Exploring EIFS’ long-term sustainability
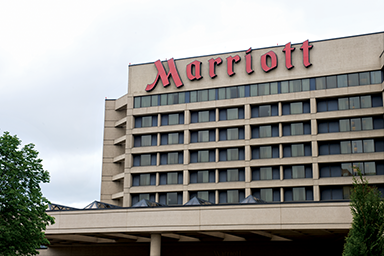
By Kevin Day and Daniel Schlegel
In the early 1990s, there were mixed opinions about what could, and what should not, be done with exterior insulation and finishing systems (EIFS) as an exterior cladding. However, at that time over 20 years ago, the EIFS industry began the conversion from barrier wall assemblies to rainscreens. Concerns about face-sealed claddings, due to incidental moisture intrusion, led to EIFS manufacturers incorporating a drainage plane in their assemblies for incidental moisture.
Today, the situation is much clearer. As sustainable design and green construction continue to grow in mainstream prominence, a particular advantage of EIFS is being cited—its lower impacts over the building lifecycle cost, mainly because it has a smaller ecological footprint compared to other traditional claddings.
A brief history of EIFS
EIFS is a composite wall cladding system that typically comprises:
- insulation board made of expanded polystyrene or other similar materials;
- adhesive and/or mechanical fastener to attach the insulation board to a substrate (and/or mechanical fasteners for special substrate conditions);
- reinforcing mesh for impact and fire resistance;
- base coat to embed the reinforcing mesh and provide weather resistance; and
- decorative and durable finish coat.
Drainage systems also include a liquid-applied air and water-resistive barrier (WRB), which can be designed as a vapour control layer and adhesive applied with vertical notched trowel to facilitate drainage of incidental moisture at window heads and through-wall-flashings. In some cases, geometrically shaped expanded polystyrene (EPS) is used to create drainage pathways on the conceal face of the insulation.
During the oil crisis of the mid-1970s, EIFS became popular with many builders, because their clients saw a significant increase in their energy bills. In 1980, EIFS received widespread consideration as a mainstream cladding, heralded for its inherent energy efficiency, and scalable economy. Within a few years, numerous high-profile projects had been completed across Canada—most notably the overcladding of Banff, Alberta’s Chateau Lake Louise in 1979 when the hotel was converted from summer-only to full-year usage. By 1990, EIFS was popular for retail and other commercial buildings as they could define corporate brand using the cladding system because of its design and colour flexibility, low maintenance, and increased energy-efficiency as it wraps the exterior in a thermal blanket of insulation.
By insulating outside the structure, EIFS reduces air leakage and stabilizes the interior environment, thus reducing the energy consumption. By contrast, traditional insulation in framed wall cavities (regardless of thickness) is diminished by thermal bridging—where heat and cold pass more freely between the outdoors and the space within.
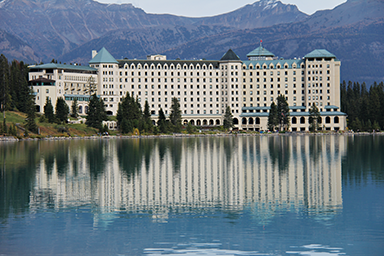
As mentioned, rainscreen options for EIFS came onto the market about two decades ago, with drainage mandated in many municipalities by the turn of the century. In 1996, the city of Vancouver mandated EIFS be installed as a rainscreen, and this became commonplace through the British Columbia lower mainland. The Ontario Association of Architects (OAA) soon decided to exclude face-sealed wall assemblies over moisture-sensitive substrates from its indemnity coverage in 2002. It is generally acknowledged EIFS installed since that time have incorporated rainscreen principles, and these systems are generally performing satisfactorily.
In 2010, Underwriters Laboratories of Canada (ULC) released CAN/ULC-S716, Standard for Exterior Insulation and Finish Systems (EIFS)–Materials and Systems. In 2014, a significant milestone for the EIFS industry was achieved as all three parts of the EIFS CAN/ULC S716 family of standards are expected to be adopted and referenced in the updated National Building Code of Canada’s (NBC’s) release this month. At the same time, Ontario will adopt this change and all other provinces are expected to follow suit.
This code change impacts projects under the scope of both Parts 5 and 9 with CAN/ULC S716.1, Materials, adopted as the underpinning standard that will govern use and application and be referenced in both parts of the code. CAN/ULC S716.2, Installation, and CAN/ULC S716.3, Design, are referenced in Part 9 of the code and become a prescriptive requirement for all projects falling under its scope. CAN/ULC S716.2 and CAN/ULC S716.3 will also be referenced in the Appendices section of Part 5 of the NBC.
