Ensuring Energy Efficiency: Specifying windows and curtain walls for cold climates
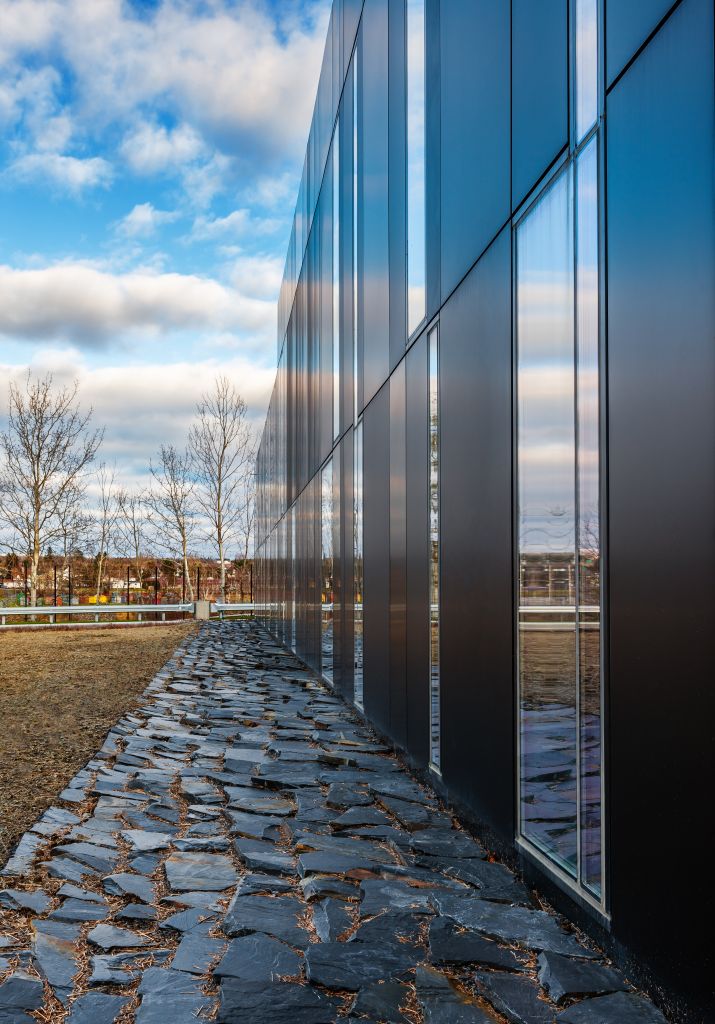
By Steve Fronek, PE
In most parts of Canada, commercial building energy efficiency is significantly affected by conductive heat loss. In the winter, resistance to undesirable condensation on interior surfaces is important. New insulating glass and framing options are available to reduce heat loss and air leakage, control solar heat gain when appropriate, and minimize the potential for condensation.
However, understanding how to best specify materials for a particular project involves first knowing the basic principles of heat transfer, which occurs from objects of higher temperature to those of lower through conduction, convection, or radiation.
Conduction, convection, and radiation
Heat transfer through solid materials takes place via conduction. While aluminum is widely used as an engineering material because of its strength, light weight, and ability to accept durable finishes, it exhibits a high thermal conductance. This attribute makes an aluminum surface ‘cold’ to the touch, even when its surface is quite close to ambient air temperature, since heat quickly transfers from the skin to the aluminum.
In an aluminum window or curtain wall, the most common means of reducing conductive heat transfer through framing is by adding low-conductance ‘thermal break materials’ such as polyurethane, fibre-reinforced polyamide nylon, polyvinyl chloride (PVC), or flexible elastomers like silicone, neoprene, or ethylene propylene diene monomer (EPDM). All these thermal break materials exhibit unique design advantages and limitations.
Effective thermal barriers may be either structural (i.e. designed to resist wind loads and dead loads as an integral part of the extruded aluminum assembly) or non-structural (i.e. designed to be supported by fasteners or interlocks). The National Building Code of Canada (NBC) requires thermal breaks in metal window and curtain wall framing.
Non-conductive wood, cellulosic composite, vinyl, and fibreglass framing has each captured or retained significant market share in residential markets, but for the reasons mentioned, thermal barrier aluminum remains the material of choice for non-residential applications.
Heat transfer through fluids (either liquids or gases) takes place via convection. A change in medium from solid to gas, as occurs at a glass-to-air surface, has an inherent resistance to heat transfer. Convective heat transfer commonly is reduced by the addition of air spaces in insulating glass (IG) units. The U-factor of IG units can be further reduced by filling the between-glass spaces with lower-conductivity inert gases such as argon or krypton.
In framing areas, convective baffles or cavity fillers can be employed to impede convective heat flow, providing incremental improvement in U-factor.
Heat also can transfer in the absence of any intervening medium solely due to temperature difference between two objects. This radiation heat transfer depends not only on temperature difference, but also on ‘view factor’ (i.e. a measure of the amount two surfaces ‘face’ each other), as well as on the emissivity and absorptivity of the facing surfaces.
Low-emissivity (low-e) glass has an almost-invisibly thin coating—only Angstrom units (one ten-billionth of a metre) thick—that is reflective to long-wavelength infrared radiation, but transparent to shorter wavelength visible light. Both pyrolitic ‘hard-coat’ and sputtered ‘soft-coat’ low-e glass coatings are designed to reduce radiation heat transfer.
In framing areas, cavity fillers can be employed to impede radiation heat flow by reducing view factor between warm and cool surfaces.