Environmental benefits of closed-cell sprayed polyurethane foam
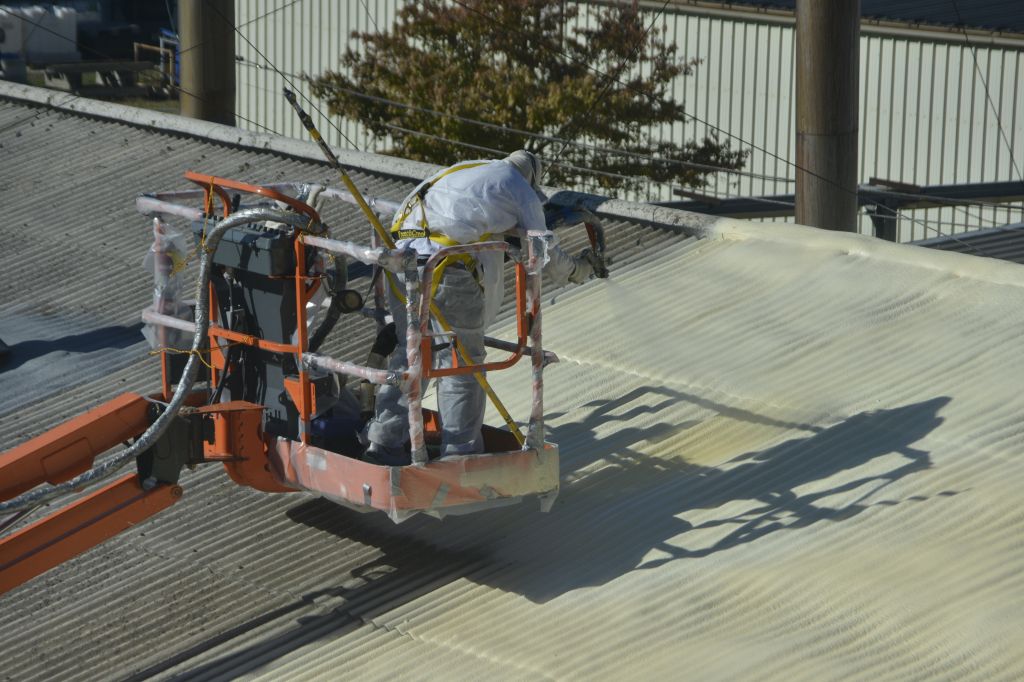
By Mary Bogdan and Xuaco Pascual
A focus on green building standards and more stringent code requirements has led to adoption of best practices in construction materials and methods. Among those is specifying more efficient insulation systems, air barriers, and seamless monolithic roofing assemblies. Use of closed-cell sprayed polyurethane foam (ccSPF) can help meet the stringent requirements of modern, sustainable building design.
This insulation material is spray-applied onsite to air-seal and insulate wall cavities, crawl spaces, attics, and basements. It is also used to insulate exterior walls and as a roofing system. Professional SPF contractors mix the foam ingredients at the jobsite. Sprayed as a liquid, it immediately expands to approximately 30 times its original volume. The foam adheres and contours to the spray surface filling in cracks and crevices that can cause air and water infiltration. It is used extensively for both commercial and residential projects.
Closed-cell SPF differs from its open-cell counterpart, ocSPF. Generally preferred for air barrier applications, ccSPF is significantly more dense and rigid, which means it can improve building durability and structural strength. It can be applied in all climates and is also the preferred material for severe weather conditions; the material also provides higher insulating properties than ocSPF. In addition, closed-cell sprayfoam is water-resistant, enabling use on exterior continuous wall installations, as well as roofing applications. (Open-cell SPF is susceptible to moisture absorption and typically is used for air sealing. It is not suitable for below-grade or flood-prone sites because it will absorb water.)
