Examining the Nuances of Greener Insulation Technologies
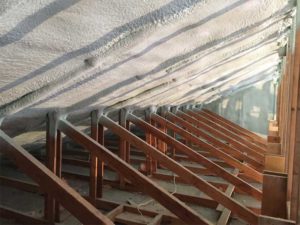
by Maxime Duzyk
The attic is one of the most neglected and overlooked spaces in a home. Many houses have ‘vented’ attics with intake vents under the eaves to allow the cool air to break free, and exhaust vents at the peak of the roof to prevent overheating and condensation by allowing hot air and moisture to escape. A closed-cell polyurethane spray foam (ccSPF) can be applied directly on the attic floor to resist transfer of airflow to the rest of the house. With Canadians wanting more home space in the new pandemic-era, the attic is no longer just a place to store unwanted goods.
Residents are spending more time at home and wanting larger living spaces due to lockdowns and stay-at-home orders. Pandemic home renovations are on the rise. In a recent report, Toronto-based real estate consultancy Altus Group calculated Canadians spent more than $80 billion on home improvements last year, a tally that outpaced growth in the overall economy. An attic renovation can provide a whole new living space that can be used for a gym, extra bedroom, or office. At the same time, a liveable attic can increase a home’s resale value exponentially.
However, it must be taken into consideration with many new and complex designs including houses without overhangs and flat roofs, ventilation is often difficult to accomplish, creating problems (ventilation opening on the roof line) or is just non-esthetic (ventilation opening on the upper portion on the exterior wall). It can also be expensive to create room and openings for ventilation and add to that the cost of the grids and the labour to install them. With thinner structures like rafters instead of trusses, one can save on costs because the added thickness for ventilation is not necessary.
Removing ventilation can also save builders some grief around how to ventilate complex roofing systems with different slopes and connections. Unfortunately, the air often does not follow complex paths and may get trapped, creating more problems than solving them.
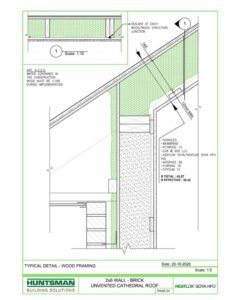
The new norm
With home space being a premium, conditioned, livable attics and unvented cathedral ceilings are in demand. These can create problems for conventional ventilated roof assemblies because the geometry makes it difficult to ensure air- and vapour-tightness at the ceiling plane. Further, ventilation spaces become small and complex, making it difficult to ensure adequate flow rates or distribution of ventilation air inside the ventilated assemblies. The ventilation space can be eliminated, and the construction simplified by using an unvented roof assembly.
For an attic to be used as a liveable space and/or a storage area, it must be unvented or “conditioned,” so the temperature is the same as the rest of the home. While there have been many debates on the subject, studies have repeatedly confirmed vents are not required if there is an airtight seal and moisture accumulation is controlled. Installing ccSPF insulation can help unvented attics in all climate zones. It has also been proven ventilation has minimal effect on a roof’s temperature (the colour of the shingles affects a home’s temperature).
Aside from providing usable living space, there are other benefits of an unvented attic such as:
• preventing ice-damming by controlling heat loss through the ceiling plane and ensuring snow is not blown into the roof space;
• fireproofing by preventing burning embers from entering the roof space (e.g. during a forest fire);
• increasing roof durability (by preventing ‘roof uplift’ in areas prone to extreme weather);
• helping mechanical equipment to operate more efficiently and preventing duct leakage;
• ensuring energy efficiency and preventing air leakage by installing medium-density ccSPF; and
• enabling more complex roof designs without compromising thermal, air, and vapour layers.
Usually, unvented attics have unvented roof assemblies, but one can still construct an unvented attic and vent the roof. The first way is by installing backing to spray the foam on from the interior, leaving an airspace above the insulation and below the roof sheeting and shingles/membrane to ventilate. The other option is to spray the foam from the exterior, on the interior finish, while leaving an air cavity above the foam to ventilate (Figure 1).
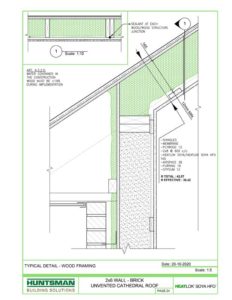
ccSPF in unvented roof deck assemblies
It is a big claim to say an insulation can save on heating and cooling costs by up to 50 per cent, but ccSPF insulation can do so. Some ccSPF products have the highest R-values in the industry at R-6/inch. Further, ccSPF adheres and conforms directly to common construction materials, regardless of shape and texture, making it suitable for areas which would be nearly impossible to insulate otherwise.
