Employing wood in commercial buildings
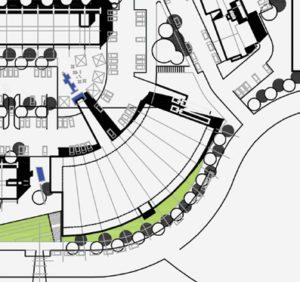
The NLT box beams have a consistent depth and continuous soffit treatment, but with variable joist spacing according to the length of span. The joists are regular 2×12 sections, used singly or doubled up for panels spanning up to 7 m (24 ft)—the longest available section. For the 10-m spans, 7 and 2-m (8-ft) sections were overlapped longitudinally and nailed together face-to-face in pairs to form beams. All the panels were finished with one layer of 13-mm (1/2-in.) plywood sheathing on top, while the spaces between the joists were filled with alternating 2×4 and 2×6 members at the bottom.
A 300-mm (12-in.) gap was left between panels to conceal sprinkler lines. These gaps are bridged by plywood on top and have corrugated cover panels beneath made from vertically staggered 2×3 members to match the main panel soffits. The panels use a total of 580 m3 (20,483 cf) of locally harvested dimension lumber and 1320 sheets of plywood.
The lumber was sourced from five regional mills to meet the demands of the schedule and to allow for competitive pricing. Shop prefabrication of the wood components also enabled the work to be carried out over the winter, providing off-season employment for carpentry crews. The simplicity of the design meant special tools or skills were not required.
The finished panels were hoisted onto the steel beams in the summer; there was no need for painting or electrical work. Sprinkler installers were able to kneel on the roof to drop the pipes in the provided slots, rather than working above their heads from scaffolding in the building. A second layer of 13-mm plywood was installed in the field to create a roof diaphragm.
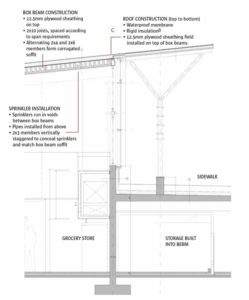
The panels did not contain insulation. Instead, continuous rigid insulation was laid on top of the field-installed plywood sheathing before the roofing membrane was applied. The vapour retarder is also located on top of the plywood sheathing. The maximum volume of the voids within the panels is less than the threshold for sprinklering of concealed spaces.
Since the lumber used has simply been cut from raw logs and not undergone any further processing, it has very low embodied energy and the benefits of natural carbon sequestration and storage within the wood fibre are maximized. It is estimated the roof structure contains 546 metric tonnes of embodied carbon. In addition to the tangible benefits of low-carbon construction and local employment, the form, materials, and organization of the building express the unique qualities of the site, and enhance the role the building plays as a social hub for the community of Salmon Arm.
Doubling as a retaining structure, the south wall of the building reconciles the change in level between the street and the future urban square below. The sweeping roof with its exposed Douglas fir soffit creates a warm ambience while the expansive windows admit abundant daylight and offer views of the surrounding mountains. The projecting eave soffit is protected by a flashing on its leading edge.
Perhaps appropriately for a grocery store, the design of Askew’s, in some respects, parallels the ambitions of the slow food movement. Just as slow food has promoted the virtues of quality and taste over the agri-business model of uniformity and convenience, the design of Askew’s puts the ecological, economic, and cultural sustainability of the community first.