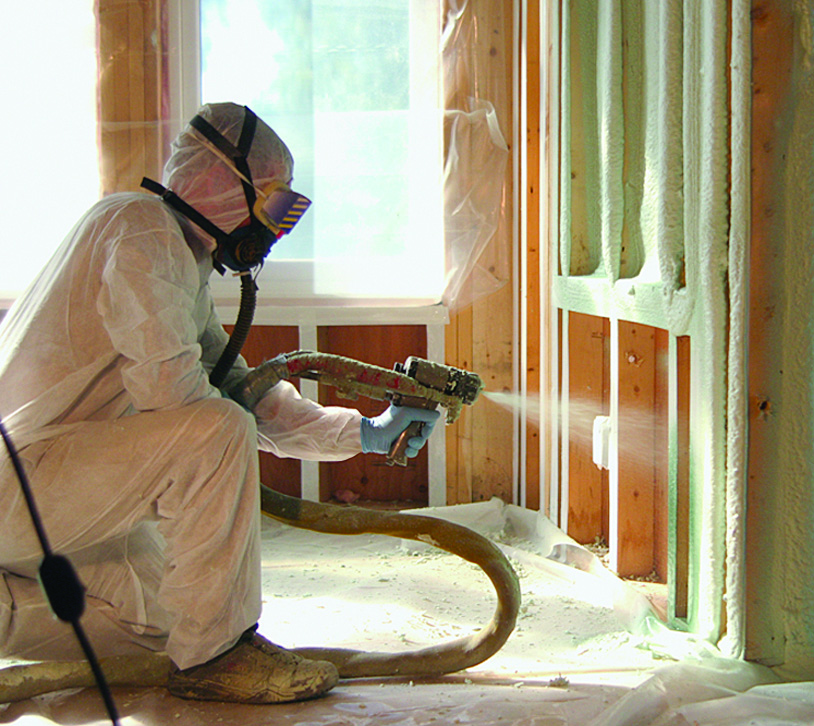
Green factors
Volatile and increasing energy prices, environmental impact, and occupant health and comfort are some of the main drivers for green building practices, which continue to grow in importance and acceptance by architectural and design communities. Tangible business benefits—such as return on investment (ROI), along with occupancy and rent increases—are being reported by commercial building owners and remain consistent over time.
A recent international study aimed at discerning trends and drivers of the global green building marketplace reported 91 per cent of global industry professionals expect to specify green building products within the next three years.1 Indeed, the same report suggests firms are shifting their business toward sustainable design/construction, with over half planning more than 60 per cent of their work to be green by next year.
The Canada Green Building Council (CaGBC) reports it has certified more than 1000 projects under its Leadership in Energy and Environmental Design (LEED) program, and registered over 4000. This represents the second highest number in the world, after the United States. Additionally, Canada has adopted several national and regional programs such as EcoDistricts, Living Building Challenge, Passive House, Green Globes, and EnergyStar, indicating the country is at the forefront of the green construction movement.
Quantifying the green building benefits of specific technologies can be complex. It requires the evaluation of a long list of criteria in a full lifecycle analysis (LCA) to determine overall product performance (related to manufactured products) and full system performance (related to buildings as a whole). This article examines closed-cell sprayfoam within this paradigm.
Environmental responsibility and ccSPF
With green building programs like LEED and Green Globes focusing on energy efficiency, it is not surprising the choice of insulation can have a significant impact. When considering insulation for new construction or retrofit projects, it is important to examine what makes ccSPF unique.
When considering the environmental benefits of an insulation, ccSPF stands apart due to its unique combination of thermal and air sealing performance, water resistance, self-adhesion, and structural strength.
This combination allows ccSPF to:
- provide superior thermal performance compared to traditional materials like fibreglass or cellulose, including unparalleled air-sealing to improve overall building envelope performance;
- lower energy use in buildings, which in turn can reduce carbon emissions and lower costs;2
- prevent air leakage, reducing the load on heating and cooling systems (e.g. HVAC sizing can be reduced providing cost savings and environmental benefits without the loss of efficiency and comfort);3
- offer moisture protection, which can help prevent mould and mildew issues;
- add structural integrity, which can increase building durability and longevity;4 and
- be applied to commercial roofs as a recoat (versus tear-off)—since ccSPF roofing systems are so durable, they can have a serviceable life of more than 30 years and be easily recoated, diverting material from landfills.
As an added environmental benefit, polyols (a key ccSPF ingredient) are increasingly being made with renewable-resource-based content, such as soy. Another key component of ccSPF that enables many of its attributes is use of a high-performance foam blowing agent to help create tiny bubbles or cells in the foam, improving insulating properties.
Advancements continue to be made in foam blowing agent technology. For example, one producer has an agent that is non-flammable and non-ozone-depleting, and has a reduced global warming potential (GWP) of ‘1.’ (This is equal to that of carbon dioxide [CO2] and orders of magnitude lower than traditional hydrofluorocarbon [HFC] blowing agents used in the industry.)5
Lifecycle analyses
To fully assess the environmental impact of insulation, one must consider the overall impact of manufacture, service, and disposal. A common tool for evaluating this impact is lifecycle analysis, and a common measure for this is the embodied energy (often expressed as carbon footprint) associated with that product.
