Factors affecting reinforcing steel performance in concrete
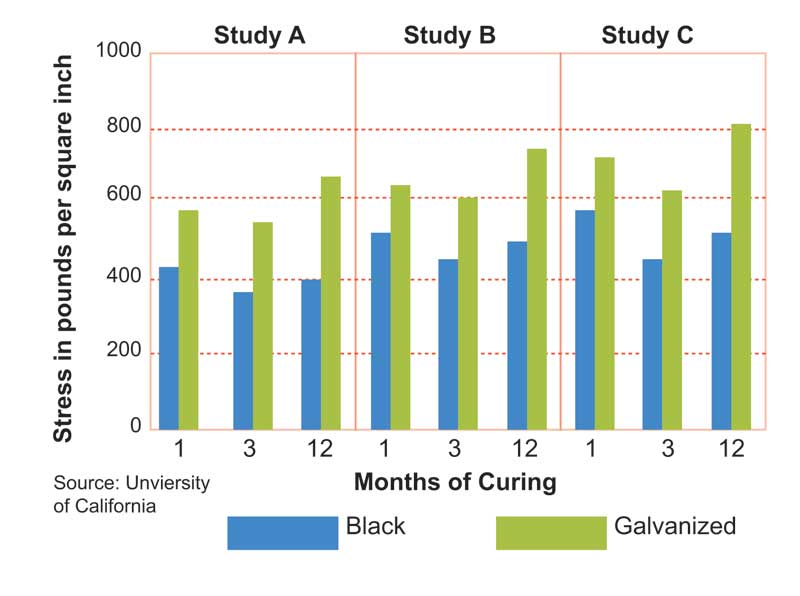
Chloride content
While total chloride content is an important aspect in the performance of reinforcing steel, the chloride content in the concrete mixture itself is only a very small fraction of the overall total. Given concrete is porous, it is susceptible to water, oxygen, chloride ions, and carbon dioxide. (This information is derived from J.P. Broomfield’s “Galvanized Steel Reinforcement in Concrete: A Consultant’s Perspective,” published in the Yeomans text mentioned in note 3.) When these elements seep into the concrete, they attack the reinforcing steel below, causing corrosion and eventually leading to failure.
Once chlorides from de-icing salts or marine environments begin to attack the steel, the corrosion threshold for chloride metal attack factors into the rebar’s performance. The corrosion protection afforded by galvanized rebar in concrete is due to a combination of beneficial effects, including the sacrificial zinc coating. Of primary importance is the substantially higher chloride threshold for zinc coatings to start corroding (two to four times that of uncoated steel). (See the International Zinc Association’s “Performance of Galvanized Rebar in Concrete” at www.galvanizedrebar.com.)
Bond strength
Bond strength between the rebar and the concrete significantly affects the performance of reinforcing steel. The structure’s overall strength highly depends on this bond strength, so it is important to use a bar or coating that does not reduce it. Affected by the bar’s physical structure, depth of concrete cover, and any potential coatings on the steel, bond strength can be improved with bars that are ribbed or deformed, as this provides more bearing surface in contact with the concrete. Coatings on bars produce varying bond strength results, with galvanized bars typically performing better than epoxy or uncoated bars. (For more, consult O. Kayali’s “Bond of Steel in Concrete and the Effect of Galvanizing,” published in Yeomans’ text.) This can be partially attributed to the chemical bond formed between the zinc layer on the galvanized steel bar and the concrete.
Concrete cure time and environmental factors also affect bond strength; in some cases, the bond between the type of bar and the cement may take varying amounts of time to form. Three studies compared the bond strength of hot-dip galvanized rebar compared to black rebar: “Zinc-coated Reinforcement for Concrete,” “The Influence of Steel Galvanization on Rebar’s Behavior in Concrete,” and “Bond of Ribbed Galvanized Reinforcing Steel in Concrete.” (All three of these studies were referenced in O. Kayali and S.R. Yeomans’ “Bond of Ribbed Galvanized Reinforcing Steel in Concrete,” published in the Journal of Cement and Concrete Composites in 2000.) In each of these studies, hot-dip galvanized rebar had higher bond strength to concrete compared to black rebar. Figure 1 shows the various bond strengths observed for hot-dip galvanized rebar and black rebar in different studies.
Further, studies from the American Society of Civil Engineers (ASCE), the International Journal of Cement Composites and Lightweight Concrete, and the Proceedings of the Institution of Civil Engineers–Structures and Buildings found epoxy-coated rebar had a reduction of 20 to 50 per cent in bond strength to concrete when compared to black rebar. (These studies are R.G. Mathev and J.R. Clifton’s 1976 “Bond of Coated Bars in Concrete,” K. Kobayashi and K. Takewaka’s 1984 “Experimental Studies on Epoxy-coated Reinforcing Steel for Concrete Protection,” published in International Journal of Cement Composites and Lightweight Concrete, and J. Cairns’ 1996 “Performance of Epoxy-coated Reinforcement at the Serviceability Limit State.”)
Type of rebar
Environmental factors ultimately decide the overall performance of a project. As concrete is porous, the steel within is still subject to anything permeating it, despite the fact the steel is not directly exposed to the atmosphere. In areas where road salts are used during harsh, icy winters, the reinforcing steel is subject to opportunities for corrosion due to the chlorides from the road salts. Additionally, in tropical marine areas such as Bermuda, reinforcing bars are highly susceptible to chlorides, which—as mentioned—can be detrimental to their performance.
Considering these factors, it is important to protect steel embedded in concrete from corrosion. With the increasing importance of sustainable design partnered with economic efficiency, specifying projects with 100-year lifespans is essential. Studies have shown while epoxy-coated reinforcing steel may be an economical choice, it does not last as long as other options due to many factors. Stainless steel comes at a high initial cost, yet can withstand corrosion for 100 years according to accelerated testing by the Michigan Department of Transportation. (Visit www.michigan.gov/documents/mdot/MDOT_Research_Report_RC-1560_407022_7.pdf.) In addition, epoxy-coated rebar requires special handling at the jobsite to ensure the coating is not damaged. Other bar types, including galvanized, stainless, and uncoated, do not require special handling and are resistant to abrasion incurred at the jobsite.
Epoxy-coated rebar comes at a low cost and performs well in roads and structures not subject to extreme weather and de-icing salts, or those located in dry, non-marine environments. While epoxy is the most widely used form of corrosion protection for reinforcing steel, it has a shorter lifespan than its alternatives.
Galvanized reinforcing steel is an extremely durable option with a middle price range, and has great performance records in a variety of concrete projects. In both galvanized and stainless steel reinforcement options, the upfront price ends up being the price of the life of the project. When working on public projects, selecting the more economical option is usually easier to justify.