Finding formwork solutions for groundbreaking projects
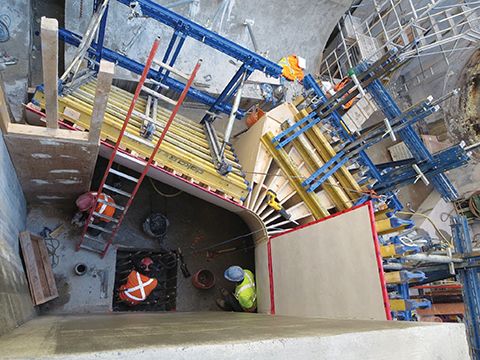
Flexible solutions for Ontario’s first cable-stay bridge
When finished in 2017, the Nipigon River Bridge will be the Ontario’s first cable-stay bridge. The $106-million, four-lane cable-stay bridge is part of the Highway 11/17 corridor east of Thunder Bay—a key part of the TransCanada highway. The final design will consist of three towers with cables supporting the bridge deck and a separate sidewalk for pedestrians.
For the first step, the contractor—BOT Ferrovial Nipigon Joint Venture—had to pour the critical substructure components including the piers, footings, and abutments. In this design, the entire cantilevered superstructure will be constructed without the use of in-water structures.
Single-sided walls were provided using a complete system, which consists of lightweight panels that are easy to handle, so they can be erected very quickly by hand, rather than relying on a crane. A framed formwork system was used to form the concrete foundations. Pre-assembled large area formwork system panels were supplied for the north and centre tower walls, which can be erected onsite as needed. The advantage of this formwork is the shape, size, tie-hole pattern, and form-facing of the elements can be adapted to suit any requirement. Shaft formwork with a shaft platform was used to form the hollow interior of the towers.
The biggest challenge for this project was the complicated geometry of the cross beam. The formwork engineers designed pre-assembled large area formwork panels for the interior and exterior walls of the cross beam. That was followed by a high capacity, fast shoring system, with a height of approximately 18 m (60 ft), which was used to shore the cross beam. The shoring frames are designed for large shoring-heights and high loads. The design provided the contractor with a flat working deck
2 m (6 ft) below the sloping cross beam formwork.
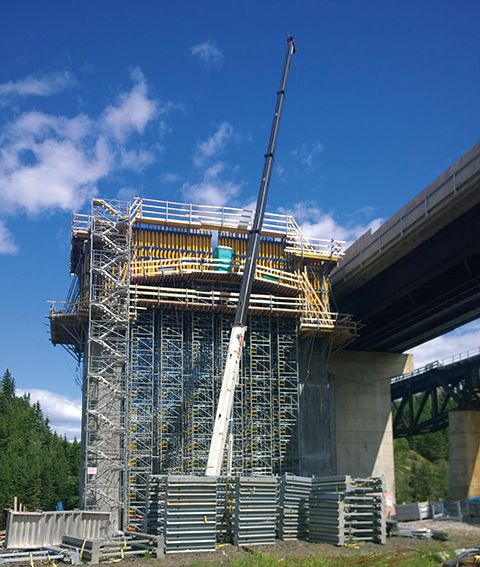
Forming a relationship
To consider formwork in the overall design of an innovative project, it is important for the structural engineer to have a good handle on the standard products available in the marketplace. This can be accomplished by contacting the major formwork suppliers, which should be more than eager to provide assistance to educate the industry on forming products and how the structure’s design affects custom products needed and overall costs.
Formwork suppliers need to be contacted during the project’s very early design stages. This can allow for as much information as possible to be incorporated into the bid documents, which provides a more accurate cost to the owner. Formwork suppliers can advise on sizing structural concrete members to meet standard form dimensions or can suggest when custom designs or parts are necessary. As major form suppliers are typically involved in a large number of projects in a wide variety of construction markets, they can draw on their resources to suggest formwork means and methods.
It is also important to ask concrete forming contractors to be involved early in the design stage of the structure. After all, they are ultimately the people who will be physically constructing it and can provide a tremendous amount of knowledge as to the most practical and economical means and methods.
There are many considerations to take into account at the design phase—and considering formwork is of prime importance—especially when an unusual design may involve custom designed parts. With the ability to pinpoint formwork designs to accommodate the needs of the project, planning ahead ensures the success of an economical concrete construction project.
Michael Schaeffer is vice-president at Doka North America, and has been in the design/construction industry for more than 20 years. His career in formwork has also included front line sales, operations, and branch management, but Schaeffer’s current responsibilities include national sales management, training, and product development. He can be reached at michael.schaeffer@doka.com.