Although there are many ways to evaluate the carbon footprint of a product, the current, internationally recognized LCA method is found in International Organization for Standardization (ISO) 14040, Environmental Management: Lifecycle Assessment−Principles and Framework. The LCA comparison avoids pitfalls associated with current single-attribute measures, which often do not provide a measure of true environmental impact.
The Spray Polyurethane Foam Alliance (SPFA) completed an LCA study for open- and closed-cell SPF insulation in 2012, which conformed to the ISO 14040/44 standards.6 This study is the material’s first comprehensive LCA conducted in North America. Specific to ccSPF, the analysis evaluated the environmental impact of using current ccSPF products in single-family residential, as well as commercial roofing structures in three different climate zones of the United States—one of which was Minneapolis, Minnesota, representative of conditions similar to many Canadian cities. Figure 1 depicts the basic components of a comprehensive ccSPF LCA.
The LCA results showed SPF products save significantly more energy and prevent more environmental impacts during the life of the insulation in a building compared to the relatively minor energy and environmental impacts associated with making the insulation. Primary energy investment was found to be recovered in less than two years for ccSPF, with greenhouse gas (GHG) releases recovered in less than eight. For all categories studied, embodied environmental impacts from manufacturing are minimal when compared to those impacts avoided during insulation use over a 60-year period.
Blowing agent LCA study
To expand on this research, a blowing agent manufacturer repeated the study and substituted data with ccSPF formulated with a low-global-warming-potential (LGWP) blowing agent in the application.7 In other words, the assumptions used in the embodied energy and use phase of the blowing agent manufacturer study are identical to those used in the SPFA study, except for the blowing agent data.8 The findings focused on two main parameters of ccSPF containing the LGWP blowing agent—the total embodied energy and GWP payback.
Figure 2 provides a relative comparison for the carbon footprint of general materials used in construction. The study shows ccSPF formulated with the LGWP blowing agent has a relative lower environmental impact (i.e. carbon dioxide [CO2] equivalence per square foot) compared to commonly used construction materials, such as nylon carpeting or brick siding.
In addition to having a lower carbon footprint than commonly used construction materials, ccSPF insulation containing the LGWP blowing agent provides considerable energy savings over the life of a project. The GWP payback is a measure of the time in which a product’s environmental impact is paid back through a benefit offered, in this case energy savings. Figure 3 shows the GWP payback periods associated with residential and commercial roofing applications. Within as few as six months, ccSPF formulated with the LGWP blowing agent starts providing a net environmental benefit for the remainder of the project service life.
Green building design drivers
Building rating programs like LEED and Green Globes typically focus on numerous factors, ranging from energy efficiency and site to material use and indoor environmental quality.
Energy efficiency and the building envelope
Generally, energy-efficient construction begins with building envelope performance. A high-performance envelope involves two significant factors: high levels of effective insulation and a superior air barrier system. The effectiveness of the latter depends on many factors, including the type of assembly, material choices, installation quality, and how well the system is integrated into the overall building enclosure.
Not only can ccSPF provide the highest R-value per inch of any insulation system,9 it also acts as an air barrier that provides a solution to thermal bridging. In Canadian commercial buildings, this is particularly significant. In steel stud walls, thermal bridges generated by steel components reduce thermal performance by up to 55 per cent.10 This reduced insulation effectiveness can lead to lower wall cavity temperatures, which may result in moisture problems. As ccSPF systems do not require metal fasteners and can continuously cover existing thermal bridges, this can reduce or eliminate the effects.
Site selection and sustainability
The urban heat island effect is a considerable issue in metropolitan areas, where the lack of vegetated ground cover can lead to urban air temperatures 1 to 3 C (2 to 5 F) warmer than rural areas (Figure 4).11
This temperature increase dramatically impacts energy use, mechanical system operation, indoor air quality (IAQ), and occupant comfort. The U.S. Lawrence Berkeley National Laboratory (LBNL) studies to reduce the urban heat island effect have focused largely on cool roofs—assemblies that use light-coloured, reflective roof coatings that can dramatically reduce energy use and, if widely used, can help reduce temperatures in urban areas (Figure 5).
