Filling the voids: Differentiating between concrete coating and polishing
Densifiers
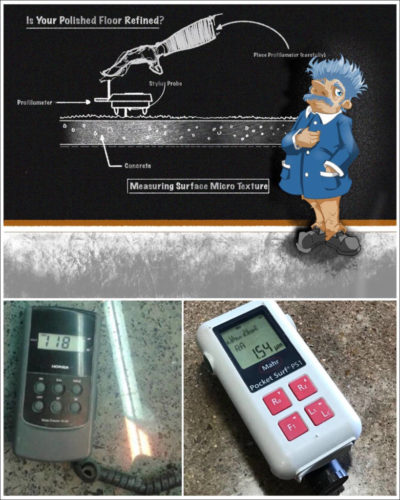
Using a densifier does not necessarily mean the floor will be polished. It is all about application. A concrete densifying agent can be employed in either coated floor systems or concrete polishing. They can be applied like a shell coating to the top of a slab or processed into a floor to aid in refining and strengthening the material inside the slab. Densifiers typically do not enhance substrate colour but can produce some sheen as a coating or with polishing. Densifier performance is based on several factors, including pH, percentages of solids, molecule size, and application process.
There are two basic types of densifiers—silicate- and silica-based. Examples of silicates are sodium, potassium, lithium silicates, or magnesium fluorosilicates. Some of the older silicate technologies have existed since its introduction as coatings for mass-produced automobiles like the Model T, but still have some uses in modern construction as a floor coating. In the presence of moisture, densifiers become chemically reactive with calcium hydroxide (CH) to produce calcium silicate hydrate (C-S-H). Silica densifiers are a newer, more reactive type. Some of these products are referred to as colloidal, which describes the suspended state of silica.
Nano silica densifiers are the smallest category of silica densifiers in which the silica size must be below 100 nanometers, allowing for better capillary penetration. When applied, billions of nano-scaled silica flood the substrate to fill the larger micro-sized pores and channels, creating new C-S-H that bonds not only to existing C-S-H, but also to itself and other silica to reduce porosity and voids on the surface of concrete. Nanoengineering-based technologies are not only small, but also offer advantages with reactive surface areas, genomic code (stacking shape), and other features that industry professionals are beginning to understand, thanks to advances in nanoindentation technologies.
Polished or refined concrete
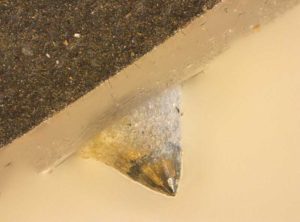
Polished concrete is the act of mechanically processing a floor to achieve a concrete surface with higher durability and physical resistance to chemical and stain attacks within an esthetic framework. Benchmarks for polished concrete are quantified by readings taken from the concrete microsurface texture. Microsurface benchmarks are measured in micrometres (μm) or microinches (μin) with ASME B46.1-2009 (R2002), Surface Texture (Surface Roughness, Waviness, and Lay), available as an easy way to test and measure average roughness (Ra) on a surface. A microinch is equivalent to 25.4 nanometers.
Polished concrete does not rely on application of a resinous coating or topical sealers to achieve performance benchmarks. Full refinement and consistent Ra is easy to achieve with polishing systems. Ra testing can help ensure voids are completely filled by the densifier, and the floor is physically refined. Ra is inconsistent with shiny coatings applications that mimic (or even advertise as) polished concrete finishes because the surface preparation involved with those systems create micro fractures while creating a profile for a topical coating.
Densifiers should not be used to create a distinct coating when polishing, but rather as a part of the physical processing of the new floor surface to aid in greater C-S-H formation, thereby reducing permeability and increasing physical resilience. The processing or folding of the slab back into its own matrix with a densifier is a wet process where final levels of refinement can be performed without creating slurry. Gloss and DOI readings may also be taken from a polished concrete floor and can be helpful in selecting a reflective esthetic, but the latter alone cannot determine if a floor has received a polishing process. It is important to ensure the selected polishing systems can achieve a consistent and repeatable surface micro texture (Ra) as well as high-traction DCOF ratings, such as from ANSI B101.3, Test Method for Measuring Wet DCOF of Common Hard-surface Floor Materials, and to avoid coatings that have a similar appearance.
A refined and polished concrete floor brings many resilient performance benefits, but it can be susceptible to certain chemical attacks. If one wanted an exposed concrete floor finish in a water treatment plant’s fluoride tank room, a coating is likely the best finish. However, for heavy floor traffic areas, long-term durability, and a more permanent solution in void mitigation in commercial and industrial settings, polished concrete is likely the preferred option.