metal surface.
For SPRI’s purposes, researchers tried to provide a simplified view based on available data and field experience, as shown in Figure 2. The weathering capabilities and overall durability of rooftop supports must be considered, using the geographic location of the project as a guide.
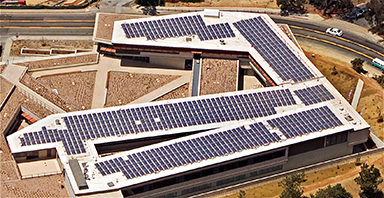
An example of a worst-case scenario would involve roof installations close to the ocean, exposed to saltwater. This location, coupled with atmospheric conditions, may necessitate stainless steel components be used to mitigate rapid development of corrosion on the rooftop support.
In most applications across Canada, zinc is used as a protective layer against corrosion. Electro-galvanized plating is common, but hot-dipped galvanized is often preferred because the additional layer of zinc affords better corrosion resistance. This may also provide a better value proposition than stainless steel supports. Aluminum is also a good option for longevity in many applications. It is commonly accepted wood supports decay more rapidly than engineered supports, and are therefore not recommended for long-term durability.
Thermal movement
Unanticipated thermal movement is another rooftop support issue that could cause damage to the roof membrane. Pipes will expand and contract longitudinally due to environmental temperature fluctuations. The amount of movement depends on what the pipe is made of, the change in temperature, and how quickly that change occurs.
One way to address this is to place the pipe atop an engineered support that has rollers instead of a fixed immovable surface. Rollers on the PV stands are one way to solve this problem, but a ‘slip sheet’ under the PV equipment will not accommodate thermal movement under load.
Conclusion
It is important to remember the rooftop support system must provide the same minimum investment horizon as the roof membrane—in other words, about 20 years—to realize the full potential of the photovoltaics atop it.
Mike Ennis, RRC, joined Single-ply Roofing Industry (SPRI) trade association in 1993. He has chaired various SPRI committees and task forces, and served as president from 2004 to 2006. He became the group’s technical director the following year. Ennis can be reached at info@spri.org.