These benefits are not only limited to hot climate areas. In fact, cool roofs can significantly benefit colder regions in North America. For example, Toronto enacted the Green Roof By-Law in 2009 and has adopted the Eco-Roof program, which provides incentives for the use of cool roof technology. The program has since impacted over 140,000 m2 (1.5 million sf) of roofs with cool roof technology, and has credited for significant energy savings and avoidance of 38 tonnes of greenhouse gas emissions annually.12
Closed-cell SPF roofing systems can provide a suitable commercial cool roof solution because they can be combined easily with high-reflectivity, low-emissivity (low-e) roof coatings. They can also be used under vegetated roofs to reduce roof surface temperature and increase building performance. Additionally, ccSPF roofing systems are effective for reroofing over existing standing seam metal, built-up (BUR), modified bitumen (mod-bit), and single-ply assemblies.
Material and resource use
Another significant green building driver centres on reducing or diverting construction waste. In Canada, millions of tonnes of building-related construction and demolition materials are generated each year.
Closed-cell SPF is applied onsite by professionals who use only as much material as is needed, minimizing construction waste. More significantly, prolonging building life can reduce resource consumption and waste generation resulting from building replacement.
Surveys conducted by Dr. Dean Kashiwagi (Del E. Webb School of Construction at the University of Arizona) have documented the exceptional durability of ccSPF roofing systems.13 More than 1600 roofs were surveyed across a number of U.S. climate zones, many of which are similar to southern Canadian regions. Of all the roofs surveyed:
- 97.6 per cent did not leak;
- 93 per cent had less than one per cent deterioration; and
- 70 per cent were applied over existing roofs.
The oldest performing roofs were more than 26 years old. Fundamentally, the studies demonstrated the physical properties of ccSPF roofs did not diminish over time and highlighted their sustainability.
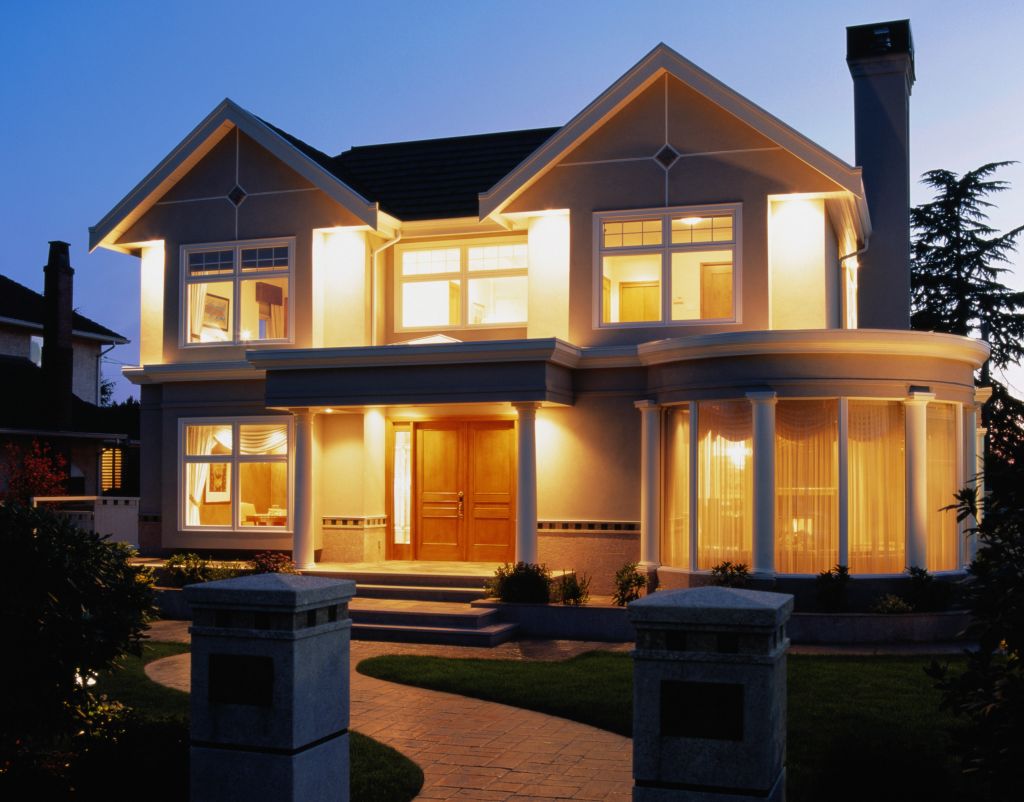
Indoor environment
HVAC performance and emissions from building components and furnishings can dramatically impact indoor air quality. Building envelope performance is paramount to good IAQ. A poorly insulated, leaky envelope can result in condensation and mould growth, as well as invasion by outside contaminants, not to mention reductions in energy efficiency.
