Evolution of below-grade waterproofing
Below-grade waterproofing: The unsung hero
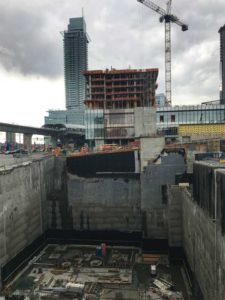
One of the most complex components of building design is the waterproofing system, especially the below-grade protective applications. They often have to serve several purposes across a building foundation, and must also be strategically applied to mitigate conditions. It can even be said, waterproofing systems are the unsung heroes of construction. When water, harmful gas, or contaminated vapour infiltrate a foundation, a structure’s performance could be compromised without effective, below-grade building envelope protection. Planning such protection is always a challenge, and site conditions can increase the complexity at an exponential rate.
There are two main classes of waterproofing conditions: Hydrostatic and non-hydrostatic. The former occurs when water present in the soil exerts pressure on a foundation or surface. The pressure can be quite intense—3 kPa (0.43 psi) of pressure is exerted for every foot of water present—and as foundations go deeper and rainfall ebbs and flows, it can increase. This pressure can essentially push water into the building, and problems occur when it puts additional strain on a building’s structural elements, for water can seep into cracks and holes. Non-hydrostatic conditions occur where there is an absence of water pressure or no significant threat of groundwater infiltration at the site and when a building foundation is not built below the established groundwater level.
Buildings need to be kept dry: It is simple. Concrete and shotcrete are inherently porous materials and can crack over time when a building has settled. This can be the result of below-grade water, among other issues, exerting pressure on a structure.
On sites with underlying contamination, unsafe vapours can migrate via diffusion or advective flow through imperfections below grade. Therefore, it is essential to place a barrier between the concrete and surrounding earth. The specified barrier must also be robust enough to prevent both water infiltration and the entry of harmful contaminants into the structure.
For non-hydrostatic conditions, the most common solution is a drainboard underlain by a simple membrane or ‘dampproofing’ material. The level and quality of the membrane selected is based on the anticipated surface runoff as well as estimated contact time for moisture and potential for infiltration.
Redundant layers offer more
In the author’s experience, most architects and waterproofing consultants are looking for at least one layer of redundancy in the design. This can be accomplished in two ways—the building team can either invest in a better membrane system or wait for leaks and treat with injection after completion of the structure.
The three main categories of waterproofing systems are:
- liquid-applied (cold or hot substance);
- prefabricated membranes (modified bitumen and elastomeric or thermoplastic sheets) and;
- mineral-based system (bentonite clay product or a crystalline material).
Bentonite, as part of a compound, is frequently specified for waterproofing. It is a type of clay that swells on contact with water and forms an impermeable barrier.
“Bentonite must be confined,” explains Steve Weiterman, a regional manager at a waterproofing product manufacturer. “Otherwise, it can become waterlogged, and depending on the conditions, it may need other ingredients added to it to provide adequate protection. When specifying this product, it is important to recognize the absolute requirement for confinement. Some commercially available products incorporate a process called ‘thermal-locked needle punching,’ which, in theory, guarantees a minimum level of confinement regardless of the installation conditions.”
Crystalline waterproofing is designed to reduce the porosity of concrete and will self-heal any water penetration into a concrete surface, provided the crack is within the conservative crack tolerance of the crystalline manufacturer.
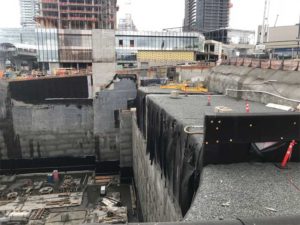
A single-component barrier, using one material only, relies on a single line of defence against water and contaminants. This is sometimes considered a ‘blanket solution,’ as this element is expected to solve several below-grade issues at once, and each of these conditions may require slightly different materials to ensure the building is protected. For example, groundwater can exert hydrostatic pressure on the foundation, resulting in cracks over time. The waterproofing material selected must be flexible enough keep the foundation watertight.
However, the main challenge with a single-component barrier is not always project-dependent. In fact, it is important the applicator is able to detail every seam perfectly—it is the weakest link as this is where the different materials join together. Good workmanship is key to a successful system, whether it is a single-component or redundant. When it comes to site conditions, however, a building envelope below grade can be extremely nuanced and because of this, a redundant system can work best for many different sites. At the same time, the system is only as good as the skill level and attention of the applicator, so highly trained professionals and proficient teams are key to the success of any below-grade waterproofing project.
“If a barrier requires redundancy, often you will see some kind of bentonite product specified to be applied under or over the base membrane,” Weiterman explains.
Redundant waterproofing systems achieve several goals. They protect against water infiltration, but with additional layers, they simultaneously ensure other contaminants are kept free from the building envelope. According to the Whole Building Design Guide (WBDG), redundant systems might be required when part of the building envelope will be permanently situated below the water table. There is no guarantee the groundwater can be effectively channelled away from the building on a permanent basis, so having a waterproof membrane with additional layering can be more effective.
Redundancy in a below-grade system can also be of indirect assistance to the construction team and onsite consultants. Often, once work begins, unforeseen challenges can become apparent, such as the presence of contaminants or gases, which were buried deep below the surface. This renders the one-size-fits-all type of solution less effective than redundant options combining several different kinds of materials to leverage the positive attributes of each and to eliminate a continuous seam. These materials can include a geocomposite base sheet, a spray-applied polymer modified asphalt, and a geocomposite sheet at varying thicknesses to accommodate different site conditions. It is important, with this kind of system, to eliminate a continuous seam in the waterproofing to avoid leaving the building susceptible to water or harmful vapours.