Essentials for protecting wood balconies from rain and rot
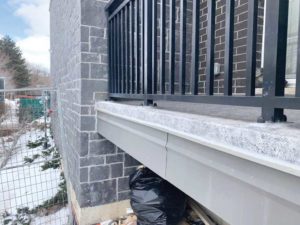
Downturns
At the front edge of a balcony, the sheet waterproofing membrane is terminated on a prefinished metal drip flashing. Metal drip flashings are typically fastened down onto the horizontal surface of the balcony with the drip extending beyond the balcony surface. The membrane is then adhered to the wood sheathing substrate and metal drip flashing, and the front edge of the membrane is terminated at the drip edge in a sealed plastic clamp. In this configuration, the thickness of the metal flashing on the horizontal surface creates a lip at the balcony edge. If there is insufficient balcony slope, this lip can cause water to pond near the balcony edge, and around top-mounted guard baseplates if applicable. Further, as the membrane ages and if it shrinks, the waterproofing at the front edge of the balcony pulls on the metal drip flashing, causing the front edge to rise. This exacerbates the ponding water issue and increases the risk of water penetration at top-mounted balcony guard baseplates.
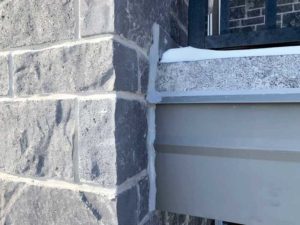
The key culprit in this approach is the metal drip flashing. If the drip flashing is instead installed vertically on the balcony rim board and fastened horizontally, the waterproof membrane will maintain its slope as it ages. This eliminates the risk of ponding water at the front edge and balcony guard baseplates. A durable repair is completed with a sealed metal clamp at the drip edge (Figure 19), combined with water diverters and sealant end dams (Figure 20) at the balcony-to-cladding interfaces to direct water onto the drip edge. A fastening bar can also be installed along the front edge on top of the waterproofing membrane.
Interfaces
Where possible, balcony waterproofing terminations should tie-in to the water control layer of adjacent building systems to provide continuous drainage. At balcony doors, the door should have a raised threshold and sub-sill flashing ship-lapped on top of the balcony waterproofing upturn, secured with a fastening bar. At rainscreen cladding interfaces, such as masonry or siding, a through-wall flashing should be provided above the surface of the balcony to allow for a proper upturn and ship-lapped interface. It is important the building systems remain decoupled to address system repairs separately. For example, allowing the balcony waterproofing to be replaced without the need to remove the balcony door.
Drainage
Balconies with solid balustrades are typically provided with a scupper or floor drain. The balcony should be properly sloped by shimming on top of the wood joists, and the area around the drain should be set lower to encourage drainage. A major risk with balconies with balustrades occurs when there is snow and ice buildup followed by a rain event. The snow and ice will block drainage, resulting in water building up on the balcony. This can cause the water to overflow the membrane upturns or door thresholds, resulting in major water penetration issues. It is critical that overflow scuppers are installed above the level of the deck, and yet below the lowest upturn elevation.
Maintenance, monitoring, and repairs
Regardless of the quality of detailing, complete diligent maintenance and monitoring are critical to maintain a watertight membrane. Snow and ice removal, sharp objects, or heavy furniture can also cause membrane tears or damaged seams. Maintenance should include periodic inspection for punctures and cleaning to confirm water is draining effectively off the balcony surface. This is particularly important where deck boards are provided on the balcony, concealing the waterproofing surface. It is also critical to conduct frequent inspections for concealed components to confirm structural safety and to identify issues before they become widespread or a structural issue. Soffit materials should be vented to allow wood elements to dry. Where solid soffit materials are already installed and it is not cost-effective to remove, access panels should be installed.
Monitoring is particularly important at engineered joists, since some manufacturers will not provide a splice repair detail, instead stating the full joist (all the way into the building) should be replaced. Where localized repairs are required to address damaged wood framing and sheathing, full waterproofing replacement should be considered to avoid back-lapped or unreliable seals at membrane seams. Identifying deterioration early—or preventing it altogether—is the first objective.
Key considerations
The following are key considerations waterproofing wood balconies or terraces:
- Pay attention to detail. Wherever possible, provide redundancy in detail design at penetrations and terminations and conduct reviews during construction to confirm compliance. Pay particular attention at top-mounted guard anchor penetrations. Use side- or wall-mount guards where possible to avoid waterproofing penetrations. Always provide upturns and consider interfaces.
- Provide for drainage and drying. Provide balconies with a positive slope to drain, especially at top-mounted balcony guard baseplates. Provide flashings, drip edges, and deflectors to direct water away from the balcony surface and building face. Consider other moisture sources, such as planters, eavestroughs, or cladding interfaces. Provide ventilation for wood elements to dry with vented soffit materials. Provide for overflow scuppers at terraces with balustrades.
- Inspect frequently. Conduct frequent inspections of concealed structural components and of readily visible waterproofing details to confirm safety. Check for damage to the membrane. Provide access panels at soffits to accommodate these reviews.
Notes
1 Refer to the Canadian Standards Association (CSA) standard, CSA S478:19, Durability in Buildings, page 12. Genge et al.
2 See this illustrated guide by BC Housing at
www.bchousing.org/publications/IG-Building-Safe-Durable-Decks-Balconies.pdf.
Authors
Stefan Nespoli, P.Eng., BSS is a project principal and shareholder in Edison Engineer Inc.’s Grand River office. He began his career as a contractor and gained valuable experience on condominium, commercial, and hospital project sites in Toronto and southwestern Ontario before finding his way to building restoration consulting more than a decade ago. Nespoli’s work focuses primarily with condominium clients, navigating capital planning and building repair challenges beginning shortly following initial construction.
Shawna Smigelski, P.Eng., BSS is a project manager and shareholder in Edison Engineer Inc.’s Grand River office. She is responsible for all aspects of project delivery, including building assessments, developing repair strategies and specifications, and construction. Smigelski is passionate about finding feasible repair options to tackle her individual clients’ needs, and improving the built environment by developing customized, durable repair solutions. She focuses on educating and communicating with clients to help them make informed decisions.