EIFS and sustainable design
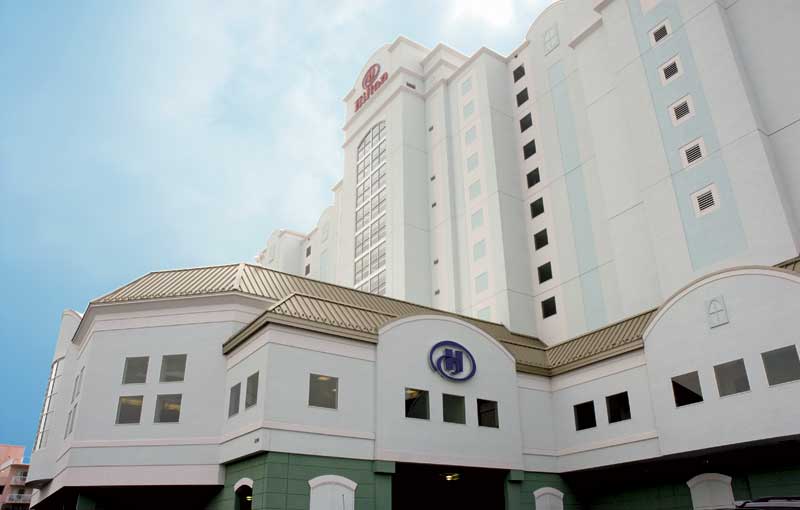
By Dale D. Kerr, M.Eng., P.Eng., BSSO, and Tom Remmele, CSI
Exterior insulation and finish systems (EIFS) can economically provide energy efficiency and reduced carbon dioxide (CO2) emission levels. (An earlier version of this article appeared in the August 2007 issue of The Construction Specifier, the official publication of the Construction Specifications Institute [CSI]). However, without durability as the cornerstone of sustainable design, most other ‘green’ attributes of products or systems are lost. Fortunately, with proper installation and integration, these cladding assemblies also offer long-term performance and durability.
From an architectural perspective, EIFS offer the ability to replicate almost any architectural style or finish material, coming in myriad shapes, colours, and textures. Low in cost and lightweight, they can be installed over existing buildings—this reskinning allows design/construction teams to reuse the original shell instead of demolition and introduction to the waste stream.
Further, a building’s overall energy performance and interior environment can be greatly improved by placing the insulation on the outside of the building. This strategy minimizes thermal bridging and helps keep the structural members at a consistent temperature, improving their expected longevity.
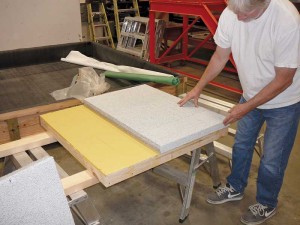
Images courtesy STO Corp.
By keeping the temperature of structural members constant, they are less susceptible to the movement and stress caused by temperature swings that could lead to cracking in concrete, masonry, and stucco walls. (In turn, this cracking could lead to water penetration and degradation, such as spalls or corrosion.)
Additionally, with sufficient insulation outboard of the structure, a dewpoint is eliminated and the potential for condensation from vapour diffusion is minimized. Mould, corrosion of metal fasteners and framing members, and deterioration of batt insulation and its R-value are a few of the potential effects of condensation that can be avoided.
Traditional, or ‘face-sealed,’ EIFS assemblies have typically consisted of five components:
- insulation board;
- adhesive and/or mechanical fastener to attach the insulation board to a substrate;
- reinforcing mesh for impact resistance;
- base coat to embed the reinforcing mesh and provide weather resistance; and
- decorative and protective finish coat.
While traditional or face-sealed EIFS were associated with some water intrusion issues in the residential industry, it is important to note the materials themselves were not the root cause. As buildings were made tighter and more energy-efficient, they became somewhat less forgiving of poor workmanship and water damage became more frequent.
Windows (and their installation) have also been a source of leakage into walls. This, combined with poor construction practices and tighter building envelopes, can affect durability, regardless of the cladding—brick, stone, EIFS, concrete, wood, or vinyl siding.
New generation of EIFS
In response to these water intrusion issues, building wraps or asphalt-impregnated sheathing paper and felts were installed behind EIFS to provide moisture protection to the wall structure. These wraps are relied on for providing water resistance, but they are often punctured and/or have the potential for tearing and mislapping during installation. As they are not fully adhered, they are also susceptible to billowing under wind load, which affects the wall’s pressure equalization performance.
Further, where sheathing paper, felt, or building wraps are used, mechanical attachment of the EIFS becomes necessary, as the specialized adhesives do not stick to sheet goods. Mechanical fasteners create thermal bridges, rendering EIFS less thermally effective. (The fasteners can cause ‘ghosting’ through the finished wall surface.)
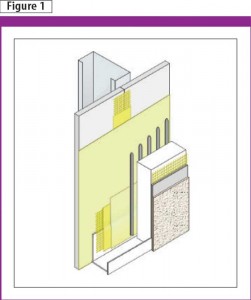
Newer EIFS products can overcome the limitations of traditional moisture protection and mechanical fasteners. These materials incorporate a fluid-applied waterproofing membrane and air barrier directly applied to the sheathing behind the EIFS wall covering (Figure 1). Rather than simply a cladding, these systems can be considered a complete exterior wall assembly, providing multiple building envelope functions.
Weather barrier
Most exterior wall problems are caused by water, primarily rain. When water gets into the wall system and wets the assembly’s materials, it can accelerate deterioration of those materials and create conditions conducive to mould growth, compromising indoor air quality (IAQ).
When the wall is designed to prohibit rainwater penetration, durability is drastically improved. In an EIFS wall, the lamina (i.e. base coat, mesh, and finish coat) acts as the initial defense against rain. Any joints in the exterior wall system, such as those between dissimilar materials, must be designed to resist rain penetration. Joints and flashing should be designed and constructed to slope toward the outside of the wall to prevent gravity flow of water inwards. Where appropriate, two-stage joints, drip edges, and capillary breaks should be incorporated to avoid inward water movement.
Water-resistive barrier
Incorporating a secondary means of controlling rainwater penetration—a water-resistive barrier (WRB)—can be beneficial in both preventing damage during construction, and keeping the building interior dry even before the lamina cladding is installed. In other words, this improves the wall’s long-term durability.
In the case of some newer EIFS styles, fluid-applied waterproofing applied to the substrate serves as the WRB; its purpose is to stop water getting past the lamina and insulation.
Newer proprietary EIFS products also provide an air cavity behind the insulation. Depending on the manufacturer, this may involve use of slots cut into the insulation and/or vertical ribbons of adhesive. Regardless, such air cavities provide a drainage space—should water get through the outer EIFS surface at a crack, it flows downward via gravity. Flashings installed strategically at floor lines and at the wall’s base direct the water back outside the wall where it cannot damage internal components.