Exploring the balancing act of glass in construction
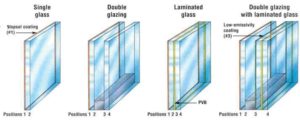
A building’s window-to-wall ratio is determined by dividing the total glazed area of a building by its exterior envelope wall area. This number is significant as it affects the energy performance of a building. While more windows or glass on a structure mean more daylight, choosing this material may also place extra loads on an HVAC system as it has to work harder to maintain an even temperature in cold or warm weather.
To ensure a building performs as needed, an architect or design team may source and specify glass with a coating that is intended to keep a building cooler or warmer, depending on the climate. When specifying glass and coatings, the architect will take into account a window’s U-factor (i.e. U-value), the measure of heat gain or loss because of a difference in temperature, the solar heat gain coefficient (SHGC), how much of the sun’s energy hitting the window is transferred as heat, and the visible transmittance of glass measuring the amount of light coming through the glass.
Yet, selecting a top-performing low-e coating does not mean that an architect should eliminate a certain design vision to obtain the right performance. In fact, Canada’s focus on sustainable design and push for the Zero Carbon Energy Standard has motivated architects to source products combining esthetics with the required performance.
“The notion of esthetics being more important than performance is not true,” says Caliman. “We are constantly adapting and looking for new ways to balance the two, and some kind of compromise is always necessary. You need to marry the esthetics with performance to achieve a high-performing building envelope.”
Enhancing the performance of IGUs
To achieve performance goals, low-e coatings can be placed on specific glass surfaces in an IGU. An IGU is comprised of two or more panes of flat glass (glass lites) separated by a spacer material and sealed at the edges (also known as a full-perimeter seal). Commonly, the end result is also known as double- or triple-glazing. The glass in these lites can be clear, low-e, reflective, tinted, or decorative, depending on the performance requirements, and can also be heat-strengthened, tempered, or laminated. The space between the lites is filled with dehydrated air and/or a noble gas (generally argon or krypton). The addition of this gas can help enhance the unit’s insulating properties. IGUs can be designed to enhance solar and acoustical control, ultraviolet (UV) light screening, and security among other purposes.
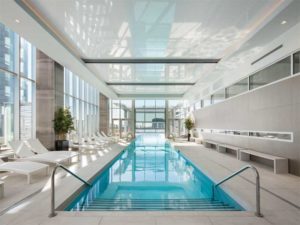
In a double-glazed IGU, there are four surfaces being treated with a low-e coating to enhance the window’s performance or to help regulate temperature and solar transmission (Figure 1). Different coatings are selected depending on the desired function.
To protect the integrity of the coating, ‘soft coat’ low-e products, or those applied off the float line to precut glass in vacuum chambers via magnetron sputter vacuum deposition (MSVD), must be installed in the second or third position in a double-glazed unit and in the fourth or fifth position in a triple-glazed unit. The low-e coating on the glass in the second or third interior positions, facing into the cavity, reduces the amount of radiated heat transfer between the two or three panes, depending on whether it is a double- or triple-glazed unit.
The U-value is not affected by applying the coating on the second or third surfaces. However, placing the low-e coating on only the second surface will reduce solar heat gain and, by extension, cooling costs.
Fourth-surface technology is one way to make glass windows perform more efficiently. Combined with the use of select coatings, this technology can deliver the required performance. It is achieved by adding a low-e coating to the second and fourth surfaces of an IGU.
Additionally, fourth-surface technology enhances the glass performance by achieving a lower U-value. The coating on the second surface will reflect solar energy to the outside when the sun is shining. Essentially, this is a new application of existing technology that can combine glass coatings using different products to achieve higher performance and overall energy efficiency in a building.
During cold conditions, the coating on the fourth surface will reflect energy back into the room. This reduces the amount of energy transferred across the airspace, thereby improving the overall insulating properties of the glass by an additional 15 to 20 per cent versus a conventional low-e unit.
“It is possible to specify select coatings delivering on performance and meeting the esthetics,” explains Jeff de Waal, architectural manager with a glass manufacturer. “When an architect knows how the glass needs to perform, it is important they also can easily learn how it will look on the building. Depending on the manufacturer, it is possible to assist with creating a signature that will perform as needed and look unique to others.”
Some glass manufacturers are able to work closely with design teams to help them achieve their vision, their ‘signature,’ for the building, while ensuring the selected glass enables a building to optimally perform. This has become increasingly important in cities like Toronto or Montréal where there is high demand for housing and new construction.