Energy and comfort transformations in multiresidential buildings
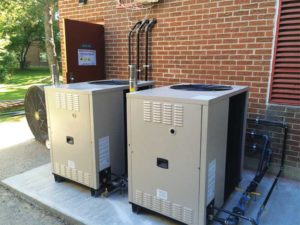
Photo courtesy Ecosystem
Getting a head start
Given a tight construction timeline of nine months, the project team leveraged the flexibility of an integrated project delivery approach and began with implementing the simplest measures such as water closet replacement and lighting. During this time, the design was fine-tuned for the more complex heating-related measures.
Work got underway in May 2016, with the installation of more than 1200 new high-efficiency, 3 L water closets. To assist with these installations as well as other in-suite measures, the project team engaged Building Up, a nonprofit social enterprise creating green employment opportunities for individuals experiencing barriers when entering careers in the building industry. This project employed more than 12 community members for an equivalent of 1650 person-hours. Overall, replacing the water closets has resulted in saving more than 53,600 m3 (1.9 million cf) of water (equivalent to a 27 per cent reduction) and $189,000 in utility savings over the first year of performance. Actual savings significantly exceeded projections because the new water closets are equipped with valves rather than flappers, a source of continuous water leakage with older models.
The lighting upgrades included a complete conversion to LED. Common areas, as well as underground garages and outdoor lighting, were changed in 2016. Rather than a one-for-one replacement, an improved fixture configuration resulted in better lighting uniformity in corridors.
To further reduce energy waste, motion sensors were installed in the underground garage at the two high-rise buildings, which resulted in an 88 per cent electricity consumption reduction. Improved quality and intensity of light, along with the automated “on/off” switching provided by the motion sensors, increased the feeling of security in the garage and in the outdoor areas.
Upgrading water heating equipment
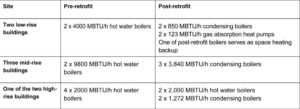
Image courtesy The Atmospheric Fund
Changing boilers should never be seen as a simple, one-for-one replacement. In addition to installing highly efficient condensing boilers, these retrofits needed to ensure the equipment is within the condensing temperature range for the majority of time. The project team achieved this by improving radiator controls for residents, which helped reduce the overheating and resulted in fewer windows being opened during the winter. The piping was also modified to ensure the lowest possible return temperature to the boiler room. Reducing energy waste in the units and across the hot water network allowed for optimal sizing of the new heating equipment. The project team reduced the total heating capacity and installed condensing boilers with high modulation capacity to ensure the building supply was better aligned with actual demand. Figure 1 shows the pre- and post-retrofit heating capacity at each site.
At the two low-rise buildings, two new condensing boilers were installed, sized to handle most of the heating load, aside from the coldest days of the winter. In this case, one of the old boilers is enough to supply the remaining load. Two new air-source gas absorption heat pumps (GAHPs) were also installed to produce domestic hot water. They have been sized to provide about 60 per cent of the hot water load, ensuring a fairly constant operation. The new condensing boilers are designed to meet the remaining load.
The GAHP technology uses natural gas to drive the refrigeration cycle. They are more efficient than condensing boilers, achieving operational efficiency in excess of 100 per cent. In Toronto, GAHPs are significantly less expensive to operate than their electric heat pump counterparts.
The two GAHPs have performed well, with an average daily coefficient of performance (COP) of 1.14 for the period of November 2017 to May 2018, and an average COP of 1.24 for the warmer months of May and June. Although GAHP efficiency degrades in cold ambient temperatures (as with electric air-sourced heat pumps), daily COP values exceeded 1 throughout the winter. Compared to the original boilers at the site, the GAHPs saved approximately 3360 m3 (118,657 cf) of natural gas since November 2017, and TAF projects they will save 8400 m3 (296,643 cf) of gas and over 15 tCO2eq of carbon emissions over a one-year period.
At one of the two high-rise buildings, two of the four existing boilers were replaced with new condensing boilers. One is mostly dedicated to domestic hot water heating, enabling it to maximize time spent within the condensing range. The second boiler is dedicated to space heating.
The other high-rise building did not need major equipment upgrade, but it underwent an extensive recommissioning process.
By September 2017, the central space heating boiler room at the mid-rise building site was undergoing major renovation. The two existing boilers were demolished and replaced by three new condensing boilers. These boilers required a new lining in the existing chimney. This required a crane to lift 33.5-m (110-ft) lining sections in the air, before sliding them down the existing chimney stack. This boiler room upgrade was the last one to be completed ahead of the December 2016 deadline.
Across all three sites, the condensing boilers were sourced from the same manufacturer to simplify ongoing maintenance.