Elevating building efficiency with roofing and insulation
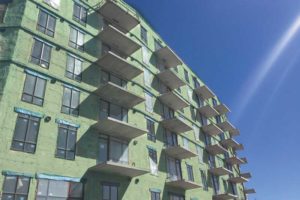
This means builders, architects, and engineers need to ensure new condominiums and apartments meet standards around affordability, energy-efficiency, and ultimately reduce environmental impacts. They also need to be comfortable, in terms of heating and cooling. Spray foam insulation in an internal or external assembly technique is efficient in the construction stages, and it enhances the overall resilience of building roofs, creating structurally sound, comfortable, energy-efficient living spaces.
In Toronto, there were 38,780 multi-unit starts in 2022—the largest number on record—with the majority being apartments and condominiums; while rental projects in Montreal represented 61 per cent of all housing starts.2
Recent MDU building projects worth mentioning: Le Viridi condos, a luxurious Quebec condo rental development in the Pointe-aux-Lièvres eco-district,3 and Mon Symposium Phase 2 in Lebourgneuf. The first phase comprises of 737 MDUs and phase 2 includes 166 units.4 The insulation for both these buildings was carefully considered and selected to deliver greater energy efficiency, comfort, and acoustical performance.
During the construction phase, both benefitted from an interior insulation method/technique where the three main properties of the building envelope were provided by one HFO spray foam insulation product that acts as an insulation, air barrier, and vapour barrier in a single application. With the quickness of installation, easier sequencing as the insulation and exterior finish can be installed at the same time—leading to cost savings for heating (winter projects) and major time savings.
Prior to the interior spray foam insulation application, it is essential to ensure substrate materials are within recommended moisture content ranges, especially in wood structures and this is critical for several reasons. These factors play a vital role in both the short-term effectiveness and long-term durability of the insulation, as well as the overall structural integrity of the building. For example, for spray foam insulation to adhere properly and perform effectively, the substrate, in this case, wood must be within a certain moisture content range which is 19 per cent for wood, in accordance with the building code. If the wood is too damp, the spray foam may not adhere properly, leading to gaps or delamination. This can compromise the insulation’s effectiveness in terms of thermal resistance (R-value) and air sealing.
Conclusion
Spray foam insulation stands as a versatile, effective, and structurally reinforcing material that caters well to the intricacies of complex large building roof designs. From seamless application and high thermal resistance to added structural integrity and moisture control, spray foam brings a multitude of benefits to the table. As the industry continues to push the boundaries of architectural design and engineering, embracing innovative materials such as spray foam insulation will undoubtedly be pivotal in realizing more sustainable, efficient, and structurally sound buildings for the future of Canada.
Notes
1 Refer to the Statistics Canada report by visiting www.150.statcan.gc.ca/n1/daily-quotidien/220209/dq220209b-eng.htm.
2 Visit the Canada Mortgage and Housing Corporation (CMHC) at www.cmhc-schl.gc.ca.
3 See project Le Viridi, condosleviridi.ca.
4 Learn more about Phase 2 of Mon Symposium, blancetnoircondosneufs.ca/projets/mon-symposium-phase-2.
Maxime Duzyk is the global director of building science and engineering with Huntsman Building Solutions. He has a background in architecture and has been in the spray foam insulation business for the last 13 years. Duzyk is involved with different building envelope committees and associations in North America such as CSC, SFC, SPFA, CCMC, and ULC Standards.