A ccSPF insulation product can be installed in different types of roof assemblies on various projects. In section 9.19.1.1, the National Building Code of Canada (NBC) requires continuous ventilation between the insulation and the roof deck except for where it can be shown to be unnecessary. In section A-9.91.1.1, it is said some specialized roof assemblies that demonstrate tightness to prevent any moisture accumulation would not require any ventilation. There are two options to consider in this regard:
- unvented roof where the product is installed directly under the roof deck (Figure 2); and
- unvented attic where the product is sprayed in the slope of the roof, but there is ventilation above the insulation (Figure 3).
Both these approaches require the sealing of all wood/wood junctions (Figure 3). In places where there are two pieces of wood side-by-side and there is no spray foam sealing the joint, a sealant must be applied for air/vapour barrier continuity. To ensure this continuity, ccSPF must also be sprayed down to the top plate of the wall. The moisture content of the wood, as required in the building code, should be of a maximum of 19 per cent. When ventilation is used, it should be at least 65 mm (2.5 in.) according to code (9.19.1.3.).
Warm air rises to the top of the house and it leaks out through the attic and the roof, which is why this area is considered the most important part of the home to insulate. Air leakage can account for up to 40 per cent of a building’s energy loss. Heating and cooling accounts for approximately 70 per cent of the average energy bill. However, what may not be known or understood, is fibreglass and cellulose insulation can leave gaps collectively equal to the size of a basketball and these gaps can also lead to excessive heat loss.
Sustainable building materials
Green construction trends will not cease. The demand for sustainable home building and green renovations will see an upward trajectory in 2021 and beyond. The green building market remained resilient in 2020, as consumers and businesses spent over $79 billion on green construction projects. This includes some modern-day medicine for the unvented roof deck assembly.
Most types of insulation will theoretically cut down on energy used for heating and cooling, and for this reason, they are considered environmentally friendly. However, this does not mean the product is sustainably sourced and toxic chemicals are eliminated.
Today’s ccSPF products use environmentally conscious blowing agents like hydrofluoroolefins (HFO). This gives it a zero-ozone depletion potential (ODP) and a global warming potential (GWP) of just one.
Some of the greener ccSPFs are made with recyclable material, such as 22 per cent recycled plastic and renewable soya oil. Resin drums incorporate greener innovation with one drum containing up to 3000 plastic bottles diverted from landfills. Since ccSPF adapts to all surfaces, shapes, and volume, the installation does not generate any waste. Reliable suppliers are also ensuring the packaging is sustainable, as the products system is sold in liquid form in returnable or recyclable containers. Some manufacturers have even pushed one step further in publishing their own environmental product declaration (EPD).
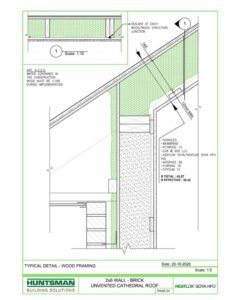
Only as good as the application
When it comes to an unvented attic job with the incorporation of ccSPF, the most important thing for a builder or contractor is knowing who they are working with. From equipment precision and handling of the chemical components to spray angle, technique is important when applying a ccSPF product. To avoid mistakes, it is advisable to work with a trained and certified installer. Certification is always provided by a third party, as mentioned in the Canadian Construction Materials Centre (CCMC) or Underwriter Laboratories (UL) evaluation of the product. In addition, avoid the following:
• spraying directly on chimneys (the installer should always leave a 150-mm [3-in.] gap between the chimney and the spray foam) or on rotten or humid wood (make sure it has been removed and repaired prior to the foam installation);
• removing older non-environmentally friendly insulation (this should all be removed prior to new ccSPF application); and
• ensuring the roof is watertight prior to the foam installation.
With the ever-increasing requirements from the National Energy Code of Canada for Buildings (NECB) and with the goal of every home construction being net zero by 2030, it is better to properly insulate. Since the roof is where most of a home’s air leakage and energy loss happens, it is better to go thicker with the ccSPF application than thinner. Ensure the certified installer properly insulates the first time to avoid coming back in 10 years or so to add more.
Conclusion
Home space is not the only demand to capitalize on, educated homeowners want efficiency throughout their homes. With ever-increasing certification requirements, such as Energy Star and Leadership in Energy and Environmental Design (LEED), they are sourcing contractors and builders with more of an ecological presence that leave less of a footprint, adhere to stricter building codes, and environmental laws.
Author
Maxime Duzyk is the director of building science and engineering with Huntsman Building Solutions. He holds a background in architecture and has been in the spray foam insulation business for the last 10 years. Duzyk is involved with different building envelope committees and associations in North America like CSC, SFC, SPFA, CCMC, and ULC Standards.