Enhancing ICF performance
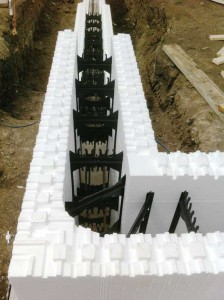
Increasing performance
Over the past 15 years, ICF block sizes have remained unchanged largely due to the high cost manufacturers would incur to create new block moulds. This has limited the insulating value of ICF structures.
In response to the recent upswing in insulation demand, both from customers and building codes, manufacturers have introduced improved, enhanced-performance ICFs. One type is made with a specialized form of expanded polystyrene with different properties than standard white EPS. Graphite-impregnated EPS ICFs typically have a grey or silvery appearance, giving rise to several brand names that include a reference to ‘metal.’ The EPS beads are coated before expansion to yield a widely spaced distribution of graphite
(i.e. black carbon particles) in the light-coloured EPS.
The manufacturer of a graphite-impregnated EPS product (used by various ICF manufacturers to mould blocks) says the material’s effective R-value can be 20 per cent higher than white EPS. Despite the temptation to think the silvery colour is more ‘mirror-like,’ this claim is not based solely on increased reflectance, but also heat absorption. In other words, graphite is giving the EPS higher thermal mass. This suggests the actual boost in effective R-value may vary with the conditions affecting thermal mass performance.
A representative of one ICF manufacturer that uses graphite-impregnated EPS has told the authors the R-value increase is actually closer to 15 per cent in his experience. In a conventional-thickness ICF, this means the total effective R-value increase would thus be limited to 3.15 for a system total of R-24.15. Assuming the manufacturer’s 20 per cent figure, a total system value of about R-26.5 would be achieved.
A possible problem with graphite-impregnated EPS has been mentioned by a contractor in the southwestern United States. On two projects, portions of graphite-impregnated EPS blocks melted during the construction process.
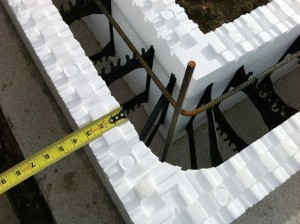
The first incident was during construction of a fire station in Scottsdale, Ariz., in the summer of 2010—blocks that had been outside for three or four days had their inside corners melted. Daytime temperatures had been about 38 C (100 F)—not normally high enough to melt EPS. In this instance, concrete had already been placed and was curing before the meltdown, so damaged insulation could not readily be replaced. Since the structural integrity of the wall was not affected in any way, the missing insulation was simply drywalled over. (One of the advantages of ICF construction is because there is insulation on the interior and exterior, any defects like this can be covered over with minimal loss of R-value. The complete system insulation, thermal mass, and airtightness is very forgiving; in this case, the practice of covering the defect would not have had a major loss of performance as it would have with traditional stick-frame and fibreglass construction).
The second incident occurred the following summer while constructing a custom home in Cave Creek, Ariz. Several pieces melted in inside corners, and also along one straight run of wall. Daytime temperatures were once again about 38 C. In this case, concrete had not yet been placed, and the damaged blocks were trashed and replaced before concreting.
When the manufacturer was consulted, the contractor was offered several possible explanations, such as a mirror-like effect, reflecting sunlight onto the blocks. None of the explanations seemed to apply to the project circumstances. It was deemed possible sun reflection from the concrete slab, or from the opposite wall of blocks, may have increased the radiant heat, and the energy absorption of the graphite surface caused the blocks to heat to the melting point.
Granted, one might assume what may be problematic in Arizona would not be an issue in Canada. However, it is important to note ambient temperature does not seem to have been the issue—the air was not hot enough to melt the EPS. The conjecture is radiant heat (i.e. the intensity of the sunshine) reflecting off these dark-coloured blocks led to the heightened temperatures at the corner. Essentially, this ‘melting’ problem could theoretically happen anywhere on the continent.
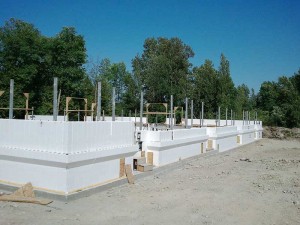
Thicker insulation
The other route toward higher performance is to increase insulation thickness. As previously stated, the price of new manufacturing tooling has long been a barrier to this approach.
One solution is to use standard ICF blocks and add sheets of additional EPS to the interior of the blocks as they are being placed. If the structure called for 150-mm (6-in.) concrete walls, 200-mm
(8-in.) ICF blocks would be used, and 25-mm (1-in.) EPS sheets would be added to each side of the block’s interior.
This type of product, however, has been reported to cause problems with concrete consolidation; the added sheets can be prone to being displaced or damaged while using a vibrator . (The normal process for an ICF form is to add rebar inside the block as it is being stacked. By adding additional EPS sheets or panels inside the block, it further compromises the opening available to allow a vibrator inside the block as concrete is being poured. Further, without visual capability to ensure the additional EPS panels have not moved, there is potential for air pockets inside the block that could affect structural properties. The most secure way of fixing additional panels would be to use a foam-to-foam adhesive when installing to ensure there is no separation. However this adds to the labour and time component).