Employing wood in commercial buildings
Whistler Community Services Society building
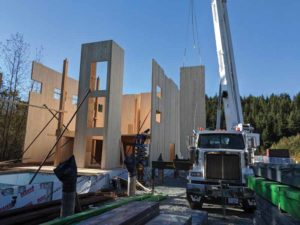
Photo courtesy Fast + Epp
The Whistler Community Services Society (WCSS) is a nonprofit providing a variety of social services to the residents of the Resort Municipality of Whistler, B.C. WCSS operates a food bank and a range of social and community programs, partially funded by a ‘Re-use It Centre’ that sells second-hand sports equipment and other donated items.
Rapid expansion of its retail operations and community services resulted in WCSS programs being spread across multiple locations, thus increasing operational inefficiencies and overheads.
With the complexities of a mixed-use program, including high-clearance storage areas and retail and office spaces, together with a desire to be close to the town centre and accessible by transit as well as private vehicles, WCSS concluded the best option for consolidating its operations was to construct a new building on a vacant site in the municipal works yard.
Due to the heavily trafficked, industrial nature of the site, the WCSS board decided the building should be constructed by using the traditional combination of a steel frame structure, with tilt-up concrete (structural insulated) panels for the exterior walls. AKA architecture + design headed the project’s design team and Fromme Engineering was the structural engineers.
The project went through the schematic design and design development phases, received both development and building permits, and was put out to tender as a construction management contract based on this steel and concrete structural system. However, it soon became apparent the concrete structural insulated panels (SIP) supplier was unable to meet the required construction schedule.
Whistler has long, cold winters with significant snowfall, restricting the construction season for concrete work in particular to the six months from May to October. Faced with this untenable situation, the WCSS board instructed the design team to investigate the feasibility of a mass wood alternative.
AKA architecture + design brought in a cross-laminated timber (CLT) fabricator (Penticton, B.C.) who recommended Fast + Epp design the wood structure. The first priority was to determine whether a wood alternative could be designed and delivered within the client’s tight time and cost constraints. From a cost perspective, the design team had a known tender price for the steel and concrete building as a benchmark.
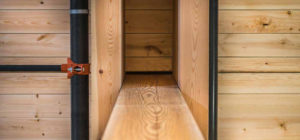
Photo © Andrew Doran Photography. Photo courtesy AKA architecture + design
In the end, the two solutions were almost identical in cost. Poor soil conditions meant large foundations were required for the concrete structure, and these could be substantially reduced for the lighter wood option. Since the CLT exterior wall panels could be loadbearing, it was possible to eliminate the perimeter columns required in the steel and concrete option. Additionally, interior finishes could also be removed in some places, as the CLT panels could be left exposed.
The mass wood structure is as simple as possible, with vertical CLT panels, a glulam post-and-beam interior frame, CLT ground and upper floors, and a glulam and CLT roof. The floor-to-floor heights had to be increased slightly, as services designed to run through open web steel joists now had to be suspended below the glulam beams.
The CLT panels were exposed in the counselling rooms and in the storage areas, where racks could be secured directly to the walls. For this project, the client was happy to specify a less expensive industrial grade of CLT, rather than an architectural ‘appearance’ one, and to leave building services exposed.
With only three months between the award of the contract to the required start date onsite, speed was of the essence. According to Carla Dickof, senior technical specialist at Fast + Epp, “The dimensions of the building as originally designed made it perfect for CLT.”
Both the height and width were just short of 12 m (39 ft)—the maximum length of a CLT panel that is currently available. It also happened to be the maximum permitted height of the building given the pre-existing development permit. The five-ply CLT wall panels were aligned vertically, running the full height of the building from grade beam to eaves, as in balloon frame construction. The elevator and stair shafts were constructed in the same way. This meant the panels could be lifted off the delivery truck and dropped directly into place by Seagate, the mass wood subcontractor. The wood at the elevator and stair shafts were also fireproofed with fire-resistant drywall.