An airtight building envelope, in conjunction with controlled ventilation and fresh air make-up, is critical for controlling pollutants, volatile organic compounds (VOCs), and other contaminants that may affect IAQ. The use of ccSPF can improve IAQ because it acts as an integral air barrier and also functions as a vapour retarder.
Innovation and design process
Under LEED, Innovation and Design (ID) credits provide architects, engineers, and specifiers an opportunity to promote the merits of ccSPF. Closed-cell sprayfoam can contribute to innovation credits for acoustical performance, reducing construction waste (e.g. reuse of existing roofs), variable and renewable raw materials sources (e.g. soy-based polyols), superior energy efficiency, and reduced freight. For more information, suppliers should be contacted to determine how using ccSPF conforming to Underwriters Laboratories of Canada (CAN/ULC) 705, Spray-applied Rigid Polyurethane Foam Insulation, Medium Density, can contribute to LEED points for a specific project.
Conclusion
The choice of insulation/air barrier systems is critical to green building design and construction. Although there are many materials that purport to provide environmental benefits, closed-cell sprayed polyurethane foam’s combination of air-sealing/insulating capabilities, moisture resistance, strength, and durability make it worthy of consideration for green building design. SPF insulation helps address core issues associated with the energy, moisture, and durability of a building in an all-in-one solution.
Notes
1 Developed in partnership with United Technologies Corp., McGraw-Hill’s “Construction SmartMarket Report” can be read at www.construction.com/about-us/press/world-green-building-trends-smartmarket-report.asp. (back to top)
2 As savings vary, it is important to check the seller’s fact sheet on R-values. (Higher R-values mean greater insulating power.) (back to top)
3 For more, visit the Canadian Urethane Foam Contractors Association (CUFCA) website, www.cufca.com. (back to top)
4 This comes from the 1992 U.S. National Association of Home Builders (NAHB) Research Center report, “Testing and Adoption of Spray Polyurethane Foam for Wood Frame Building Construction,” for the Society of the Plastics Industry/Polyurethane Foam Contractors Division. Visit www.sprayfoam.com/spps/ahpg.cfm?spgid=74. (back to top)
5 When specifying a sprayfoam system, it is beneficial to contact blowing agent manufacturers to discuss the latest technology available. (back to top)
6 Visit SPFA’s site at www.sprayfoam.org. (back to top)
7 For more, see the authors’ article, “Environmental Assessment of Next-generation Blowing Agent Technology using Solstice LBA in ccSPF,” in the October/November 2012 issue of PU Magazine. (back to top)
8 At the time of the LCA, the blowing agent used in the study had a GWP of < 5. It has now been shown to have a GWP of 1. Therefore, LCA results may be even more favourable. (back to top)
9 It is important to check the SPF seller’s fact sheet for specific R-values when comparing sprayfoam to other insulations. (back to top)
10 This comes from work by Jan Kosny, Jeffrey E. Christian, and André O. Desjarlais at Oak Ridge National Laboratory’s (ORNL’s) Buildings Technology Center. (back to top)
11 For more on heat islands, visit heatisland.lbl.gov/coolscience/cool-science-cool-roofs. (back to top)
12 Visit www.coolrooftoolkit.org/wp-content/pdfs/CoolRoofToolkit_Full.pdf. (back to top)
13 The Kashiwagi findings were also reported by Mason Knowles on a blog at sc.leadix.com/honeywell/commercial/blog.php?mid=247. (back to top)
Mary Bogdan is a senior principal scientist for Honeywell. She earned a bachelor’s degree in chemistry/biochemistry and an MBA from Canisius College. Joining Honeywell in 1989, Bogdan currently supports the fluorine products blowing agent business leading application research projects and providing technical service to the global spray foam industry. She has more than 20 U.S. patents and numerous published technical articles on the development and use of fluorocarbons as blowing agents. Bogdan is currently a member of the Spray Polyurethane Foam Alliance (SPFA) board of directors. She can be reached at mary.bogdan@honeywell.com.
Xuaco Pascual is a global marketing manager for Honeywell with responsibility for sprayfoam applications. He holds a degree in mechanical engineering from Old Dominion University and brings more than 15 years of experience with construction building envelope solutions focused on energy, moisture, and sustainability practices. Pascual has several patents in construction, composites, and consumer applications. He can be reached at xuaco.pascual@honeywell.com.