Execution is key for door hardware installation
Technology has provided improved tools to help the project team with the execution process. Project design documents once consisted of hand-drafted drawings. The first 2-D computer-aided design (CAD) systems automated this process and made it easier to manipulate building sections and share information. Now, 3-D building information modelling (BIM) systems make it possible to go beyond plan views and see designs in three dimensions.
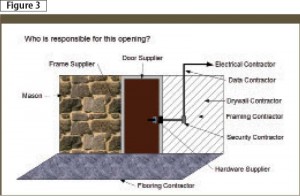
Distributors use software that manages the entire lifecycle of doors, frames, and hardware for construction projects. It is used to:
- efficiently bid projects;
- produce submittals;
- generate purchase orders;
- manage cost; and
- track the overall project.
Forward-thinking distributors have detailing software allowing seamless communication with an architect’s BIM files. Architectural hardware manufacturers are developing libraries of their products that can easily be selected by design teams, which can link into functional systems to evaluate esthetics and performance. While these tools represent a great opportunity, problems can result without the proper execution written in the specification (Figure 4).
Integration, not just installation
Most 08 71 00 specifications include little, if any, language about execution. They do not establish an integration process, set requirements to achieve this end, or assign responsibility. Integration provisions should be included in the specification so the general contractor can account for them. Most standard 08 71 00 specifications assign the integration responsibility to the general contractor in a non-specific way and leave it at that. They seldom include requirements about how integration is to be performed, and by whom. The general contractor must make project co-ordination plans, procedures, and requirements clear to all subcontractors. Hardware distributors/integrators must know what they are expected to do and how they are expected to perform their work.
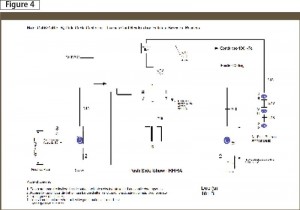
If these were included in the execution section of the 08 71 00 specification, important decisions could be made at a project’s beginning. All the trades would know how the project work will be co-ordinated and performed before they make their proposals, which will be based on the same assumptions so they can be realistically compared with each other.
Throughout a building’s life, the end-user is the main decision-maker in maintaining or upgrading the facility, and with door openings being an interactive part in every structure, they necessitate frequent support, replacement, and upgrade. Who better to provide that support than the distributor who was part of the design team? This proposition would mean the intended use, function, and design integrity could be maintained. Given that doors and hardware are becoming more function-rich and complicated, manufacturer and distribution partnerships add significant value in project management, installation, and co-ordination with the other various elements of the building process.
As higher technology and more intelligence gets embedded and integrated into door-opening products and solutions, the skill sets involved to select, specify, install, and maintain a door opening change a great deal. A few years ago, having knowledge of the complex mechanical part of hardware products sufficed. As more electromechanical components and features became part of products, the ability to handle low-voltage wires became an additional integral necessity in the process.
During the last few years, the convergence of physical and logical security has introduced a new complexity level into handling door-opening products. This emergence of intelligent access control openings and, in general, of highly integrated building management systems, triggered increasing links of the physical controls to a facility’s information technology (IT) infrastructure. Therefore, being proficient in dealing with software, computers, and IT networks is becoming an additional necessity in the process of selecting, specifying, installing, and even using or maintaining door-opening solutions.
A successful, efficient project considers the client’s needs, well-being, and budget. The client, architect, and contractor have very specific and necessary roles. Therefore, it is not surprising many contractors have become design-build firms, and many architects and engineers have become contractors as well.
Moving forward
New and innovative approaches to project execution have shifted the relationship between architect and contractor. No longer is there the typical separation between them with its daily time lags, as one party communicates information to the other. This method of project delivery puts enormous pressure on the firm responsible for the project design and execution.
These two approaches point to a coming evolution in project delivery methods in architecture and construction. Both have developed cyclical processes that go back and forth between reviewing design intent and constructability throughout the process, rather than defining a line when design stops and construction starts. While it seems both are vying for a more close-knit relationship between architect and contractor, it remains to be seen who will take the upper hand and gain control and monetary rewards for their additional involvement.
The project’s most recent specification documents should be reviewed, and Section 08 71 00 should be looked at to find out who is writing the specification, and if are they ensuring the job gets delivered right the first time.
Ken Burkimsher is the special projects manager for Knell’s Door & Hardware in Kitchener, Ont. He has more than 25 years of experience working for both manufacturers and distributors in the door and hardware industry. Burkimsher is an active member of Door and Hardware Institute (DHI) Canada, and has participated on committees with the Ontario chapter. He can be contacted via e-mail at kburkimsher@knells.ca.