Employing wood in commercial buildings
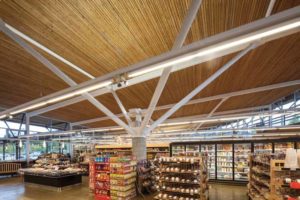
Photo © Derek Lepper Photography. Photo courtesy Allen+Maurer Architects Ltd.
The exterior wall panels had dimension lumber ledgers pre-installed to provide bearing for the five-ply CLT upper floor panels. At mid-span, the floor panels bear on a pair of glulam beams running either side of a central line of glulam columns.
The lateral system uses the exterior walls along the 34-m (112-ft) length of the building, with the panels connected by plywood strips nailed across the joints. For these tall panels to contribute to the lateral system, a creative interpretation of the Canadian Standards Association (CSA) 086-14, Engineering design in wood, was required (CSA 086-14 requires the aspect ratio and platform-framed approach when using the noted ductility values. However, it does provide an alternative approach with lower ductility if the criteria [such as aspect ratios, sliding of panels governing, etc.] are not met. This is a very conservative approach but does offer a path forward for alternate approaches to CLT structures [such as ‘balloon’ style construction] within the current code limitations.). Across the width of the building, elevator, and stair shafts contribute to lateral stability.
For lateral load distribution, a simple envelope approach was used, considering both rigid and flexible diaphragms. Diaphragm action was achieved by ‘stitching’ the floor and roof panels together using strips of plywood to bridge the seams—the same detail as used for the exterior walls. The revised foundation design is a raft slab, with short perimeter walls to create a crawl space. These concrete walls support both the CLT floors and exterior walls.
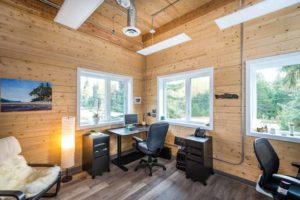
The building program is arranged on three levels. The first (ground) level is largely devoted to the sale of second-hand items, with receiving, storage, and sales areas, and seasonal storage is located on the second level (mezzanine) above. The food bank, counselling, and other community support programs operate out of offices and meeting rooms on the third level.
Since the mezzanine occupies more than 40 per cent of the floor area in which it is located, it is not considered a mezzanine, as defined in BCBC. Therefore, the structure is deemed to be three storeys in height. In the specific case of WCSS, the higher hazard retail-use had to be located only 1.5 m (5 ft) from the north property line. Vancouver-based engineering firm GHL Consulting devised an alternative solution that permitted the use of CLT within the exterior wall assembly in the locations where a two-hour noncombustible wall assembly was prescribed by the building code (see “Firewall Alternative Solution,” page 12). Had the mezzanine conformed to the BCBC definition, the building would been subject to less stringent fire performance requirements.
This is the first retail building of its type in Canada. It demonstrates the potential of mass wood construction to compete in this market sector, with comparable costs and enhanced environmental performance relative to ‘traditional’ steel and concrete construction. The wood solution is, in the author’s opinion, cost competitive and highly repeatable.
FIREWALL ALTERNATIVE SOLUTION |
For the three-storey structure of the Whistler Community Services Society (WCSS) in Whistler, B.C., Vancouver-based engineering firm GHL Consultants provided an alternative solution to address the exterior wall construction due to the proximity of the building to the property line, which is as little as 1.5 m (5 ft) in some places.
Given the higher fire load for the retail occupancy and the size of the fire compartment in this location, the British Columbia Building Code (BCBC) 2012 prescribes no more than 10 per cent of the wall adjacent to the property line be unrated window openings and/or wall area. The remaining (minimum 90 per cent) of the wall assembly must have a two-hour fire-resistance rating and be of noncombustible construction. The functional objective of this requirement is to limit the risk of a fire in the WCSS building spreading to the neighbouring property before emergency responders could perform their duties (e.g. fire suppression and wetting of nearby structures). This could be due to the fire spreading to the adjacent property through a window opening or unrated wall assembly or through ignition of the wall itself. The alternative solution permitted the use of cross-laminated timber (CLT) within the exterior wall assembly in the locations where a two-hour noncombustible wall assembly was prescribed by the building code. The solution demonstrated a non-loadbearing CLT wall could achieve the required level of performance. This was achieved using a char analysis and specifying mineral fibre insulation and a noncombustible cladding on the exterior side of the CLT. Similar measures could be used on future projects to address the same situation, if reorganizing the program or increasing the distance from the property line were not viable options. |
Jim Taggart is a Vancouver-based journalist who has written on the subject of contemporary architecture in wood for over 20 years. His credits include more than 100 articles for national and international magazines, numerous technical case studies for wood industry organizations, and the books Toward a Culture of Wood Architecture (2011) and Tall Wood Buildings: Design, Construction and Performance (with Michael Green, 2017). He can be reached via e-mail
at architext@telus.net.