Exploring John Abbott College’s latest building
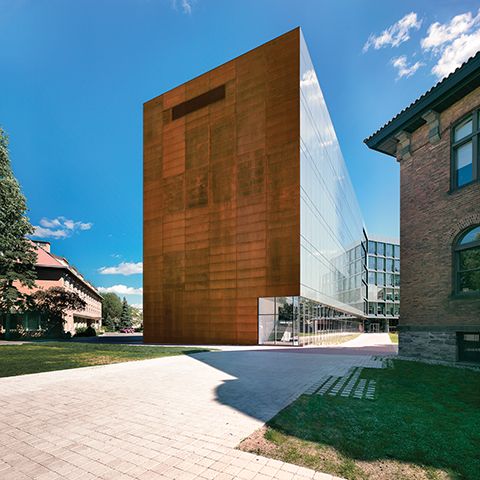
Transferring energy from one place in the building to another without using any outside source of energy (i.e. neither heating nor cooling) is the best way to achieve energy savings. For example, during a winter day, the heat extracted from the interior zone can be used to compensate the loss of the perimeter. Geothermal heat pumps are generally three to four times more efficient than a traditional system in heating mode. This system responds to 50 to 70 per cent of the cooling and heating energy demands of the building. Two air-cooled rooftop chillers (each with 150 tonnes of capacity) and two electric boilers (288 kW each) cover the remaining needs during the peak season.
The envelope of the building is mainly heated with a radiant low temperature system using the concrete slab to distribute the necessary heating. The pipes were located in the lower portion of the slab so they could be used at the same time as a radiant ceiling for the room underneath (i.e. exposed concrete ceiling) and as a radiant floor for the room over the slab. This position in the slab ensures the ceiling radiates more heat than the floor so it does not exceed the maximum allowed temperature for a radiant floor. This system is also used to cool a portion of the load from the envelope. Special care was taken to control the humidity level in the building to ensure no condensation would form on the slab during the cooling mode.
A solar preheating system is used for domestic hot-water needs. This assembly comprises flat-plate collectors located on the roof of the building and is usable all year long, even during the winter when the exterior temperature is below 0 C (32 F).
Connected to the hydronic network and allowing the building and its occupants to ‘breathe’ are the ventilation systems. The strategy behind the ventilation network was to install a primary fresh air unit that supplies the air to secondary fan coil units distributed all around the building. This ensures the right amount of fresh air is distributed everywhere independently from the load and, therefore, reduces wasted energy.
Further, a double-duct secondary system is used to recirculate return air from common zones. Depending on the needs, this air compensates the exhaust in the laboratories (from the chemical fume hoods), recirculates interior zones, or exhausts through a heat recovery device. Combined with the radiant slab, it decouples the fresh air treatment and distribution from the air change requirement and the pressurization in the laboratory and from the temperature control.
All air-handling unit (AHU) fans are equipped with variable speed drives to respond to real-time ventilation requirements, including input from carbon dioxide (CO2) sensors in ducts and in high-density zones such as the classrooms and various learning centres.
The air entering the primary unit is pretreated by two heat recovery devices. The more efficient accumulation type is used on the ‘clean’ exhaust (not from the fume hood) and has a yearly efficiency of 82 per cent for sensible energy and 70 per cent from latent energy (latent energy is recovered and humidity is transferred from the exhaust air to the fresh air in the winter and from the other way around in the summer). The secondary device, a run-around glycol loop, is used on the chemical fume hood exhaust and has a winter efficiency of 40 per cent.
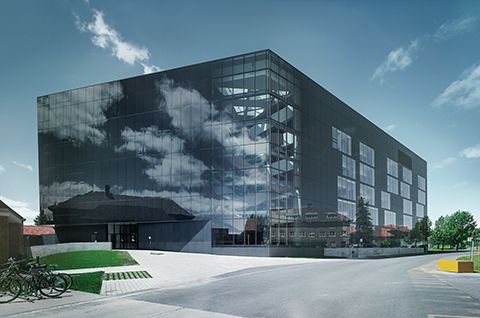
To increase the efficiency in the summer, the water collected on the fresh air cooling coil is evaporated in the exhaust. This device, though less efficient, is safer and has no risk of recirculating contaminated air from the exhaust into the fresh air.
A dedicated ventilation unit fed with fresh air from the primary unit is also installed for the biopharma area.
To reduce the use of electrical energy during the shoulder season, natural ventilation is used for all the common areas. When the exterior temperature is adequate, automatically operated windows are opened at both ends of the building in the hallway of every floor and at the upper portion of the sixth-floor atrium to create a stack effect throughout the building. During that mode, the ventilation units from these zones are stopped.
In terms of water, the building limits its potable water needs by recovering rainwater and by using efficient devices. Potable water consumption is reduced by 60 per cent. The recuperated water is kept in a large underground tank and is employed for the toilets throughout the building.
During the design, special care was taken to ensure easy maintenance for the various components. For example, all the decentralized fan coils are located directly on the floor in small closets in the hallways. The mechanical elements in the laboratories are exposed in the ceiling, and sufficient space has been allowed around the mechanical systems in the mechanical rooms.