Expanding laminated glass performance
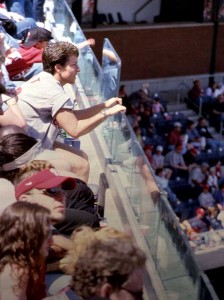
Photo courtesy DuPont Glass
Transparency and security
Many commercial buildings, especially storefronts, are taking advantage of the transparency of ultra-clear glass laminates and the security interlayers bring to the overall glazing product. This type of glass has reduced iron content, making it appear highly transparent, even when laminates are constructed with multiple pieces of thick glass.
Burglar-resistant laminates use a 1.52-mm (0.06-in.) interlayer for impact resistance. Underwriters Laboratories (UL) 972, Burglary-resisting Glazing Material, contains a test method for evaluating laminates. UL 752, Bullet-resisting Equipment, provides rating levels, required ammunition, and other information related to testing bullet-resistant products. Multi-ply glass laminates, or those incorporating polycarbonate, are designed to resist bullet penetration and spall (i.e. release of small glass fragments from the back side of the laminate). A UL certification program is available for both burglary- and bullet-resistant products, and can be a requirement in the contract documents.
Special security applications include zoo enclosures, correctional centres and jails, psychiatric facilities, and data-processing centres. Careful consideration of the threats associated with each project must be undertaken before specifying laminate construction. For instance, new mental health facilities in London and St. Thomas, Ont., operated by St. Joseph’s Healthcare, will incorporate impact-resistant laminated glass to elevate the overall security of the buildings.
Energy performance
The typical laminate interlayer filters up to 99 per cent of ultraviolet (UV) radiation below 380 nanometers. UV exposure is a major cause of fading fabrics and other interior furnishings. Therefore, the laminate interlayer can help reduce fading, while providing other valuable benefits.
Laminated glass interlayers are available in various tints that can help lower solar heat gain and control glare. Tinted and spectrally selective tinted glass, can be used in laminate construction. Low-emissivity (low-e) coatings are often specified to improve energy performance. These are microscopically thin, virtually invisible, metal or metallic oxide layers deposited on the glass. The coating reduces infrared radiation from a warm pane of glass to a cooler one, lowering the window’s U-factor (i.e. heat transfer).
Low-e coatings are designed for high, moderate, or low solar gain. Requirements for U-value and solar heat gain are given in ASHRAE 90.1, Energy Standard for Buildings except Low-rise Residential Buildings, as well as in the applicable building code. These requirements vary by climate zone. Additionally, programs designed to promote sustainability—such as Canada Green Building Council (CaGBC) and U.S. Green Building Council’s (USGBC’s) Leadership in Energy and Environmental Design (LEED) rating system—encourage the use of energy-efficient glass.
In some cases, energy performance is enhanced by materials encapsulated inside the laminate interlayer. One example features an encapsulated solar film between two pieces of interlayer that decreases solar heat gain by up to 34 per cent. The film is neutral in colour with a minimal reduction of visible light.
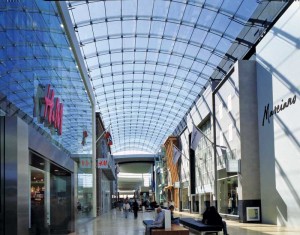
Photo courtesy W&W Glass
Decorative applications
Digital printing on glass, interlayer, or film encapsulated between interlayers is another way of creating colour and imagery with laminated glass. The printing process allows multiple colours on a single panel and the replication of photography and designs through the use of coloured inks. Graphics encapsulated within glass are safe from any surface abrasions.
Laminated glass has always been a vehicle for decoration by encapsulating materials to create a unique appearance. Natural materials, such as leaves and feathers, have been encapsulated, as well as various fibres that provide texture to the laminate. One type of decorative encapsulation incorporates an open-weave fabric, finely woven from black polyester fibres and coated on one side with a thin layer of metal to give a highly reflective metalized appearance.
Gold-blue and copper-bronze encapsulated dichroic films between two interlayers are now being marketed as alternatives to dichroic glass. This non-metallic, corrosion-free technology does not interfere with radio frequencies or wireless communication.
Conclusion
Laminated glass has been used for safety, including overhead glazing, for many years. Its use in glass railings and floors is expanding as applications continue to grow. While interlayers have traditionally bonded glass plies together and created a safety glazing material, stiff, structural interlayers now enable thinner, lighter construction and improved open-edge durability of the laminate.
Laminated glass products offer designers colour, imagery, and encapsulation options. Additionally, new solar choices expand choices in the energy area. More materials are bound to appear as demand increases in the future.
Valerie L. Block, CDT, LEED AP, is the senior marketing specialist for DuPont Glass. She chairs the ASTM task group on Glass Strength and the task group on Glass Floors, and also chairs the laminating division of the Glass Association of North America (GANA). With 30 years of experience in the architectural glass industry, Block is the president of the Glazing Industry Code Committee (GICC) and a member of the Canadian Standards Association (CSA) Technical Committee on Building Guards. She can be reached via e-mail at valerie.l.block@usa.dupont.com.