Enabling faster returns to service when installing flooring
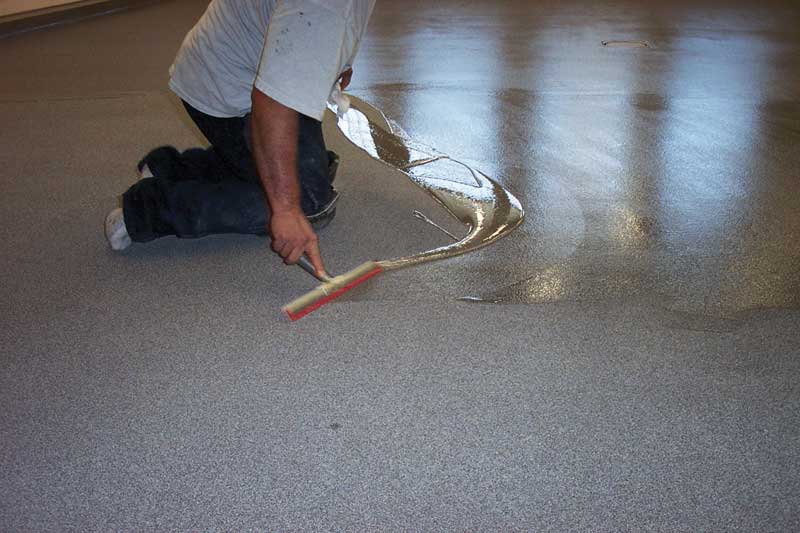
Intermediate coats
Between the surface prep and topcoating steps, the three flooring systems differ in application efficiencies in terms of the number of steps, material workability, and curing times. Conventional epoxy mortar systems require the application of primer, mortar, and grout coats before topcoating. MMA systems also use a primer, but they trade the mortar and grout coats for a single slurry coat, which is similarly applied before topcoating. Further, the MMA primer application is slightly faster than that of the epoxy mortar system. Urethane systems have the fewest steps, only requiring the application of a slurry coat before topcoating, as a primer coat is optional. Applications of the grout and slurry coats are similar among the three flooring systems, but the epoxy system’s mortar application is the most time-consuming and labour-intensive difference.
MMA systems require a primer to fill in imperfections in the concrete and assist with bonding to the substrate. Using squeegees and rollers, this application takes about a quarter of a shift for the 500-m2 cafeteria floor. The primer cures in as little as an hour, allowing crews to also complete the slurry application within one shift.
For a conventional epoxy mortar system, the primer coat also helps establish a smoother substrate and enhance bonding. The crew would likely take half a shift to prime the cafeteria floor. The primer needs to cure for 12 hours. However, it is also possible to apply the mortar into the wet primer, which speeds up the overall application. Still, many applicators prefer to wait for the primer to cure, due to the difficulties of working with a wet epoxy (such as potential splashes, tackiness, and timing considerations).
Next, the installers apply the mortar bed by mixing sand and epoxy resin, dumping that mixture into a screed box, distributing the material evenly with rakes and trowels, and power trowelling to leave a level, smooth substrate. The mortar typically combines more than 22 to 32 kg (50 to 70 lb) of aggregate with 4 L (1 gal) of resin. The result is a thick, heavy mixture that does not self-level and requires a lot of energy to smooth. This part of the epoxy system application takes roughly four to five hours to complete.
After the mortar has cured—usually overnight—installers apply the grout coat, which fills in the porosity in the mortar. Installers can apply this coat in about half a shift for the cafeteria floor using squeegees, hand trowels, and brushes. Once the grout cures (about 12 hours later), installers are free to apply the topcoat as described above. The floor will be ready for full service 24 hours after applying the topcoat.
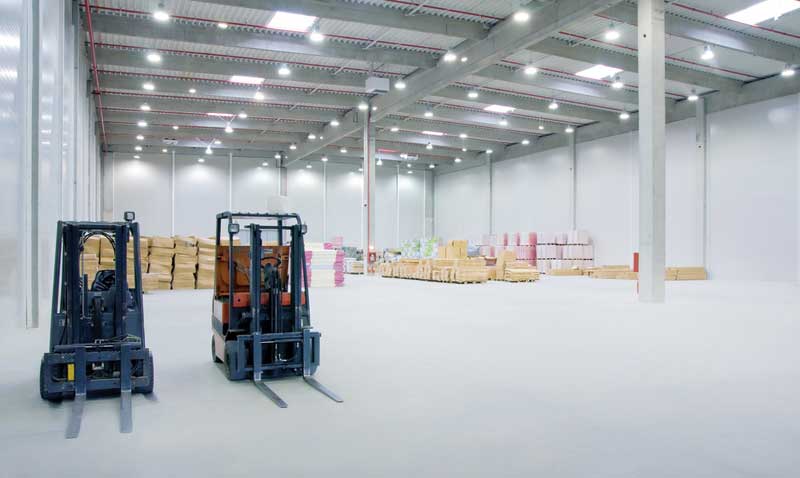
Both urethane concrete and MMA systems forgo the heavy mixing and tougher labour requirements for the installation of a mortar bed. They instead use a self-levelling, intermediate slurry coat, which is a mix of resin and hardener. However, the slurry solution is much less viscous than the mortar, as it uses less aggregate. Therefore, the resin-rich mixture flows and levels much more easily than the mortar mixture, reducing the energy required to apply this intermediate coat.
Using rakes and trowels, the crew can install a minimum of 93 m2 (1000 sf) of the slurry per hour. Therefore, installers may be able to complete the cafeteria floor slurry application in half a shift for either system. For the urethane concrete system, topcoating can start four hours later, and as mentioned, the floor can be returned to full service 12 hours after completing the topcoat. Those times are reduced to one hour for topcoating and two hours for returning to service when using an MMA system.
Repairs
Any flooring system in any environment inevitably gets scuffed, scratched, or otherwise harmed from use. Fortunately, it is relatively easy to repair a resinous flooring system without doing a complete reinstall. Unfortunately, that repair will always look like a patch. Installers simply cannot blend a repair into an existing flooring system—there will always be some difference in colour or sheen that defines the transition from the original floor to the patch.
However, the quality of the repair and how well it performs has a lot to do with the installer. This is why it is advisable for facilities to include language in their repair specifications requiring the contractor to have completed at least five projects within the last five years of equal size, scope, and complexity. Including this requirement helps ensure the job goes to a qualified contractor familiar with the flooring system and has the appropriate skill set for repairs. Another helpful tactic is to require contractors with third-party certifications. A facility may also consider identifying various hold points for approvals throughout a project so third-party inspectors can ensure a step such as surface prep, for example, is completed correctly before moving to the next stage.
Among the flooring systems discussed in this article, MMAs are typically the easiest to patch because they create a chemical bond with the substrate. Installers can often lightly prepare the area to be patched and then apply the MMA with confidence it will bond. Both epoxy and urethane systems rely more on mechanical bonding. Therefore, they require installers to sand or grind the repair area first so the substrate is prepared to accept a mechanical bond with the flooring systems.