Energy and comfort transformations in multiresidential buildings
by Olivier Matte, Ekaterina Tzekova, PhD, and Keith Burrows, LEED AP
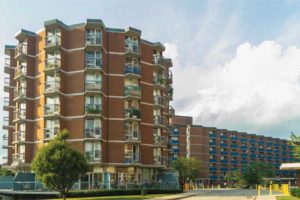
The Atmospheric Fund (TAF) and Ecosystem have partnered with Toronto Community Housing Corporation (TCH) to perform energy retrofits on seven multi-unit residential buildings (The Toronto Community Housing Corporation (TCH) manages more than 2100 buildings in Toronto. Founded in 1991, The Atmospheric Fund (TAF) invests in urban low-carbon solutions in the Greater Toronto and Hamilton Area to reduce carbon emissions and air pollution. Ecosystem is a fully integrated design and construction engineering firm specializing in buildings’ energy ecosystems.). These retrofits, which are part of the TowerWise program, have reduced annual utility bills by $492,000 and carbon emissions by more than 920 tCO2eq per year, while addressing thermal comfort and ventilation issues for residents.
Maintaining housing affordability and indoor comfort while addressing high utility costs is an ongoing challenge for multiresidential building (MURB) owners. Through the TowerWise Retrofit Project, TCH saw a great opportunity to address these high utility costs (pre-retrofit energy use intensity was 284 to 318 ekWh/m2) as well as commonly experienced operational challenges such as year-round thermal comfort and poor ventilation.
Finding the right partners
TCH and TAF identified seven buildings within TCH’s portfolio that would benefit from deep energy retrofits. These sites were chosen based on their varied building form (low-, mid-, and high-rise) and occupant profiles (individuals, families, and seniors). Together, they contain more than 1200 units.
TAF and TCH issued a public request for proposal (RFP) in October 2014 with the goal of finding a design-build firm that could maximize project outcomes and utility cost savings. Rather than specifying desired equipment, systems, or services, TAF and TCH issued an outcomes-based RFP, providing bidders with the option of developing solutions to best achieve the desired project outcomes such as:
- improving tenant comfort by enhancing indoor environmental quality;
- decreasing greenhouse gas (GHG) emissions by 30 per cent;
- reducing energy consumption and utility costs by 20 per cent; and
- minimizing annual operations and maintenance costs.
The goal was to work closely with a firm that could effectively capture the needs of a range of stakeholders—including tenants, building superintendents, TCH Smart Buildings and Energy Management unit, and building operations/maintenance teams—using an integrated approach. Given the nature of this performance agreement, the bidders also needed to guarantee the expected utility cost savings and financial incentives, as well as monitor and verify the savings during the agreement period.
Maximizing outcomes
The winning firm, Ecosystem, a Canadian design-build company, began the project with an extensive energy audit of all the seven buildings. Next, the team undertook several design charrettes to discuss and prioritize the retrofit solutions. These meetings included a variety of project stakeholders (TAF, Ecosystem, TCH, energy management and facility maintenance teams, and building superintendents) and industry experts. The project team also took advantage of this integrated design process to collect energy and indoor environmental quality information to help prioritize the energy retrofit measures.
After a six-month analysis, the project team finalized the following energy retrofit measures:
- installing 3-L (0.8-gal) low-flow water closets;
- converting interior and exterior light fixtures to light-emitting diode (LED) luminaires;
- installing motion sensors in underground garage bays, garbage rooms, and mechanical rooms;
- cleaning radiators;
- installing condensing boilers with high modulation capability (a condensing boiler is a high-efficiency [typically over 90 per cent efficiency] boiler, most often producing hot water. It is designed to condense water vapour in the exhaust gases and, by doing so, it recovers the latent heat of vapourization, which would otherwise have been wasted);
- using gas absorption heat pumps for domestic hot water;
- cleaning of fresh air supply and return ducts;
- installing new makeup air units with heat recovery and variable frequency drives (a variable frequency drive [VFD] is an electronic component that controls AC motor speed and torque by varying the frequency and voltage of the electricity input. By doing so, a VFD allows for matching the motor energy consumption to the real-time needs in the building, so the motor does not have to run at 100 per cent speed all the time. A VFD is installed upstream of the motor’s electric input.);
- modulating booster pumps for domestic water; and
- installing new in-suite smart thermostats.