Defining sustainability for claddings
While EIFS standards have evolved, so too have expectations for a building’s energy performance. Fully glazed buildings, with their propensity for poor (overall) insulation values, are not really sustainable from a lifecycle-analysis point of view.
Defining a framework to compare EIFS to glass and other cladding types requires a comparison of the respective ecological footprints. The simple method to evaluate this footprint of a product, technology, or building system involves a critical examination, quantified by resource expenditures such as embodied energy, carbon, and water. Aspects include:
- extraction of resources;
- processing, packaging, and storage;
- transportation (along the entire supply chain, from cradle to grave);
- erection/installation and service life; and
- recycling, reuse, and/or landfill waste.
In this framework, EIFS can be compared to many other traditional claddings—such as brick, stucco, aluminum, cedar siding, and vinyl—each of which has its own features and benefits. However, it could be argued no other cladding option has as small an ecological footprint as EIFS when considering embodied energy, associated greenhouse gas (GHG) emissions, and thermal efficiency. In 2007, using its Building for Environmental and Economic Sustainability (BEES) v.4.0 program, the U.S. National Institute for Standards and Technology (NIST) conducted a detailed lifecycle assessment (LCA) of various cladding systems to compare the relative performance on the “ecological scale.” Figure 1 shows some of the relevant findings.
Extraction of resources and manufacturing
Comparing the embodied energy by fuel value, which means the fossil fuel energy necessary to extract and create the raw materials needed to manufacture a product, EIFS was found to be about 75 per cent lower than brick, and 40 per cent over traditional stucco. Cedar plank siding and vinyl also ranked higher due to the increased amount of energy required to collect the resources, process, and then supply to the market. The low embodied energy of EIFS ranks the assembly among the lowest carbon footprints for cladding system alternatives.
Transportation
Transportation showed a similar trend—for example, the expense of transporting brick and stucco materials can be far more intensive than brick and traditional stucco. Other siding products, such as aluminum panel, wood, and vinyl are comparable to EIFS, as they are lightweight materials requiring significantly less truckloads to transport the materials to the jobsite.
Construction and use
EIFS has the advantage of external insulation placement, so it can be considered more efficient than any other cladding. The placement of insulation in stud cavities will be 40 to 60 per cent of the actual insulation value of EIFS, as the latter has no fasteners or structural elements and, therefore, minimal thermal bridging.
Along with American Society of Heating, Refrigerating, and Air-conditioning Engineers (ASHRAE) 90.1, Energy Standard for Buildings Except Low-rise Residential Buildings, the latest National Energy Code of Canada for Buildings (NECB) clearly delineates the intent of having ‘true’ R-value in the wall assembly, so calculations of the net R-value must be determined. Computer models used to predict building energy costs need to validate the R-value/U-values ‘assumed’ for wall assemblies.
Recycle, reuse, and waste
The end of the cradle-to-grave cycle of EIFS results in:
- re-coating the EIFS and replacing sealants (which can extend service life by 10 to 20 years);
- re-laminating the EIFS (which can extend service life by
20 years); and - replacing with new EIFS, after more than 30 years of service—new cladding can be expected to hit 50 years.
At the end of its service life, all EIFS components are physically reusable. The EPS can be separated and ground down to serve as filler in recycled-content insulation or employed for soil stabilization. The lamina (i.e. reinforced base coat and finish) can be ground down and converted into lightweight fill for geotechnical applications or be used for soil stabilization.
Conclusion
The long-term performance of exterior insulation and finish systems is no longer under speculation. The guidelines and track record are well established and the strength of EIFS’ sustainability value proposition is undeniable when the entire global warming potential is analyzed.
The packaging of EIFS products continues to evolve, with research finding ways to make materials even more adaptable to recycling and reuse. At the same time, recycled content is increasingly being used within EIFS components.
Kevin Day is the director of sales and marketing for Dryvit Systems Canada, and a LEED AP. He is the vice-chair (and past-president) of the Exterior Insulation and Finish Systems (EIFS) Council of Canada, and a past-president of the Ontario Building Envelope Council (OBEC), winning its 2014 Anthony A. Woods Award. Day is regarded as a leading expert on EIFS, and is widely recognized for his extensive cladding engineering experience. He is a past contributor to Construction Canada. Day can be reached at kcday@dryvit.ca.
Daniel Schlegel is a marketing and branding expert who has been connecting people and products through technology for almost a decade. He draws on his diverse experience in B2B and B2C marketing, sales, and business development to create a platform for Dryvit to promote its product, share expertise, and interact with clients. Schlegel holds a bachelor’s of commerce degree in business management from Ryerson University, and is currently working toward obtaining his Project Management Professional (PMP) designation. He can be contacted by e-mail at dsschlegel@dryvit.ca.