Finding formwork solutions for groundbreaking projects
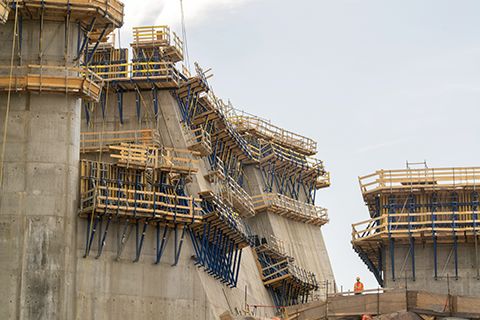
Hydroelectric plant case study
As more unusual designs and projects appear, new formwork challenges are faced. At Muskrat Falls (also shown on the cover), a complete formwork solution package was needed to accommodate the build of the second-largest hydroelectric facility in Canada. The project is located on the lower Churchill River, about 25 km (15 ½ mi) west of Happy Valley-Goose Bay, Labrador. It consists of a powerhouse with four turbines, three dam structures, six spillway piers, separation and retaining walls, and a north and south service bay.
For a huge project such as this, with its many cast-in-place concrete requirements, the formwork manufacturer needed to train and supervise onsite for the use of its systems. Additionally, high standards were built into the design of the formwork solutions, with a zero-tolerance for any lack of site safety. To aid in the project flow and save on jobsite space, the formwork was pre-assembled before being brought to the site. This included pre-assembly of large area formwork, dam platforms, and custom curved formwork.
In one area of Muskrat Falls—the six spillway piers—the structure has true vertical concrete surfaces. Every spillway consists of a bullnose on the upstream side with a large concrete block overhang on the downstream side. Every spillway also includes eight block-outs required for the installation of mechanical gates. This design needed a solution for the symmetrical bullnose to reduce risk of deflection and movement during pouring. The formwork element also needed to be re-used 14 times without any problems. The use of custom radial steel channels instead of wooden gussets was the solution to form the shape of the bullnose.
Another challenge on this job was the separation wall between the spillway and powerhouse structure. The large wall was realized in seven 1.5-m (5-ft) tall monolith pours. It was difficult to perform the monolith pours against the existing structure of the Centre Transition Dam. Custom large-area formwork panels were used to allow and fit the transition between the separation wall and the Centre Transition Dam.
The innovations on the Muskrat Fall project included design and fabrication of a custom off-set bracket to install and support large area formwork off a short starter pour when dam formwork could not yet be installed. An additional innovation was the design and fabrication of a tie-loop anchor to tie down formwork diagonally to vertical rebar, to avoid long ties going through the entire structure to the opposite formwork element.
Tie-less formwork solutions were requested to increase productivity onsite for all the mass concrete pours, reduce the amount of metal embedments and list items in the concrete, and ultimately reduce labour and produce cost savings.
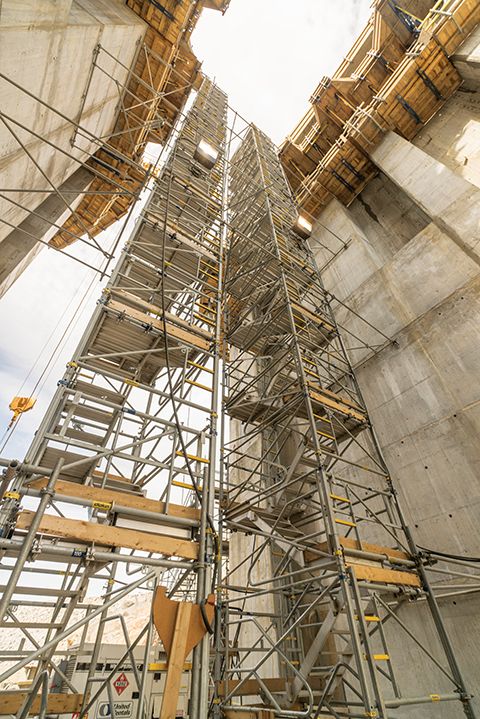
Formwork for bigger sewers
In the eastern end of the Greater Toronto Area (GTA) the cities of Markham and Pickering are experiencing rapid growth. A trunk sewer was required to accommodate the additional sanitary sewer flows projected from the continued future growth.
The goal of this sewer project was to carry 100 per cent of the projected 2036 design sanitary sewers flows. The new Southeast Collector (SeC) trunk sewer is approximately 14 km (8 ½ mi) in length. The sewer was to be constructed at depths of 5 m (16 ft) to more than 40 m (130 ft) below the ground surface.
A major challenge of this project was to ensure the pipeline stayed within the Newmarket Till soil stratum, which is more conducive material for tunnel construction. To do so, a substantial drop in elevation of the pipeline over its length was needed. The use of an earth pressure balance machine as a tunnel-boring machine allowed for different modes of operation to accommodate the changing soils conditions.
Strabag, the contractor, had extremely tight project deadlines and needed high-quality custom built formwork panels ready-to-use onsite. Custom benching (i.e. half-round channel) formwork was supplied for 13 ventilation shafts in total, ranging in depth between 10 and 60 m (30 and 200 ft). The custom formwork panels allowed Strabag to pour the U-shaped benching at the bottom of each ventilation shaft connecting the newly drilled tunnel openings with each other.
These custom formwork panels were based on large area formwork, including wooden gussets and custom splices. Each custom formwork element was highly complex and different in shape and size. Every single formwork element was hand-built.
To meet the city’s requirement for the final concrete finish, the formliners were epoxy-coated during the assembly process and then shipped to the site ready to use. This was an alternative to the use of a controlled-permeability, polypropylene-based formliner. The achieved concrete finish was of a comparable high standard, and was therefore accepted by the client.