Enabling faster returns to service when installing flooring
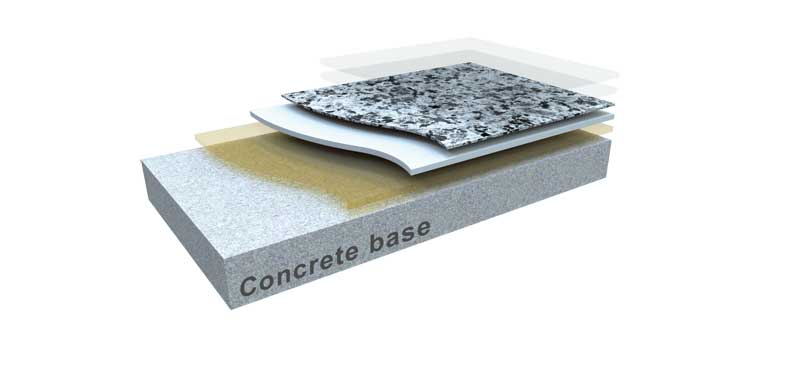
Reducing steps and time
One might use a 500-m2 (5400-sf) cafeteria floor as an example for comparing conventional epoxy mortar, MMA, and urethane concrete system installations. This size is a nice round number, and the employee welfare environment requires the typical properties desired in a resinous flooring system, including anti-slip characteristics, cleanability, and resistance to chemicals, abrasions, moisture, impacts, and thermal shock. Additionally, for any of the applications, the crew size would be about the same—approximately five to seven people.
When applying any of these flooring systems over green concrete, applicators must carefully measure the moisture vapour content of the concrete substrate to ensure it is within acceptable limits for the chosen system. For both conventional epoxy mortar and MMA systems, applicators must wait at least 28 days after pouring concrete to apply the flooring system. Even after this wait, they need to first test the substrate’s MVEs to ensure moisture has sufficiently diminished. If it has not, the installation will be delayed further—perhaps by only a day or two, or sometimes as long as another 28 days, depending on site conditions and the concrete mix itself.
The 28-day waiting period can be significantly decreased by choosing a urethane concrete system instead. These systems are highly tolerant of moisture, which reduces their required wait time to as little as three to five days. Therefore, applicators can install a urethane flooring system at least 23 days sooner than a conventional epoxy mortar or MMA system. Doing so could greatly speed up construction timelines and reduce downtime.
Urethane and MMA flooring systems offer enhanced application efficiencies, primarily due to their reduced application steps and faster curing times compared to a conventional epoxy system. Applications of all three systems are similar on their front and back ends, except for MMA, which may require the added step of setting up an odour-mitigation system. The biggest differences arise in the intermediate application steps, with epoxy systems requiring more steps and time.
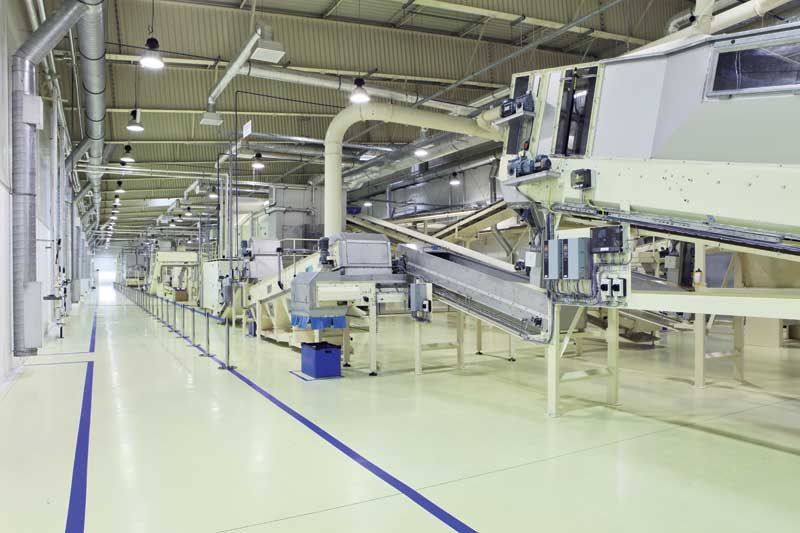
Containment setup
For MMA flooring system installations, heavy odours are a common concern. The systems emit noxious fumes during their installation and curing, and crews often need to contain those odours to ensure safety. Both urethane concrete and epoxy systems have lower emissions and rarely require a containment system during installations.
Establishing odour mitigation contributes to increased downtime for an MMA system application. To do so, applicators must set up a negative pressure containment system that contains and captures indoor air particles and odours to minimize air toxicity and reduce flammability potential. Workers first construct a physical barrier separating the work area from the rest of the facility and seal off any HVAC return air vents. They then set up and activate fans and high-efficiency particulate arrestance (HEPA) filtration devices to introduce clean air and exhaust dirty air. These steps all take time, adding to facility downtime and project costs. A reasonable estimate to set up a containment system for the 500-m2 cafeteria flooring installation would be roughly half an eight-hour shift.
Controlling the odours is especially critical in renovation projects, as the building may be occupied during the flooring installation. This may necessitate night, weekend, and/or holiday work, which could extend project timelines. The same may be true for new construction projects so flooring installers do not impact the health and safety of other trades working on the building.
Surface preparation
Preparing the concrete substrate for application of any of the three systems is essentially the same. Crews mechanically abrade the substrate to give it a rough, sandpaper-like finish that enables proper bonding to the flooring system. To ensure the concrete is free from defects and contamination, crews may cut, shot-blast, grind, polish, scarify, scrape, strip, and/or acid-etch the surface.
The surface preparation methods may vary depending on the condition of the concrete, but this example assumes one full eight-hour shift for the established five- to seven-member crew to prepare the 500-m2 cafeteria floor. The crew can begin subsequent steps immediately afterward.
Topcoating
The topcoating process is also similar among all three systems. Installers mix the materials in batches, pour them on the floor, and then squeegee, trowel, and roll them to a smooth, even finish. For the cafeteria floor, topcoating would take about half a shift to complete when using either an epoxy mortar or urethane concrete system. It may only take a quarter of a shift to apply the MMA system, due to the coating’s lower viscosity.