Enhancing ICF performance
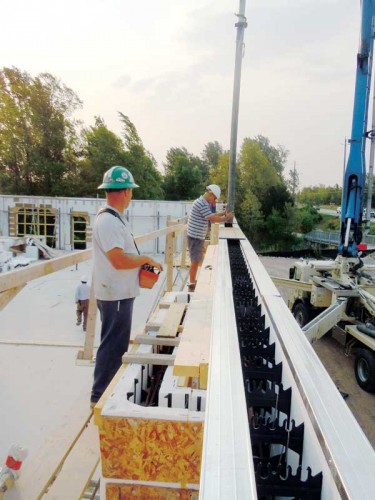
By Gary Brown and Steven H. Miller, CDT
Insulating concrete forms (ICFs) offered an energy-efficient mode of construction long before sustainability was widely pursued, or even understood, in the overall building industry. In the intervening years, competing building methods have seen improvements in thermal energy efficiency, but the properties of ICF have remained virtually constant, until recently.
There has been (more or less) one standard thickness of insulation available, and the most widely used insulating form material—expanded polystyrene (EPS)—has remained unchanged. In the past few years, however, manufacturers have stepped up their insulating capabilities. To stay ahead of the sustainability curve, they have pursued different strategies for getting a higher effective R-value from their wall systems. The resulting products, which can be thought of as ‘enhanced-performance ICFs,’ deliver the advantages of traditional forms, along with a significant increase in energy efficiency.
Sources of energy efficiency
As its name suggests, an ICF is a method of making structural concrete walls (and other structural elements, though this is beyond the article’s scope) using formwork with insulating properties. Designed to be left in place to serve as insulation, the formwork itself has certain permanent structural properties allowing the attachment of interior and exterior finishes. (The properties and details of ICF construction have been previously covered extensively in Construction Canada. Readers can find greater detail on the system in Gary Brown’s July 2010 article, “Building With Insulating Concrete Forms,” or “ICFs and the New Green Standards,” by Paul Nutcher in the January 2012 issue. For more, visit www.constructioncanada.net and select “Archives.”) Essentially, the completed wall is a concrete sandwich with EPS for bread slices.
The sandwich derives energy efficiency from both concrete and EPS, the latter of which contributes its insulating value. Its thin internal cellular structures provide resistance to thermal conduction—the primary property measured in R-value tests. Its light colour reflects radiant heat, reducing the second mode of heat transfer. (Since this concerns radiant heat reflection, the issue of actual exposure to the elements is irrelevant. Radiant energy entering through either the cladding (from the exterior) or the drywall (on the interior) can then transfer by conduction, convection, and radiation. Every hot object gives off some radiant energy—this is why infrared photography works, and why the tip of one’s nose looks darker on an infrared photo than one’s cheeks, even though they reflect the same color in the visible spectrum. The light colour of the EPS reflects not only visible spectrum, but also infrared—radiant energy. It reflects radiant energy even in total darkness). Its closed surface resists convection of hot air through the insulating material.
White EPS is generally given an R-value of about 4.1. Since R-value testing primarily measures resistance to conduction, it should be noted two materials with similar R-values may have differing performance due to radiant energy absorption or reflection. A dark-coloured material with little reflectance absorbs more radiant energy at its surface than a light-coloured one. Although both materials may offer similar resistance to conducting heat from the surface through the material’s thickness, the dark-coloured material has more heat to resist, and therefore more heat transfers.
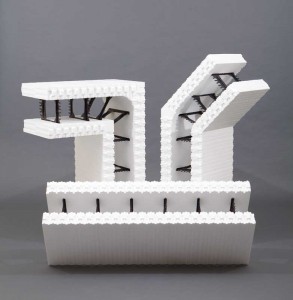
Since the introduction of EPS ICFs, most available systems have featured pairs of 65-mm (2.5-in.) thick panels, for a total insulation thickness of 130 mm (5 in.). Adding in the (low) insulating value of the concrete wall, plus additional value from the interior and exterior finishes, a total system resistance of about R-22 has been common for ICF walls.
The concrete provides thermal mass, which is the ability to absorb and retain heat energy (see “Understanding Thermal Mass,” page 38). When heat is applied to one side, it must ‘fill’ the concrete before it can be transmitted to the cool side. This can slow interior heat gain when the sun is shining. When the concrete has stored heat and the surrounding temperature drops, the concrete gives back its own heat before transmitting it from one side to the other. This can help maintain more evenness in the interior temperature when the exterior temperature drops at night.
Thickness of concrete in an ICF assembly—and therefore available thermal mass—is usually determined by the wall’s structural requirements, not its insulating requirements. ICF blocks are available in standard sizes ranging from 100-mm (4-in.) concrete thickness up to 300 mm (12 in.), meaning available thermal mass may vary by up to 300 per cent between projects. It would, of course, be possible to use a thicker wall than structurally necessary to boost thermal mass, but it is not usually done. (For various reasons, walls are usually sized for structural needs, rather than thermal mass performance.)
Thermal mass increases the system’s effective energy efficiency, but the amount of that boost depends on climate conditions. Calculating a specific system’s performance is complex, and must factor in not only the wall materials, but also the prevalent exterior temperatures and day/night temperature swings.